Quality control (QC) laboratories in regulated environments are under increasing pressure to “get it right the first time.” That means streamlining the process of running routine methodology. This can be accomplished by a well-defined SOP that includes less human interaction with the instrument and the associated software. If the process is streamlined and we lessen human interaction along the way, we will reduce the chance that errors will occur.
Join this discussion to discover how the addition of smart LC systems and software, such as the Alliance iS HPLC System and Empower 3.8.0, can help you meet that goal, while improving your lab’s efficiency, and saving your lab valuable time and resources. Prepare your lab for the challenges it faces today and lay the foundation for your QC Lab of the Future.
Speakers:
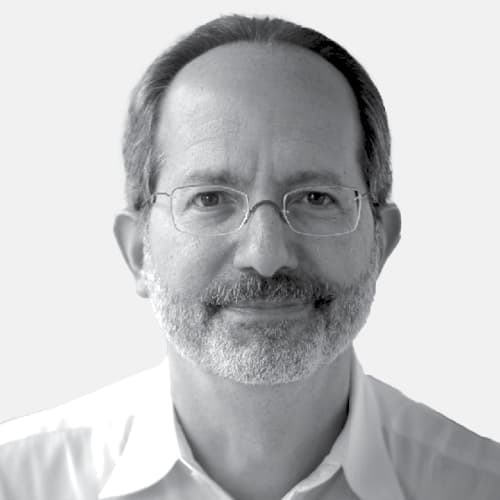
Neil Lander
Principal Product Manager Informatics Group
Waters Corporation
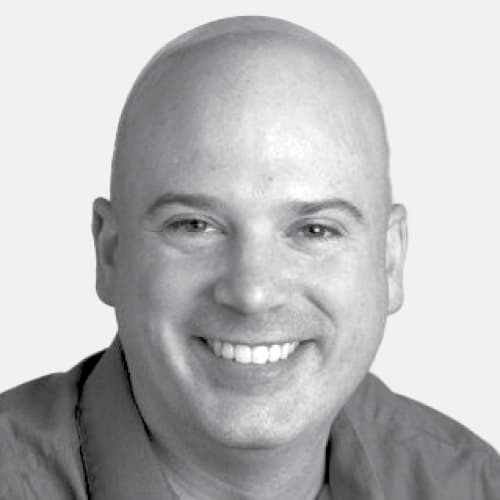
Patrick Flanagan
Principal Product Marketing Manager
Waters Corporation
This Summit Talk was part of Lab Manager's 2023 Innovating the Future Digital Summit.
As science and technology continue their advance, laboratories must evolve to stay current. To prevent time-consuming and expensive delays and overhauls, successful lab managers maintain a flexible lab that easily accommodates changes in equipment, process, and procedures. To keep up with the most recent standards and practices, lab workers must receive the required training and development. How can lab managers maintain a secure, creative, and productive working environment while also providing space for unidentified brand-new services and equipment?
Lab Manager recently hosted its 2023 Innovating the Future Digital Summit, where business leaders discussed the most recent advancements in lab technology, automation, and services as well as what lies ahead in the immediate and long term. Watch for free on-demand to gain knowledge and practical experience to help you create a lab that is optimized and future-proof.
Hello everyone and thank you
for attending Lab Managers innovating the
Future Digital Summit.
My name is Mary Beth Dena
and I'll be moderating this discussion.
Welcome to this session, reducing Errors in the QC Lab
with SMART Instrumentation.
Please send us your questions
or comments at any point during this presentation.
Our speaker will adjust these questions during the question
and answer session following their presentation.
To ask a question or leave a comment,
simply type your query into the q
and a box located on the right hand side of your screen.
We'll try to adjust as many questions as possible
during our time together,
but if we happen to run out of time,
I'll forward any unanswered questions towards speakers
and they may be able to respond to you directly if possible.
Additional resources
and a completion certificate
for this presentation are located on
the right hand side of your screen.
In the handout section, in the handout section,
you'll also find information about Lab Manager's Leadership
Summit in Denver, Colorado in May, 2024.
I'd like to remind you that the recording
of this webinar will be available for free OnDemand viewing
after the conclusion of this event,
and I would like to extend a special thank you
to our sponsors who support Allows Lab Manager
to keep these webinars free of charge for our readers.
So with that, I'd like to introduce our
speakers for this presentation.
Patrick Flanagan is a principal product marketing manager
and Water's QA QC division,
where he has worked for over six years.
He's currently responsible for product marketing
and product management activities
for Water's next generation HPLC systems.
He received his bachelor's in science degree from Worcester
Polytechnic Institute in biochemistry
and worked for 15 years as a formulation scientist.
Patrick began his career in Water's product management
department responsible for optical detection,
multidimensional systems,
and the Alliance Arc Premier System Arc, HPLC.
And the new alliance is HPLC system.
His recent work has been focused on the development
of innovative new products
for pharmaceutical qa, QC departments.
Q Neil Lander has worked for Waters Corporation since 1994
and has held a variety of positions including technical
support specialist, technical trainer, manager,
customer education, and currently principal marketing
manager and waters in the informatics group.
Neil provides internal support for Empowers CDS software
and is focused on developing laboratory software solutions
that help organizations achieve their scientific
and operational objectives.
Prior to joining Waters Corporation,
he was an analytical chemist
where he gained experience in both the cosmetics
and specialty chemical industries.
Patrick and Neil, thanks for joining us today.
Welcome, everybody.
Uh, my name is Patrick Flanagan
and I'm excited to speak
to you today about reducing errors in the QC Lab
with Smart Instrumentation.
Uh, this is a continuation
of 2023 lab managers innovating the future,
accommodating tomorrow's lab technology.
So, and what myself
and Neil Lander will talk about today is really the new
innovations from waters on how
to remove errors from chromatography.
So, just a little background
so you know, who's speaking to you today.
Um, so you already know my name, but it's Patrick Flanagan.
I'm a product marketing manager at Waters.
Uh, I've been at Waters for about seven years.
Uh, at this point I have experienced in almost every
chromatography system, waters, uh, cells, um,
and prior to waters I worked as, uh, both a QC analyst
and also as a formulation scientist for a number of years.
And I'll turn it over to Neil for a moment
to give himself some description.
Thank you, Patrick. Um, I'm Neil Lander.
I'm a, uh, product manager in the informatics
marketing group at Waters.
I've been with Waters a little over 29 years now, uh,
in a variety of different roles.
I started out in the field
as a technical support specialist in the New Jersey
and Pennsylvania area,
and then I moved to corporate headquarters,
which is in Milford, Massachusetts,
where I joined the customer training department.
And I was there for quite a number of years.
And then in 2015, I joined the Informatics marketing group
where I support Empower both externally with customers such
as yourselves, as well as internally with my colleagues.
Now, prior to joining Waters, I was an analytical chemist
and did quite a bit of chromatography in the cosmetics
industry as well as in the specialty chemical industry.
Alright, well, with our descriptions covered, I would like
to start introducing you to our innovations.
So I'll turn off my camera
so we can all focus on the presentation,
but in essence, as water sought to look into innovation
that would solve problems that matter for our customers, uh,
we did not do it in isolation.
So one thing we, we had
as a guiding principle was true innovation has
to solve business problems for our customers,
and it has to come from real problems from our customers.
So we had collaborations around the world
with numerous quality control labs
and analytical labs to truly cause
to truly solve these problems that matter to them.
Uh, and really everything you're seeing
today are about to see.
We really be reflective of things expressed
to us from customers and those types of partnerships.
And what we found through our research
and our interaction with customers was there were three
major bins and I, I go,
I'll subcategorize these actually later,
but three men categories where users were asking for help.
So one was with human errors.
So we're all human and we all make mistakes.
And when we sent out a survey
to about 56 quality control labs, with the caveat
of them having 25 systems
or more, we found that about 40%
of all method failures were due to just human mistakes, um,
preventable human mistakes, especially.
We also found that, um,
instrument poor performance accounted for an additional 22%
of run failures.
So that's somewhat hard to tease out
of actually human errors
because oftentimes human errors can kind of lead
to performance errors.
But to keep things simple, we can say that about 22%
of failures were caused by the instruments for performance.
The remainder of that, after
that 62% was actually just failures that were destined
to happen due to some kind of sample problem.
So the sample itself was faulty.
An additional survey out to customers found that about 74%
of customers struggled with system suitability issues.
So essentially trouble migrating
methods between instruments.
So users asked for our help in those parameters.
Now, to provide some metrics
to kinda start quantifying this problem, we found
through our conversations with customers that every time one
of these methods fails, on average, it took about four hours
to resolve and for every single sample run failure.
So this, we can go through the math later at the end,
very end of this presentation,
but this was a significant business problem that led
to operational inefficiencies for all of our customers,
let alone any investigation that needed to occur
because of these methods.
Failures, subdividing
even further, these were five other main categories kind
of branched out from that.
Were were things were really discussed
as being necessary to, for us to help them.
Uh, one was, again, reduction in errors in quality control.
We've covered that. Uh,
we also talked about smoother method migration.
Now tied to instrument performance though was just in
general reducing downtime.
So obviously time is money. Instrument uptime is also money.
You need to get as much analysis done as possible,
and you need instruments working to do that.
So anything we could do to assist in innovating to help
stop basically system downtime.
Another one, we simplified fleet management.
So this is going into a real systems
level thinking for a lab.
Oftentimes lab managers around the world need
to coordinate entire workforces to be able to be
as efficient as possible.
So they sought help from us to assist them with that.
And then again, somewhat related
to human errors is consistency.
So consistency of operation.
So guaranteeing that between analysts,
the same results are obtained.
So reducing variability,
and usually that's the variability in starting up
a system and shutting it down.
Uh, but helping customers get consistency of results.
Now, waters has always viewed ourselves
as an ally to our customers.
Uh, we seek to form these business partnerships and
and really treat it as such as a partnership.
And to us, any system we produce needs
to be an extension of that.
So we want this new innovation we're about to show you
to be a true ally to your lab.
And that's what the alliance I-S-H-P-L-C system really is.
It's another proverbial set of hands
to assist you in making sure
that your chromatography results are exactly what you expect
and are consistently performing at the highest levels
All to achieve certain results.
So obviously we're selling these to businesses.
You are in the business, uh,
you're looking to save time and money.
Um, so the way we're looking to save you time
and money is again, to reduce those errors by up to 40%.
We're looking for help you mitigate any potential risks
with various special features we have
that we'll talk about today.
We're looking to speed up method migration
by about three times, and we're looking to reduce the number
of operator hour training by about three times, essentially
by making a system that's easy to use.
So that additional training is not necessary.
We're also looking to improve performance to stop as much
as those 22% of run failures due to performance as possible.
Now in dealing
and talking with quality control labs,
oftentimes they're not looking for game changing innovation
around the science.
So you have legacy methods
and you need to get the same results for those, um, so
that you're not raising issues for your lab.
But that doesn't mean you shouldn't have improved
performance when within the parameters you want.
So we sought to improve things like carry over injection
precision and sensitivity
to truly help these labs obtain the results they need, all
with the goal of being your partner and trusted ally.
Now, as I said, the main crux
of this new alliance I-S-H-P-L-C system, uh,
which is shown here in the the center image, is
to be an error reducing system.
But none of that matters if we don't,
can't do the core performance
of analytical science that you need.
So let's start our conversation as we kind
of dive into the system to, to begin with core performance.
Now, first I'll just have you look into the, the photo here.
So this is what the alliance is HPLC system looks like.
It is a, uh, integrated system,
has all the components embedded into it.
So detection, sample management, pump column manager, uh,
everything you need to run the chromatography that you need.
If I break that down further looking at the very top,
you'll see that touchscreen.
So we're gonna talk a lot about the touchscreen today
because a lot of the innovations of this product
to help your QC lab are embedded into that touchscreen.
Now, to start us off though,
behind the touchscreen is a TV V based detector.
So it's wavelengths R 190 to 700 nanometers.
And we have some recent innovations
that really help control thermal stability
and we'll, we'll talk a little bit more
about how, why that's important.
Uh, but for now I'm just kinda laying kind
of setting the table, so to speak.
Now, in the touch screen, which is right in front of
that detector, are a number of things
that assist your core performance.
There are things such as guided diagnostics,
guided troubleshooting and guided service.
So all to enable a user
to get the best performance out of their system.
And if something does go wrong to problem, solve it
as quickly as possible to ensure
that you're always getting the best performance.
Also, to do that embedded into this our QR
coded service help.
So as you go through the workflows that are in the system,
if you truly are struggling, you'll be guided to a step
where there's a QR code that all you have to do is scan
with your smartphone and I'll
show you an image of that later.
Going down to the sample management,
the sample capacity here is a three plate system.
Um, so when we spoke to customers, we found the most
really extreme use case in these
labs was dissolution testing.
And for that testing, usually three plates was
the request we received.
Temperature range is four to 40 degrees C,
which is fairly standard for a chromatography system.
Uh, but what's unique for this system is,
is the stability of that temperature.
So water has been in the
chromatography business for a long time.
Um, we know from numerous interactions with customers
how we can make improvements
and the one of the things we found was
that the range was good, but we needed some more stability.
So what we've done with this system is we've improved
that thermal stability beyond anything we've done before.
Uh, that's a general theme.
As we talk about anything in the system involving
temperature, we've, uh, essentially stabilized everything.
Continuing that theme is the column heat cooler.
So that has a one column capacity,
but it's the full length that are typically used
for things like size exclusion.
So up to the extreme use case of 300 millimeters
and eight millimeter id, its temperature range is four
to 90 degrees C,
which is a larger temperature range than we have ever
offered in one module before.
All to make sure that you can run as many applications
as your lab requires In this setting, we also,
as they expressed, we have, uh, years
of experience in chromatography production.
So we again, know how
to improve certain parts from our lifetime experience.
So we've extended the life of many of the common fittings
of these instruments through rigorous testing to ensure
that you're gonna get the most robust system possible.
Continuing the theme of that robustness, if we go down
to the sample or the solvent management system,
it's a quaternary pump.
Um, and what we've really done
to improve things here is an improved check valve
and mixer, all designed for robustness
to ensure you get the best results and the best uptime.
It is, uh, a 10,000 PSI pump,
or really that's the, the extended range.
Um, so it's an HBLC system,
but the high end of an HBLC system
and a flow rate range of zero to 10 mils a minute.
So this system is more than capable
of doing any analysis typically performed in a quality
control laboratory, um,
or really any release testing with a kind
of UV based detection.
I've talked about some of this,
but we've also, again, we sought to improve that 20%
of failures that were caused by system performance.
So it's hard to quantify that,
but let's talk about some of the improvements we've done.
One is enhanced robustness.
So we have a new needle design
or a puncture needle, which is designed
to protect the needle from coring.
So again, enhancing robustness of your applications.
I mentioned how we have a new check valve design,
but again, designed for uptime, uh,
to basically have far less failures and results and,
and feedback we've received
so far from customers who've used
the system have been stellar.
We also have an enhanced method and migration support.
So this is a, again,
the temperature range is typically what's important there.
And this system is really be built to be able
to do an extended range, as I discussed,
at far better temperature stability than we've ever offered.
So if you're running this system in a cold environment
or a warm environment, it's stable enough to tolerate that
and give you read the same results no matter
what test you do around the world.
We also have a new optional mixer, um, which is really
for improved TFA and normal face, uh, baseline performance.
So this is one, again, it's an, it's an optional mixer,
but we found through the use with our beta testers
that people who have had, um, methods
that essentially were on the fringe of being successful
and whether they should be accepted, were actually found
that they didn't need to alternate any method parameters
anymore because this mixer alone stabilized things for them.
So again, every application's different.
We can't promise that for everyone,
but we have seen in significant improvement in
performance in these conditions.
We also have improved data quality.
So we've optimized our needle design
and also our wash presets to lower carryover values
and give greater injection precision.
So again, every application is different,
but some of the feedback we've received from
around the world so far has been a 10 x reduction in
carryover and, uh, very similar performance improvements
for injection precision.
So, as I said, every application's different,
but we're starting to get feedback like
that from around the world.
It's also built for serviceability.
So we have essentially built the system in such a way
that commonly, commonly serviced parts are easy to access
and make alterations to.
We've also provided key lighting in certain locations,
so it's easy to see what you're doing.
So again, the the goal being to keep great performance
and if anything ever goes wrong, to be able to fix
that core performance to get it back up
and going again as quickly as possible.
I talked earlier about that QR embedded, um, kind
of service help, which this is
just a visual depiction of it.
So essentially if you were
to dial into the system touch screen for looking for help,
you'll find QR codes at certain kind of workflow paths
and all you have to do is scan them with your smartphone
and you'll be taken directly to an article on waters.com
that will explain how to do the service that's required.
So again, all goal towards ease of use and enhance uptime.
Now I'm gonna shift gears. So having laid the foundation
for core performance
and talked a little bit about how to improve uptime,
I'd like to talk now about reducing risks.
Now, as we interviewed users around the world,
there was no one single thing that happened,
like all the time to create errors with methods.
It was really just a number of different kind of, you know,
death by paper cut kind of situations
where just numerous small problems kept
creeping into analysis.
So what we sought to do was to clean up as much of
that as we possibly could.
The first two things shown in this image are really color,
color-coded solutions.
So color-coded bottle flags and color-coded solvent lines.
The principle behind that is to control
your solvents in such a way
that users know exactly what to put where.
So not having mistakes in terms of dealing
with your solvents, adding them to the system,
or even just putting things in the wrong location.
We've also heard great feedback from around the world
that it really just helps the professional appearance
of the laboratory to have these.
A third one is tool-free fittings.
So one of the most common errors that did occur
that we heard quite frequently though was leaks
and specifically leaks at common touchpoints.
The most common of all
of them being when the column is added to the system.
So we now have, uh, extensively tested tool-free fittings
designed for usability, uh,
and tested throughout the world
to make sure people felt comfortable using them.
They also intuitively understood how much to tighten them so
that leaks did not occur.
So again, these are just two examples
or three examples of things embedded into the system
to prevent um, or really mitigate risks to prevent errors.
Well, that's just a starting point
'cause there are a number of other things embedded
into the hardware of the system.
So I'm gonna graphically walk you
through from top to bottom.
Um, many of these now.
So one, if you just look at kind of the bottle tray,
it's hard to tell from a small image,
but there's visual status indicators embedded into the
bottle tray that quickly communicate
to users exactly what's going on with the system.
So there's essentially a three color based system
where there'll be a bar on top that will highlight green.
If the system is operating perfectly, your method is going
and it's doing exactly what it's supposed to be doing,
you'll see a green bar.
So if you're walking in your lab, you just have to look over
and you'll immediately feel
comforted that things are going okay.
If it's a blue bar, it means that no method is running,
but all health metrics of the system are satisfactory.
So if you are a user who wants to use the system
and you see that color, you know it's ready for you
and there's no problems if that co if that color is red,
you know that you have to interact with the system
because something has gone wrong.
So immediately knowing when you need to stop
what you're doing and get your system back
up and going again quickly.
The other thing too, and it's relatively simple,
but the solvent tray is clear in the front
and what that allows is just very easy access to look, look
and see what your solvent levels are.
So, um, not having the risk
or lowering the risk of just your solvents running low
to preventing that error from occurring going down
to the TV detector and the touchscreen.
So the detector has self-identifying flow cells
and lamps, so it is now virtually impossible
to add the wrong part numbers to the system
as the system will stop you from doing so.
So preventing errors and configuring your system
and repairing it, it also has enhanced feedback, uh,
intuitive interface,
which I'll show you a little bit more in a moment.
And guided operation.
So the guided operation includes a guided shutdown,
a guided startup, and a guided priming workflow.
These are the most common things expressed to us by users
as being sources of variability of use.
So once the method is running, typically there's no errors
because the method set has already been written by someone,
but it was really the before that method that's running and
after it's running, which is
where most problems were occurring.
So we sought to help users there with solvent management,
uh, we essentially have a system that's always ready.
So there's a self priming peristaltic seal wash pump.
So this used to be a step
that users had to perform on their own.
So we've essentially removed this from their workflow.
Uh, we now take care of it, uh, on their behalf,
so less errors will occur
and more system robustness with the column heater cooler.
I already talked about the tool free
fittings to prevent leaks.
Uh, we'll talk more about the column heater cooler later in
terms of ways of doing column tracking.
Um, but for the core embedded system performance, we have
that leak protection for sample management.
We have, uh, self-identifying sample plates
with a barcode reader.
So it will now warn you if you've placed the wrong plate in
the system or you've placed the plate incorrectly,
which is an error we heard quite frequently from users.
We also have needle protection in
that there's vile bottom sensing now.
So again,
a common error we heard quite a bit was users inputting the
wrong settings and bending needles,
they're now protected from that.
Now here you're seeing just a picture representation
of the intuitive touchscreen, so
it's much more dynamic in in real life.
Um, but if you were to go dial into the,
like the second level of the system, so there's a,
a main screen with some key metrics
and then you'll enter into the system
and this is what you'll see.
And I'd just like to point out a couple things.
So the numerical things on the left
and right, those are the key health metrics
of your system always being updated.
So it's very easy
to get the most important metrics of your system.
The center is a map, uh, essentially showing users
what's happening with solve outflow that's mostly useful
for training new users.
Uh, as feedback we heard from virtually every customer we
interacted with who had to train was, it was very hard
for new users to understand
what was going on with the system.
So we provided this dynamic map to show them
and teach to explain the usability.
Essentially anywhere you see a circle
is an interaction point.
So if in the center of that kind
of map you can dial into the various settings of the system
and learn more on the left, there's a number of workflows
that you can be walked through.
So for example, in setting up the system, those kind
of guided workflows I I showed talked about briefly earlier
plots, you can go investigate more about the, the metrics
and the data you're receiving
and maintenance you can be taught how
to maintain your system through workflows.
Health will teach you how to repair your system
and the system one on the bottom, bottom left is there
to basically do emergency settings.
So if you ever had to do an emergency stop, that's
where it's located and the top right, I won't go into it,
but you can also customize your system.
But hitting in that top right button,
which you can name your system for example
and put your own personal flare on things.
Now the workflows are not complicated,
but there's numerous steps, uh, so that users only have
to digest so much information at once.
So this is just the very first screen
that users see when they hit the instrument startup method.
So there'll be guided step by step on exactly what to do
as well as how long to do it.
So we provide uh, numerical values that we suggest
but users can override them if they feel
like more time is necessary.
So it's a combination of walkthrough guidance with
an advanced user can alter the parameters if they wish.
Now everything I've talked about is just the core system
performance and the air reducing
that are standard to the system.
But since waters has an ecosystem of products, we're able
to level up the system so to speak and enhance it.
And that's by leveraging the ecosystem with Empower
and our column chemistries.
So at this point I'm gonna turn the presentation over
to Neil who will walk you through all the advancements
with that ecosystem.
Thank you Patrick. Some of the things that we're going
to talk about is looking at the uh, ecosystem
between Empower the system itself, the HPLC and the columns.
And these are some of the topics that I'm going
to talk about such as column tracking, pre-run checks to
avoid errors and saving time.
And uh, going back
to something Patrick talked about a little while ago,
that touchscreen interactivity, uh, how this interacts
with Empower itself.
Now one note I should make, uh, an important one.
In June of this year we introduced a new version of Empower
and that's 3.8 0.0.
Well, there are many customers around the world
that are on a variety of older versions of Empower.
So the question becomes what version
of Empower at a minimum do I need to uh,
run the alliance is and take advantage of the new features.
So provided that you are on Empower three feature release
four with Windows 10
and higher, you can take advantage
of the intelligent method translation application, uh,
the method matching
and the runtime checks, which I'm going
to talk about in more detail with the new version
of software that we released in June.
You have some additional capabilities which include column
tracking and history and also pre-run checks
and we'll get into those details as well.
So probably one of the most challenging things
for any laboratory,
but particularly for a quality control laboratory,
is moving a method
or migrating a method from an existing system
or a legacy system to a new system.
And this can be a very time consuming process.
So we've developed what we call the intelligent method
translator application.
I'm gonna show you in more detail how this works,
but this allows you to take an instrument method
and it's the instrument method in empower that defines
how are you're going to control the HPLC
and how are you're going to collect the data from the HPLC.
So we can take an instrument method from an alliance,
an arc, HPLC, an acuity arc,
and a number of different Agilent H PLCs
and have those instrument methods translated
into an alliance is instrument method so
that you can take advantage of the features
that Patrick was describing.
Now this is a toolkit application
and to access this application you would open a project
and from the apps menu select method translator
and it steps you through in just a couple
of clicks the ability
to translate an existing instrument method.
So this is what the opening screen looks like
and at the top there's a dropdown menu
and you can choose an existing instrument method.
And then on the left there's a translate
button that you can click.
So here is an example of an alliance instrument method,
I click translate
and it has now translated
that method into an alliance is instrument method.
The last thing we need to do though is give it a name,
enter any appropriate comments and save the method.
And then finally you do have the capability
of creating a report
and it's a PDF of the instrument method in a report format,
an easily readable report format.
Now let's talk about column technology
and how the column technology and empower software interact.
Some of you may recall that when we introduced the
acuity UPLC in 2004
and we have a whole family of instruments
around the acuity UPLC, we introduced a new type
of column technology called the EEC chord.
And when you install the column in the column oven,
the EEC chord on the end
of it had a little round magnetic disc
that was attached physically to the
outside of the instrument.
The instrument would read the information from that chip
that was in that magnetic disc
and then Empower would read the information from the
instrument and permanently store the
information about that column.
There was no human input needed, so column name,
serial number and a number of other pieces of information
that are critical to tracking that column were recorded
and permanently stored.
So now we're introducing a new technology called eConnect
and it's similar in that
when you install the column in the column oven,
you'll notice in the photo there is a column tag
and there's information embedded in that column tag.
So we put the column in, we close the oven door
and using a subset of RFID technology,
the tag is red.
Empower reads the information from the instrument
and stores a whole host
of information without any human input about that column
again including things like column names, serial number,
and a number of other fields.
So from a traceability standpoint
and when we're in a regulated environment,
there's no question which column was used
when you make an injection.
Now I am gonna show you some screen captures in just a
moment From Empower 3.8 0.0, we've expanded
what you'll be able to see in the configuration manager
section of the software.
When you look at the column information,
so there'll be a new field called column detect
and if it's an eConnect column it will say auto detected.
If it's an E chord it will say E chord.
And you also have the ability for manual entry
or the ability to scan a tag on a column.
So here we have a new instrument
with the first column installed on an alliance is
we go into configuration manager, which is
where the housekeeping of the software is done.
And on the left in the tree there's selection.
So by clicking on column we can see
what columns uh, have been used.
Now this was a brand new system one column.
So all you see is one column in the table
and while it's cut off a little bit, there are 13 fields
of information that are permanently stored in power
about this column.
So over time you can get the complete history of how
that column was used.
The alternate view is the sample set view,
and in this way we can see what sample sets were run on
that particular column.
Now this is very similar, I would say it's identical to
what you can see with the e chord,
but we took this a step further.
If you right click on a sample set
and select view as sample set,
it will take you into the project where the column lives.
So we no longer have to think about while I see a sample
set, I'd like to interrogate it,
but I'm not sure what project it was in.
A simple right click view, a sample set
and you're in the project and you can interrogate that data.
Now we talk about, and we mentioned column tracking a lot,
what does that really mean?
Well that can mean a lot of things to different people,
but essentially we want to track the performance
of the column and that's most likely a combination
of different measurements.
It could be the resolution between a critical pair of peaks,
it could be the tailing factor for a a critical peak,
it could be the plate count for that particular peak.
So we can track
that information over time either in a tabular format
or you can create a control chart at Empower,
which is just a visual way of looking at results.
And the nice thing about that is you can
look for trends in the data.
Well how do we do that with one of these eConnect columns?
This is just a simple example.
We're looking at the injections tab in a project
and what I've done here is I've added the column name
and the column serial number to the table.
So if I wanted to, I could select a particular serial number
and uh, I could then track that column's history over time.
And there are a number
of fields within the project that you can track.
There are up to six different fields
and you can add them to the view filters on a number
of the different tabs in the project to make it easy
to track which column you've been working with.
And again, uh, what we want
to do here is cut down on errors and save time.
So classic example is we get everything prepared,
the system is ready, we put the samples in,
we press the green button to start data's collected
and we come to find out that something went wrong
and now we have a set of data that we cannot use
and we have to write up a report as to why we cannot use it
and then go and investigate what the problem is
and take corrective action.
So the combination of this version of Empower along
with the alliance is prevents that from happening.
So when you go to click the green button in the run samples
window, it looks at a whole series of different things
and if anything is wrong
and I'll explain in detail what that means, it's not going
to start any injections.
So what do the pre-run checks really consist of?
Some of which, uh, Patrick described, you know,
is the plate in, is the plate installed?
Is it in the right position?
Is the service up to date
or have we exceeded a date for service or calibration?
Have I installed the correct column in the column of it?
Has the mobile phase expired
and have I selected the correct instrument method
for the system configuration?
So here we take a look from the touchscreen
of the alliance is,
and this is where we can enable all
of these different pre-run checks
that will then work in conjunction with Empower
Runtime checks consist of
are the vials in the right position,
is there a leak detected?
Is the mobile phase solvent level sufficient
and is the wash solvent level sufficient?
And here again through the touchscreen of the system,
we can see where we can enable these various checks.
So if we press that green button in the run samples window
to start a sample said method
and an error occurs, this is the generic message
that you will see on the screen
and you'll be encouraged to look at the message center
to see the very specific error that has occurred.
Let's look at some examples.
So first of all, here's a look at the instrument method
for the alliance is, and in particular we've clicked on the
column and we're going
to select which column is required for the method.
We pick the column from the list
and it is now part of the instrument method
that this is the particular column that should be used
If we install the column in the oven.
And the alliance is reads the tag
and that column does not match what's
specified in the method.
This is the message that you're going to get,
essentially telling you the wrong column has been installed
in the oven and preventing you from running.
It will not start the first injection.
Here's another example.
The solvent for the mobile phase has expired.
Certainly we don't wanna use use mobile
phase that has expired.
This will check that date
and again, if we've exceeded that date,
it's going to flag it.
The sample set will not begin.
What if the level in the bottle is too low?
Same thing, we have a long queue of samples.
It's going to require so much solvent in
the mobile face bottles.
If it's too low, we don't wanna start
because that will cause trouble as we go
through the sample queue.
And what if a vial is missing?
This is one of the classic things.
So the instrument will check to make sure
that the vials are in the correct positions
as per what's in the queue.
And if it's not there you'll get this message
and again, the sample set will not begin.
So in addition to the features specifically built
for the alliance is there are a number of other new features
that were released in this new version of software.
I'm not going to go through this list,
but I will mention one thing
that's been on everyone's mind for the past year.
It was a year ago today
that the USP revised chapter 6 21 on chromatography.
So we've updated the calculations
and the terminology so that you can comply
with those changes to USP chapter 6 21.
Now I'd like to talk to you about something called
system monitoring.
System monitoring is a cloud-based application
that works in conjunction with empower.
So most organizations have many instruments scattered
around different laboratories
and maybe in different geographical locations
and it's very difficult to manage all of those instruments.
What the system monitoring application will do is
any chromatographic instrument that is connected
to the Empower Enterprise environment can be monitored
through this application.
And you can see in the upper left hand corner
each instrument will appear as a tile
and there's colors associated with it.
So green running blue idle
red means there's a problem
and you can click on any one of those tiles
and you can get more information about the
status of that instrument.
What we've also added recently is the ability
to schedule time on that instrument.
So again, it's any instrument that's hooked up
to the Empower enterprise environment,
whether it's a waters lc, whether it's an Agile
and gc, any
of those instruments will show up in this particular
application making management
of all the chromatographic systems a lot
easier in the laboratory.
Patrick, back over to you.
Alright, well I hope everyone enjoyed that, uh,
I guess quick tour of the system
and uh, all the ecosystem surrounding it.
So just to summarize and,
and I'll go through these numbers
that you're obviously looking at on the, on the slide
to moment, but our, you know, our major goal was to be
that ally, the proverbial set of hands
as I described earlier.
Um, we've done that through trying to mitigate
and stop 40% of the user errors.
We're doing that through the various features
that make using the system more intuitive.
And then as Neil described, also combining that with
features that stop users from making mistakes
or being able to run the system at all
if they're making mistake.
And also, uh, flaggy if their mistakes made during the run.
So all those things
to prevent you from essentially making any errors
and having chromatography problems.
Um, we've also tried to simplify fleet management
as Neil just talked about with that system monitoring tool.
We've tried to improve your core performance
through all those features to improve the robustness,
the uptime, um, the performance with needle injection
and detection systems.
And we've also improved your ability to do method migration
through that intelligent method translator app, combining
that with better thermal stability control.
So you got the same results anywhere in the world.
So really everything is designed to make the operations
of your lab better.
So that's great, right?
Innovations are are really cool and neat,
but they don't matter unless they're
providing you business value.
So every organization's different, uh,
but we're gonna walk through just some relatively simple
math and we're gonna make some assumptions.
So if we make some assumptions that the, the,
the average large organization has about 10 quality control
labs and from our surveys of those labs, we find
that on average they do about two hours per week
and it takes about four hours to resolve those errors.
If we also assume about four methods are migrated per year,
which is from, you know, my conversations with most
companies, that's actually pretty conservative,
but if we assume that we assume one new operator per month
and we assume it takes them at least 24 hours to train
and the average salary of an analyst is about $35 an hour.
So again, a lot of assumptions embedded in there,
but if we make those assumptions which are fairly realistic,
we can now we can do some math.
So if we're reducing 40% of common errors in operation,
that saves about 1700 operator hours per year
and that's a total cost savings
of about $60,000 in operator costs.
By enabling that method translation to occur faster
and more seamlessly,
we've saved about 107 operator hours per year at a savings
of around $4,000 in operator cost.
And by making things more intuitive with guided workflows
and more dynamic help, we've enabled training
to occur three times faster,
which saves almost 2000 operator hours per year at a savings
of around $67,000 in operator costs.
So all of that adds up pretty quickly
to almost 4,000 operator hours saved
and almost $130,000 in operator costs, uh,
saved by your company.
So you can see the value of this system is not just,
you know, frustration and preventing, you know,
user frustration and mistakes, it's also valuable
to your business bottom line.
So at that I will thank you very much
for your attention today
and uh, I will come back on screen
to answer any questions that we have in the chat.
Okay, great. Thanks very much Neil
and Patrick for a wonderful presentation.
So at this point we are ready to move into the q
and a with our audience.
Again, for those of you who may have joined us late,
you can send me your questions
or comments by typing them into the q
and a box on the right hand side of your screen.
I'd also like to remind you to take this opportunity
to look at the handouts section on the right hand side
of your screen for supporting information for this event.
So Patrick Neil, thanks again.
Let's, uh, go right into the
first question from the audience.
Does the method translator app modify method parameters?
So the short answer to that is no.
Um, the longer
or slightly longer answer is, um, it doesn't modify anything
that would be a compliance trigger.
So it just translates those values.
If it red flags something as maybe of concern,
it will actually highlight that section for you
as a user interaction point.
So we as a company won't change those parameters.
We do nothing that could alter your compliance
and um, it's only a translation essentially,
Essentially. Great,
thank you. Let's move on to the next question.
This one says what detectors are available?
So standard to the system is a TUV detector.
Um, we know from our user research with Quality control labs
that that accounts for about 70% of the use cases.
Um, so the vast majority now that said, there are users
around the world who wanna do other detection choices.
So in the instrument there's an inject start functionality
which allows you to trigger other, you know,
detectors and third party equipment.
So the system has that functionality.
So if a user wants to add other waters detectors and
and things of that nature that can be triggered
by inject start, uh, they can,
they can use basically those things through that means.
Wonderful, thanks. Okay, thanks.
Let's move on to this next question.
Can I use existing columns
or does the system require new columns?
So I believe that question's really asking about eConnect
and whether this only uses eConnect.
So if a user wants the functionality to
do the column tracking that Neil described,
they would need an eConnect column now.
But for core chromatography
and to just do whatever methods you used
to run, you do not need that.
So the system will run any standard column,
anything you're used to running on an HBLC,
it's capable of performing.
It's just that very specific feature requires
eConnect columns.
Great, thanks. There's another question under that one
that says, how is the system shutdown workflow different
than the shutdown and and power?
So it's basically the same functionality
but more on demand.
So Empower basically is triggered, I mean it's triggered
by an an event, um,
where the touchscreen functionality is really just there to
the user can control it a little bit easier.
Uh, and we imagine it's being used when it comes down
to shutting down the system for a longer period of time, uh,
for due to inactivity or if maintenance needs to occur.
So it's really the same basic idea
but triggered differently, um, for user convenience.
Thanks. Let's move on to the next question.
Does Empower create a new record
for a column when it is moved from one HPLC to another
and how can you track what systems the
column was connected to?
Great question. Um,
and the answer to the first part is no.
Um, there's only one record per column.
Now whether it's an eConnect or say an Ecor column.
So even if you were to move the column
to a different instrument for some reason, um,
the column is still identified by its tag, which includes
that name and serial number
and all of those other fields that are, that are captured.
So it doesn't matter how many instruments, uh,
it's been connected to, there's basically
one record per column.
With regards to the second part of the question,
if you go into the project,
and I'll go back to the injections tab
'cause that's what I showed in the presentation,
you can make a custom view filter that shows you, you know,
which CHROMATOGRAPHIC system was used to make that injection
and then add to that view filter the column information.
So you can very easily see what the use of the view filters,
you know, what system did I use with this column.
And if I want to go beyond just one project,
you can go into Confi Configuration Manager,
highlight multiple projects, right click open
and that'll open up a global project view
and you can make the same type of view filter
to look across multiple projects to say, okay,
with this system
and this column, you know, what data did I did I collect?
So it it's fairly straightforward to get
that kind of information.
That's a good question.
Okay, wonderful, thanks. I think we have time
for a couple more questions.
We currently have Empower 3.6 0.0
and would like to know if it is possible
to flag the instrument when it has exceeded its maintenance
or calibration date.
Okay. Yes. You, you can do this.
Any, any version of Empower has the following capability.
So if, if you didn't have the Alliance is you had a
different instrument, uh, whether it was an Acuity UPLC
or some other instrument, if you go into Configuration
Manager and you go to the node, um,
and in an, in an enterprise environment, we,
we hear the term lace boxes, uh, which is basically
the acquisition server
that the instruments are physically connected to.
So you go into the properties of that node
and you go to the instrument tab,
you'll see all the instruments that are connected to
that node or a place box,
there is a next service due field.
So you can populate that field so that when
that date is reached you could potentially block users from
using that instrument.
Um, there's a privilege in Empower,
everything's privilege based,
so there's a privilege in Empower that would allow
or disallow our user to operate
that instrument once it exceeds that date.
So if I don't have the privilege to do that
and I try to go in and use that instrument,
it's gonna lock me out of that instrument
because I've exceeded that service date.
So you can do that on, on any of the, uh, versions
of Empower with, uh, any chromatographic system
that's connected to Empower.
Okay, great, thanks. I think we have time
for one last question.
What is the easiest way
to compare results from my previous
system to the new system?
Ah, okay. So you've migrated from an alliance
to an alliance is and you wanna compare results.
All right, so two part answer, uh, based on
where, where are the results?
Are they in one project or are they a different project?
So if they're in one project, um, you could go
to the injections tab in the project, it could go
to the channels tab in the project, you could select the,
uh, the raw data or you could go to the results tab
and select the final results, uh, from the two systems
or results that were generated by the two systems.
Highlight them right click
and you have the option of going to the review area
or the compare area if the data's in different projects.
Something that I mentioned earlier is you can search across
projects by going into Configuration Manager highlighting
the projects right click Open that opens up the global view.
You can then go to the results tab
or the raw data tab depending on what you want to compare,
highlight the data from the two different systems,
right click and select Compare
and that will open up a window that will allow you
to make an easy visual comparison
of the data collected on the old system
versus the new system.
Okay, wonderful. Thank you both very much.
You're welcome. Yeah, thank you for the questions.
This brings us to the end of this webinar.
On behalf of Lab Manager, I'd like to thank Patrick Flanagan
and Neil Lander for all the hard work they
put into this presentation.
And I'd like to thank all of you
for taking time outta your busy schedules to join us.
A reminder that all of the presentations from the Innovating
the Future Digital Summit will be available
for free on demand viewing.
Please watch your emails
for a message from Lab Manager once
these videos become available.
Once again, thank you to our sponsors, poly Science
Waters Corporation, PerkinElmer xyx, Milliport Sigma, Tecan
Molecular Designs Lab, vantage, Zare, and Agilent.
Their support allows Lab Manager to keep these events free
of charge for our readers.
Please be sure to tune in
for our next presentation at 12:30 PM Eastern
Synthesis Automation with Cynthia and Simple.
Ken, for more information on all
of our upcoming on-demand webinars,
or to learn more about the latest tools
and technologies for the laboratory,
please visit our website@labmanager.com.
Thank you all for being part
of our Innovating the Future Digital Summit
and we hope you have a great day.