Recognizing Hazards in the Lab
Building a safe lab environment requires systems, collaboration, and organizational commitment
Laboratory safety is a critical yet often misunderstood aspect of research environments. Here, Julia Means, lead occupational safety specialist and member of Lab Manager’s lab safety editorial advisory board, emphasizes that recognizing and mitigating hazards requires more than individual vigilance—it demands systematic, organizational approaches.
Q: What do you wish more people knew or understood about laboratory safety?
A: Recognizing hazards in the lab isn’t intuitive. It is not something that innately happens on the first day in the lab or because someone has spent years in the lab. Recognizing hazards and understanding how to effectively eliminate or control hazards takes established systems and active problem-solving at the organizational level.
Labs cannot rely on a single individual’s experience or perception of the risk to keep them safe. The lab must implement management systems to ensure safety is integrated into their operations. When safety is integrated into the production side of the lab, the gains and efficiencies can be substantial. Integrating safety into production not only protects the people and property but it improves reliability of the research and outcomes.
Q: What’s the biggest lab safety-related lesson you’ve learned in your career so far?
A: The biggest lab safety-related lesson that I have learned is that every organization and every lab is different. My job is to always remain inquisitive and to discover how the work is being done in each lab and to determine what their ultimate goals are. The real way to drive change in safety is to understand the processes, the people, and the needs of each organization. Then and only then can we help set goals for improvement that are manageable and achievable for long-term success.
Q: What does a day in the life look like for you as a lead occupational safety specialist?
A: My days are always different. I am constantly learning about the things that inspire and drive other professionals. I partner with experts in their field to really learn about the goals of their research or work, understand lab’s specific processes, and assist them in achieving their goals safely. I work in the field to observe and collaborate with researchers and operations to learn about what they do and what they need. When I am not in the field, I am working closely with my colleague researching, writing, and customizing resources to help apply safety principals to real-life situations.
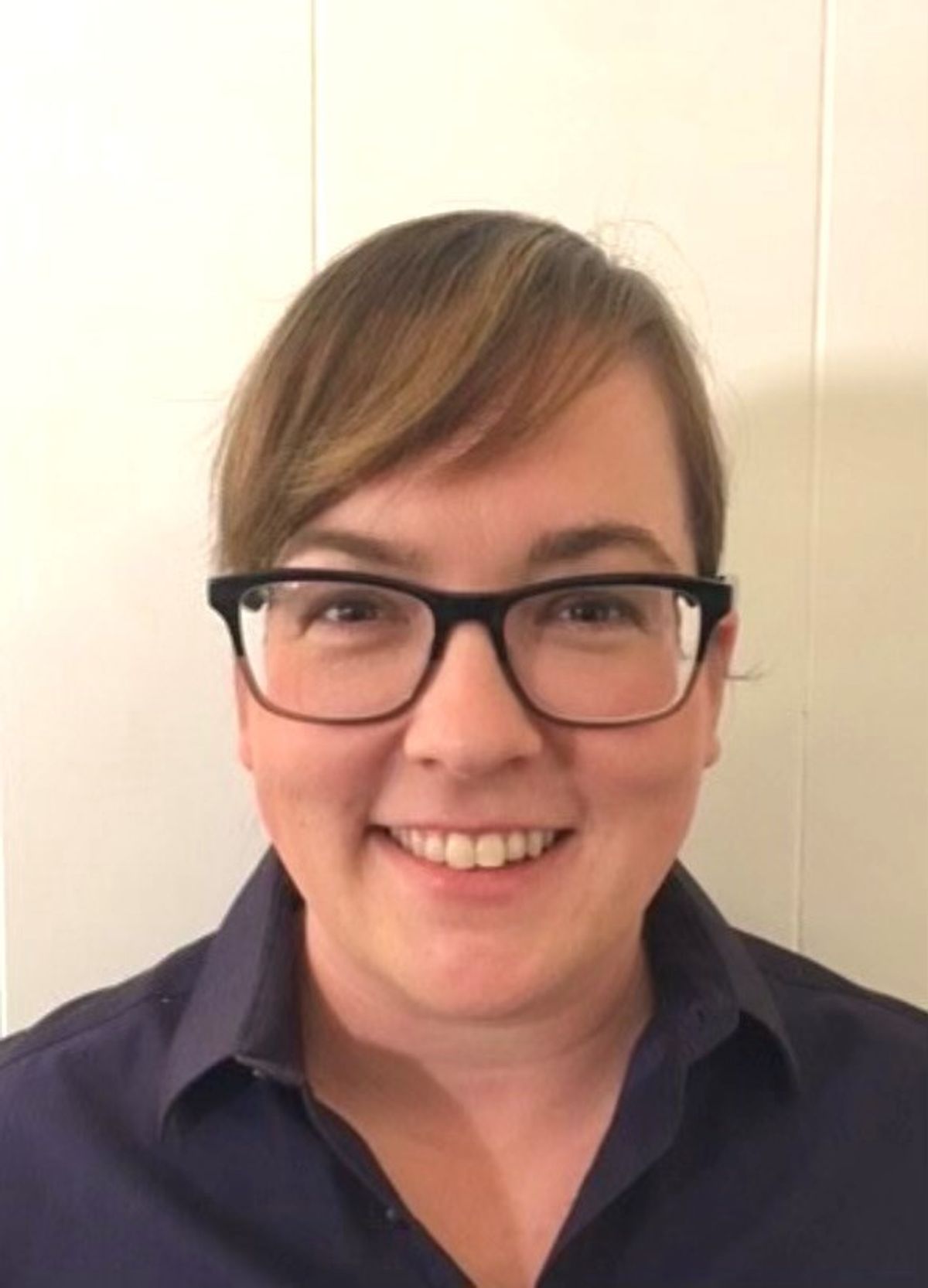
Q: What advice can you give someone looking to establish a better culture of safety within their laboratory?
A: Leadership must invest in safety and ensure it as an organizational value not just a priority. Our priorities change depending on internal and external pressures, while our values remain at the core of what the organization does no matter the challenges they face. If leadership does not value safety and production priorities are higher than safety, the culture will never fully integrate safety into their operations.
Q: What do you enjoy doing outside of work?
A: I coach my daughters’ year-round competitive softball team. When I am not at work, you will usually find me and my family on a softball field somewhere. While we dream of having a free weekend for camping, those are rare to come by. Either way as long as I am with my family and my dogs, I am enjoying life.
Julia Means is a certified safety professional (CSP) with over 16 years of experience in occupational health and safety with a strong focus on industrial safety. Julia’s experience includes managing in-house safety programs and providing outside consultative services to higher education, public authorities, and private industry clients. She works collaboratively with leadership, operations, researchers, and educators to understand their needs and implement achievable solutions to fit their unique challenges. For the last four years, Julia has applied her knowledge and experience to lead the design, implementation, and delivery of industrial safety services at the University of California at Davis, where she acts as the lead general and occupational safety specialist.
In addition to her work at UC Davis, Julia heads two safety workgroups for the University of California system. Julia is the current chair of the UC Occupational Safety Workgroup. This workgroup is comprised of representatives from 10 campuses, five healthcare systems, and one national laboratory. Recognizing the unique challenges that campuses face with electrical safety, Julia founded and leads the UC Electrical Safety Program Workgroup. Both leadership roles allow Julia to collaborate with safety professionals within the UC system and other institutions to strategically tackle some of the toughest safety challenges facing higher education.