This webinar will be presented by Larry Wong, who in his 49 years in the EHS field has visited over a thousand laboratories—not only as a Cal/OSHA compliance inspector, but also as an EHS Director with the goal of improving the culture of safety in laboratories. We will not only discuss some of the most common OSHA violations, but also address some health and safety requirements which are frequently overlooked in a laboratory environment. This session will also offer suggestions on how to improve the safety culture in the laboratory.
Learning Outcomes:
1) Frequent health and safety violations found in laboratories
2) Obscure OSHA requirements laboratories frequently are not in compliance with
3) How to survive and OSHA inspection
4) How to improve the safety culture in the laboratory
Speakers:
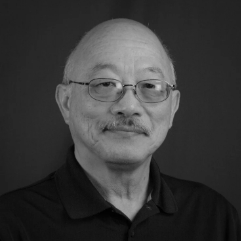
Larry Wong
Adjunct EHS Instructor
UC Berkeley’s School of Public Health
This Summit Talk was part of Lab Manager's 2023 Safety Digital Summit.
Lab managers are tasked with keeping their lab staff safe, which means anticipating and mitigating various hazards around the workplace. Heavy equipment, dangerous chemicals, sharp instruments, and mental stress all present varying levels of risk. Managers must develop a comprehensive lab safety program to protect their personnel, equipment, and products—this will help prevent tragedy, as well as benefit a lab’s bottom line by decreasing product loss and costly downtime. What are the steps needed to develop an effective safety program, and how can managers convince their staff to achieve compliance?
Lab Manager recently hosted industry experts who spoke on these issues and more during its Safety Digital Summit. Industry experts shared their personal experience and stories to help you achieve a safer lab. Learn the steps you need to take to properly assess levels of risk in your lab, keep your equipment in working order, and recognize signs of distress among your staff and yourself. Watch for free on-demand to gain the valuable guidance you need as you improve your lab’s experience and create a safer environment.
Hello everyone. Thank you for attending Lab Manager Safety Digital Summit. My name is Michel, and I'll be moderating this discussion on OSHA considerations for lab safety. Please send us your questions or comments at any point during this presentation. Our speaker will address these questions during the q and A session following his presentation. To ask a question or leave a comment, simply type your query into the q and a box located on the right hand side of your screen. We'll try to address as many questions as possible during our time together. However, if we do run out of time, I will forward any unanswered questions to our speaker and he may be able to respond to them directly. If possible, lab manager would like to announce that the admission of our Safety Excellence Awards are now open and available for entry. Please see the handout section for more information and a direct link to our Safety Excellence Awards page to learn more. Additional resources and a certificate for this presentation are located on the right hand side of the screen. In the handout section, I'd like to remind you that the recording of this webinar will be available for free on-demand viewing. Following the conclusion of this event, I would also like to extend a special thank you to our sponsors who support allows Lab Manager to keep these webinars free of charge for our readers. So with that, I would like to introduce our speaker for his presentation. Larry Wong has worked in the e h S field for 49 years. In 2019, he retired as the associate e h S Director for the University of California office of the President. As Associate Director, Larry has provided technical and administrative guidance to 10 uc campuses where he is inspected and reviewed the h s program of several hundred uc laboratories. Before coming to uc, Larry was a section chief with Cal e p a. Prior to that position, he was an industrial hygienist with Cal osha. Larry is a certified industrial hygienist and is an American Industrial Hygiene Association fellow. He's the past chair of the A I H A Lab h and SS committee. Larry has developed several Cal OSHA regulations and is the primary author of the A S T M H and SS Training Standard. He's the graduate of uc, Berkeley, and is currently an adjunct e h s instructor for US Berkeley School of Public Health Labor and Occupational Health Program. Larry, thanks for joining us today. Uh, so welcome to OSHA consideration for Laboratory health and safety. For this session, we'll discuss the primary OSHA regulations, which are applicable to laboratories. From there we'll go over several common lab health and safety violations, which I have found over the years. We'll look over a couple of obscure and often overlooked OSHA regulations, which are applicable to laboratories. We will then go over some suggestions on how to survive an OSHA inspection, and we'll finish off with some Larry recommendations on how to improve the safety culture in your laboratory. OSHA is a federal Ag agency within the US Department of Labor. Their primary mission is to protect workers osha Promulgates Health and Safety Regulations, which are entitled 29 of the Code of Federal Regulations, which are abbreviated as 29 C F r. OSHA enforces compliance through workplace inspections. Their jurisdiction is over private sector employees. OSHA does not cover state or local government employees. When the Occupational Safety and Health Act of 1970 was passed, one of the primary goals was to encourage states to develop their own health and safety program. OSHA approved state programs must be at least as effective as OSHA in regulations adopted and in how they conduct inspections of places of employment. If you look on at the map on the slide, the darker blue colored states in Puerto Rico are approved state plans, which cover private and state local government places. The very dark blue are six states plus the Virgin Islands, who have an approved state plan to only cover state and local government workers. The light blue states and territories, which have no state plans, and these states cover the health and safety for private sector employees only. Some states with no state plans may adopt their own health and safety regulations and address health and safety for state and local government employees. Besides the OSHA regulations in 29, uh, C F R, there is the general duty clause in which the OSHA Act entitled 29 US Code of uh, regulations section, uh, 6 54, uh, section five A one. This requires each employer to furnish each of his employees employment and a place of employment which are free from recognized hazards that are causing or likely to cause death or serious physical harm to his or her employees. OSHA may use the general duty clause if there is a recognized serious hazard and the employer does not take reasonable steps to prevent or abate the hazard. The general duty clause is used only if there is no standard, which applies to that identified particular hazard. OSHA regulations which apply to labs fall in the general industry section, which is in part 20, uh, 1910. There are hundreds of sections within 1910. The next two slides, I will quickly go over the most common sections applicable to labs. Since we are short on time, I've prepared a handout which goes over in more details, these primary sections. I'll quickly highlight some of these sections and for certain ones we will go over in more detail later in this talk. So the first one, occupational exposure to hazardous chemicals in laboratories is the main standard for labs. It is commonly referred to as a lab standard. We'll go over into more details later has come or has Communication is technically covered in the lab standard, but it still applies to support personnel who enter the laboratory such as custodial or facilities personnel, eye wash and UDE showers is in the first aid section. The wording and the regulations is very brief. So what OSHA does is they look at the ANSI Z 3 58 0.1 consensus standard for guidance, uh, for employers to use for their eyewash showers. There are several sections which cover personal protective equipment or p p e. One particular requirement in the P p E section is for the employer to perform a job hazard assessment or a J H A and specify the required p p E for the specific jobs. It also requires the employee to be instructed and uses P P E in accordance with manufacturers instructions. In certain labs, there are belts and pulleys. They require guardian. So lab workers will not get their fingers caught in the belt or pulley and lose a finger. Storage and handling of flammable liquids is always an issue in labs for emergencies. There are requirements for fire extinguishers, sprinklers, emergency action and fire prevention plans, along with a requirement for unobstructed exits and clear ioas and corridors for egress. Material handling and storage are always issues in laboratories for labs in earthquake areas. There are many, many issues, uh, we should be concerned about. Storage of chemicals also falls into this ca category of, uh, materials handling and storage. Housekeeping is always an issue in labs due to either a lack of space or lab workers electing not to make the effort to keep the workplace clean and orderly. Uh, we will go into more detail on the last three items on this slide later on. This talk has whopper emergency response, access to medical and exposure records, and reporting serious injuries and fatalities. Here are some of the major requirements in the OSHA lab standard. First of all, the requirement for a written chemical hygiene plan, which we sometimes abbreviate as the C H P, uh, designate a chemical hygiene officer to implement the chemical hygiene plan if needed to help implement the chemical hygiene plan. A chemical safety committee can be established emphasis on how particularly hazardous substances or P H Ss are, are, are handled. P h s are select carcinogens, reproductive toxins, and chemicals with highly acute toxicity. How information and training will be conducted to ensure lab workers are aware of the hazards and what procedures have been established to prevent lab workers from exposure to these chemicals. Okay. How the lab will determine the lab workers' exposures to various chemicals and methods to protect workers, such as use of fume hoods, uh, personal protective equipment, work practices, et cetera. Okay, and how to, how the lab will implement its medical monitoring program after exposures or if employees start showing signs and symptoms from exposures to various chemicals. Okay, Let's go over the main elements of the, uh, chemical hygiene plan, which are the practices and procedures for use of chemicals in the laboratory. Okay. The C H P should establish guidelines, practices, and procedures for use of chemicals in the lab, which includes SOPs, which are to be developed with specific procedures for working with a chemical or a class of chemicals or a particular process. The s o P should address what are the hazards and what are the risk. It should also address what steps are to be taken to control hazards using the hierarchy of controls, such as engineering controls where you enclose it, use substitution or ventilation use of administrative controls If engineering controls cannot control the hazards and then use of p p E as a last resort, the s o p should also address what are the possible unplanned events which could take place, and if that occurs, what are the plans to address that particular emergency? The c h p needs to address when the fume hood is to be used measures to ensure proper operation of the fume, hood and procedures to follow if the fume hood is not operating properly. It should also address criteria for the use of P P E, such as the lab coats, aprons, uh, gloves, face and eye protection and respiratory protection training. Uh, to ensure employees are made aware of the hazards of the chemical. Many universities have a generic online one hour, uh, lab safety training. Typically, this training is lab safety, health and safety training, uh, kind of from the 1000 foot level. The individual lab needs to supplement this generic training with specific training for that individual lab and specific lab individual processes and SOPs. So, so this individual training by the lab addresses health and safety training down to the 50 foot level. Okay. Circumstances which require approval from the supervisor or manager before an experiment or process is initiated, initiate it. For example, if the quantities of a chemical or upscale, uh, specific approval must be given before that particular experiment can proceed. In, uh, 2010 Texas Tech experience an explosion when a grad student upscaled the quantity of nickel hydrogen per chlorate 33 times over the maximum approved limit without approval, and that resulted in the employee losing three fingers in a perforated eye. Lastly, procedure on how medical examinations or consultations would take place when exposures have or may have occurred. Uh, for the next 15 to 20 slides, we'll see examples of common health and safety violations, which I have observed in in laboratories over the years. Uh, this first slide, one of the most common violations is either no label on the container with a name of the chemical and or no hazard warning on the container. When transferring from one container to another, the new container must be labeled with a chemical name and the hazard warning, unless it is under the control and only to be used by the lab worker who made the transfer, and that lab worker uses that container within that work shift. Here are some examples of incompatible chemicals being stored next to each other. On the top one, we see acid being stored next to bases. Uh, below we see organic acid, uh, like acetic acid being stored next to some mineral acid. Uh, for example, uh, nitric acid. Okay, food or beverages being stored. Consume in the lab is always an issue. I've encountered food being stored in a laboratory, refrigerator or freezer. So again, food or beverages should not be eaten or stored in the laboratory. There have been some labs which have designated clean areas, uh, where food and beverages can be eaten or consumed just due to, uh, lack of space, and that's typically in odor labs, uh, which they, they just did not have the space designed in into that laboratory. Certain chemicals such as EERs or tetra hydrorange can form unstable peroxides, which have the potential to explode to prevent peroxide from forming. The common practice is to keep track of how long the chemicals have been in the lab by labeling the container with a date, received the date open, and periodically testing for the but or peroxide. The container should also have an expiration date, which is a date by which container should be disposed of in chemical storage areas. If you not keep an eye on the condition of the containers, it may lead to deterioration of the containers or possible reactions with other chemical containers nearby. For example, in the photos here on the one, the right, the top end, you see a rustic container that's been sitting there for years and years. On the lower right photo, you see a container of nitric acid, which reacted with other cont uh, chemicals in the media storage area, which resulted on the beat up of precipitates. On the top of that, uh, bottom housekeeping is a problem which is found in many labs. Lab workers, they tend to leave, uh, clutter on the benchtops, such as used gloves being left out rather being disposed of. Used paper towels not being thrown away. Chemical bottles left out were not put away or chemical bottles left on the floor. Eyewash and dhow issues are commonly found, and that's, uh, due to a lack of clear space around these units. Uh, the shower head must have a 16 inch clear space radius around the shower, and the eyewash fountain must have a minimum six inch clearance space from the eyewash head to the wall. Uh, again, you need clear space in front of these units to allow, uh, lab workers access to these units, uh, in event of emergency. Other issues found with eyewash and dilute showers are not visually checking the eyewash dute shower either weekly or monthly, and not performing the annual performance tests on the eyewash shower units. Some eyewash shower units have been found that after a while, such as 10 minutes after use, the eye wash fountain tends to start to, uh, be a dribble and not able to wash both eyes simultaneously. That's why it's extremely important to do these performance tests at least once a year. Uh, b exit in ioas are very common in laboratories due to lack of adequate space. Uh, Unguarded belts or vacuum pumps, uh, can be a serious hazard. In laboratories, uh, uh, pumps without guards over the belt can lead to a lab worker, uh, losing a finger, and OSHA would consider that to be a serious violation, which can result in a $15,000 civil penalty. Okay, poor fume hood. Housekeeping is a very common problem in many laboratories. Large items in the fume hood can block the airflow into the fume hood, which would result in dead spaces where the face velocity would not be capable of capturing airborne contaminants. This may result in lab workers being exposed to airborne contaminants. Large items should either be removed or elevated on blocks to allow the airflow to go under the large item. Crowded fume hoods may also be contrary to the manufacturer's recommendations. Some fume hood manufacturers recommend that more than 50% of the fume hood surface should be left open. OSHA could cite an employer for not using the fume hood in accordance with the manufactured recommendations. If you have a crowded fume hood, When a fume hood is out of balance, the fume hood will sound, the alarm will sound. There have been several cases where the lab worker elects to continue to work in the fume hood, and he or she would find creative methods to engage the mute button. An OSHA inspector would consider this to be an instance where an employee purposely overrides a safety device and would probably cite the employee employer for a serious citation, uh, for overriding a safety device. If the alarm is ringing and the fume hood user cannot figure out the cause of the alarm, the fume hood should not be used and be posted with a big sign. Do not use the fume hood. Sash should be kept at or below the mark where the face velocity is at a hundred feet per minute. The only time the sash should be raised is, is when the items are either being placed or removed from the fume hood. Having open containers within the first six inches of the fume hood opening is also contrary to the manufacturer's recommendations. Fume hood users may be exposed to chemicals, uh, in the, with open containers within the first six inches. If the fume hood is defective, it must be removed from use and posted with a large sign. Do not use. In the lower picture. Here, we see that the fume hood was, had a sash, which was broken. Someone wanted to use the fume hood, so they found a container, placed it in there to hold up the sash while they were working in the fume hood. This, again, is contrary to, uh, safe war practices In the area of compressed gas management. Three common violations are not, uh, securing the cylinder to prevent the it from falling over. The standard does not state how many chains are to be used. The best practice is to use two chains, one at the one third height, and the other, the two third height of the cylinder. Another issue is not placing the valve protective cap onto the cylinders when they're not in use. In the lower picture here we have an example of a violation where they were storing flammable gas cylinders within 20 feet of an oxidizer, which is a oxygen cylinder here, which is considered also to be an OSHA violation. Misuse of, uh, p P E is very common in laboratories. The most common issues are either the failure to wear p p e in the lab or not worry in the proper type of p p e in the lab, examples of not worrying, uh, the proper face protection or eye protection or failure to wear the proper type of hand protection. Another issue in laboratories is bringing contaminated food into designated clean areas. Uh, this would bring contamination to areas where people would either consume food or consumed beverages. Very common in the lab setting is the reuse of single use gloves. On the box of many of these gloves is a note that they are for single use, one time single, one time use only. We frequently find lab workers removing the gloves and put them aside for reuse. This is not only following the manufacturer's instruction for the use of their gloves, but also leaving potentially contaminated gloves on the bench stop or the fume hood not storing respirators is commonly found in laboratories. The disposal dust masks, or N 95 respirators are the most frequently used respirators in laboratories. When not in use, they need to be stored in a manner to protect the respirator from dust, sunlight, or chemicals. What we commonly found, again, is the respirators are just left out in the open or in on shelves next to chemicals. Sharp objects such as razor blades, knives, or broken glassware are hazards to the laboratory workers. Razor blades and knives must be stored so that the sharp edges are not able to accidentally cut the lab workers' hands. Broken glassware needs to be disposed of, so they do not accidentally cut the lab workers. Commonly broken, broken glassware is found around or in the sink areas of the laboratory due to a lack of an adequate number of electrical outlets. Many laboratories, the improper use of electrical extension cord is an ongoing issue. Okay. The electrical regulations state that flexible al extension cords are not to be used in lieu of fixed wiring. Extension cords also are not to be attached to walls run through doorways. Walls are attached to building surfaces. Extension cords can also create a tripping hazard. In the laboratories. Daisy chaining is plugging one power strip or surge protector into another. The OSHA regulations require the use of equipment to be accordance with any manufacturer's instructions, which included, which includes the listing or labeling. Daisy chaining does violate the UL listing for surge protectors and power strips. Electrical outlets, which are located within three feet from a sink, much must have A G F C I outlet. There may be exceptions in which they grandfather older electrical outlets. There are portable G F C I plugs, which can be purchased for around 20 to $25, which you can see in the picture here. Okay. Many times for lab benches, the whole circuit of plugs may be tied together into one G F C I plug that would meet the requirements for A G F C I outlet. You may not visually see it on the plug near the sink, so you should check with your facilities person how the electrical setup is for your laboratory. Due to lack of space in, in laboratories, lab workers sometimes end up storing items in front of the electrical circuit breaker. The electrical safety order requires a clear space in front of the al Circuit breaker, which is six foot six, six inches high by 36 inches deep and 30 inches wide. This would allow the electrician access to the electrical circuit breaker in the event of an emergency. In some labs, they end up making the area in front of the, uh, uh, circuit breaker with a marking, which you can see in the photo here, which warns the people. The area is to be kept clear. Storing more than 25 gallons of flammable and combustible liquids outside of flammable storage cavity is always an issue in laboratories. In California, however, uh, they have allowable quantities down to only 10 gallons for educational occupancies. Failure to bond and ground while dispensing flammable liquids from one container to another is a big issue. At one of the University of California campuses, there was an incident several years ago where Penting was being poured out of a five gallon container into a bottle without bonding and grounding. What happened was static electricity built up and the pen liquid pentane caught fire. The person dispensing the liquid dropped the five gallon containers, and it resulted in the fire spreading, and the fire ended up destroying two fume hoods and resulted in over $300,000. In damages to the laboratory, fire sprinklers are required to have an 18 inch cleared space below and horizontally to allow the sprinkler to have an unobstructed spray pattern. When the sprinkler is triggered to operate. This fire regulation is usually violated because many laboratories lack adequate STA space to store materials, and therefore they end up stacking items up to the ceiling. As you can see in the photo here, portable fire extinguishers are typically located near the doorway into the lab. A fire extinguisher is be located within 75 feet of where it is to be used or needed. Common fire extinguisher violations found or not mounting them to the wall, not identifying them with a sign, not checking them monthly, or having the access to the fire extinguisher. Block persons whose job requires them to use the fire extinguisher are to receive annual training on how to use the extinguisher. First aid supplies are to be adequately stocked in the absence of an infirmary, a clinic or hospital in near proximity. One common violation found is first aid supplies are often found, found to be expired. For laboratories which use hydropholic acid, the first aid treatment is applying calcium gluconate to the areas which have been exposed. Containers of calcium gluconate are often found to be expired. Issues have also occurred when the emergency room is not familiar with exposures to hydrofluoric acid. It would be helpful for an exposed worker to bring along the hydrochloric acid emergency room treatment guidance document, which was developed by Honeywell. Uh, one of the handouts for this session will be a copy of the Honeywell Hydropholic Acid First Aid and Medical Treatment Guidance document. There is an OSHA standard hazardous waste Operations and emergency response, commonly known as has whopper for laboratories. The the ER portion of emergency response is a section which is applicable to laboratories Regarding laboratories. The common guidance given is if it is an incidental spill, it would be safe for the lab worker to clean up. The OSHA definition of an incidental spill is it does not pose a significant safety or health risks to the employees in the immediate vicinity. It does not pose a significant safety and health risks to the employees cleaning it up, and it does not have the potential to become an emergency. For an, for example, if it's a small spiel in the fume hood, typically it's okay for the lab worker to clean it up. However, sometimes it's difficult to give a specific guidance, uh, for quantities or volume of a spill because again, hazards of, uh, different chemicals can vary due to the specific hazard of different chemicals. For an incidental spill, the respondent would be required to wear respiratory protection, uh, gloves and protective clothing. The responder would be a member of a hazmat team. Uh, if the employer does not have a hazmat team, uh, typically the local city or county, hazmat would be the one to respond and clean up the spill. As a lab manager, if there is a non incidental spill, you would not clean up the spill or enter the immediate area of the spill. Instead, you would, from afar from the spill, keep the people out, protect nearby persons and protect property and the environment from a distance. If we look at the hazmat, uh, regulations under emergency response, the lab manager would fall under the first responder operations level, or commonly called fro F R O. When you initially respond to the release in a defensive fashion and try not to stop the release, but contain the release from a far and keep people out for a fro, there is a requirement to receive eight hours of initial emergency response training and annual refresher training thereafter. So this is an important training all lab managers should have initially and annually. The next requirement that a lot of folks are not aware of is a requirement report. Serious injuries or fatalities, OSHA or the state OSHA program requires all fatalities, inpatient hospitalizations, amputations, or loss of an eye to report it to the local OSHA office within eight hours for fatalities or within 24 hours for an inpatient hospitalization, amputation or loss of an eye reporting can be done via phone or in person to the local area, OSHA office, or by phone, the one 800 OSHA to free phone number. Or it can be done electronically by going online to the osha.gov webpage and using the reporting form there. As part of the OSHA employee right to know regulations, employers are required to maintain documentation of an employee exposure records such as safety data sheets, employee medical records, and employee exposure and monitoring records. The employer is also required to maintain these records for their duration of employment, plus an additional 30 years. The employer is required to respond to an employee, employee or an employee representative request for such records within 15 days. One requirement that many employers are not aware of is initially, and at least annually thereafter, the employer is required to notify all employees of the existence of the medical and exposure records. Who is the person within the company who's responsible for maintaining these records and the availability, availability of 29 C f r 19? 10 point 10 20. Okay, so let's talk about an ocean inspection. Next, what triggers an inspection? Most likely it would be a complaint. A complaint by an employee or an employee representative is considered to be a formal complaint, and OSHA is supposed to respond to formal complaints within 15 working days. An informal complaint would be one filed by a member of the general public or a concerned citizen. This type of complaint carries a lower priority, and sometimes OSHA may not respond to an informal complaint. Okay. Other situations which could trigger a an inspection would be, uh, one, a follow-up inspection after a serious citation had been issued, or two, uh, OSHA has a target industry program in which they target a certain industry to inspect, or three, it's part of a sediment agreement, uh, with osha, uh, following the 2009 U C A L A laboratory fatality as part of the settlement agreement to ensure all conditions of the agreement were complied with. Cal osha, uh, had in the agreement that they would inspect up to three uc campuses each year over the course of four years. So we as the University of California, were aware of those inspections coming up. Okay, so what happens during an OSHA inspection? Okay, when the OSHA inspector first arrives on site, he or she would request to see the highest level of management available at that time. So the highest level of management happens to be out to lunch or at a meeting. Uh, they would ask, okay, who's next in charge? And that's who they would, uh, request to see. Uh, they would present their ID and would hold an opening conference with the highest level of management. After the opening conference, the OSHA inspector would initiate a walk around inspection and would ask an employee representative, such as, such as a shop steward, be offered the opportunity to accompany the inspector on the walk around. If there is no employee represent representative, or it is a non-union shop, uh, the inspector would be required to talk with a representative number of employees, and, uh, it would be in private, away from management. The inspector may ask, uh, the employee if they have any health and safety concerns. During the inspection, the inspector would look at health and safety records, such as training records, inspection records, monitoring results, and injury illness logs. Okay? The inspector may request copies of various records to take with them and would also take photographs to document their findings. After the inspection is completed, the inspector would hold a closing conference where they would summarize their findings and would either issue citations at the closing conference or would issue 'em, uh, via, uh, registered mail to the employer if any violations are found. Okay? So when an OSHA inspector arrives to inspect your lab, it's really important, uh, to leave a good initial impression on the inspector. Again, the inspector's job is to identify violations. So if you have a, a good lab in their mind, they'll think, I'm wasting my time here. They have a good safety program. I wanna go find a lab where there's issues. So you, you wanna leave this, uh, positive impression. Okay? And a positive impression is that you have an effective health and safety program. Okay? If, however, the inspector sees issues that inspector would wanna dig in and find out, well, why are these problems occurring in this lab? What's wrong with their health and safety program? So, some initial, uh, problems which would cause the inspector to be concerned are things like poor housekeeping or the labs a mess. Uh, egress access to exits are blocked. Uh, emergency equipment, eyewash showers, fire extinguishers are blocked. Or they go in and they see lab workers not wearing proper, uh, p p e, no lab coats, no eye protection, no face shield, no gloves. Again, this leaves a negative impression on the inspector, and he may hang around. He or she may hang around your lab for longer time and talk with more employees to get to the bottom of this. Okay? So if you can show the inspector you have a effective and ongoing safety program, it will, uh, lead the ocean inspector with a positive impression of your laboratory. Okay? So the last two slides will discuss positive steps to not only improve the safety culture of your lab, but also make a positive impression on the OSHA inspector. Okay. Uh, one thing. Okay. The first thing is the lab conducts documented periodic inspections to identify unsafe conditions and work practices. The lab needs to correct these, any deficiencies found in a timely manner, okay? If a deficiency happens to require a longer time to correct, such as, for example, if something has to be ordered, it might take months to come in or lack of funds. What the lab needs to do is implement an interim corrective measure, uh, to prevent the lab workers from being exposed to that unsafe condition. So you might adopt the interim, uh, safety practice or, or some kind of interim, uh, measure. Uh, so they're not exposed this the unsafe condition. Okay? Okay. Another, uh, way to improve your safety culture and keep your OSHA inspector happy would be to have a established and effective health and safety training and communication program. Uh, a good way to do this would be health and safety is discussed at every lab group meeting. Now, the National Academy of Sciences recommend that this be done using the safety moment concept to begin each meeting, or health and safety concerns are openly discussed. Safety moments can be considered, uh, to be health and safety training. And as such, should be documented with sign-in sheets, an agenda and minutes to document, uh, discussions. Again, when the safety training done, it really needs to be documented. Uh, OSHA's view is if it hasn't been documented, it wasn't done. So you have to have some kind of, uh, sign in sheets and agenda for the inspector to, to view, Okay? Okay. Whenever there's a fatality accident incident or a near miss, the lab in partnership with your E H N S office should develop a lessons learned to assess what happened, find out what was the cause, and not only what went wrong, but also what went right. They should develop, uh, corrective actions to prevent such an event from occurring in the future. And lastly, summarize the lessons learned document with up to four to six lessons learned. Bullet points. Okay. Lessons learned should be discussed at the next lab meeting as a training topic and shared with other laboratories and other institutions to prevent a similar incident from occurring in the future. Now, the U C L A Center for Lab Safety has a lessons learned webpage where if you forward it to them, they'll sanitize the lessons learned so people won't know which particular, uh, company or lab this was, and they'll post it on their lessons learned webpage for other, uh, laboratories to look at and use for their training and safety moments. Okay? Okay. Lastly, uh, uh, continue Non-compliance is an ongoing issue at many, uh, laboratories. So to ensure that there's a health and safety program, the lab needs to develop a program to address, uh, continued non-compliance of health and safety practices and procedures. It should not only include retraining, but also trigger a progressive disciplinary program if the employee continues to not comply with established health and safety practices. This would include documented verbal and written counseling of the employee. The lab should consult with your human resources department prior to implementing such a progressive disciplinary program. So that, uh, that's it for the presentation. Uh, I would like to thank you for attending, and are there any questions? Thank you so much, Larry. At this time, we are ready to move into our question and answer portion of the webinar. A reminder for those who may have joined us late, that you can send us your questions or comments by typing them into the q and a box located on the right hand side of your screen. This is another reminder to please visit the handout section on the right hand side of your screen as well for more supporting information about this event. And let's get started with our first question from the audience. So, Larry, your first question from the audience is, after a lab worker has been accidentally exposed to a chemical, there is always a reluctance to use the emergency shower. Any suggestions to get them to use the shower? Shower? Okay, thank you for the question. What we have found is, uh, for the emergency shower, there are three main reasons why the, uh, lab workers don't like to use the shower. The first reason is they're afraid they're gonna flood the lab. 'cause a lot of, uh, showers, they, they don't have a drain, so they're afraid they're going to be, be flooding the laboratory. The second reason is that, uh, hypothermia, what they find is if they're in the shower for long periods of time, they're really cold, and they, they just would hop in. They wanna hop out and which, which doesn't, uh, meet the intent you to be used in the shower for 15 minutes. And the last reason is modesty. They do not want to remove their, the clothing, uh, to go into the lab. So how this can be addressed is okay, uh, for the flooding of the, uh, lab issue, it's gonna be flooded. That's, that's, that's a give me some labs. What they do have is they have those little pigs where they can put it around the shower to, uh, to keep, uh, the water there. And hopefully it, it would, uh, uh, they wouldn't, people won't be as concerned about that. The, okay, the, uh, the, the hypothermia and the modesty issue, they kind of go hand in hand. So what some labs have done is either around the shower, they've, they have purchased modesty curtains, but I see very few of these. But some laboratories, what they have done is they've set up a, as part of the emergency procedure is, uh, uh, just, uh, holding, uh, uh, people around circle around the person in the shower, holding up lab coats as kind of a, a curtain around the, the persons such as, if it's a female employee who gets splashed, they'd have the female employees, uh, stand around there and hold up the, uh, lab coats. If it's a male employee, that's the other way to do it. And the other other way to address this would be just training. You gotta train and, and emphasize employee. It's important to get into the shower as soon as possible. I have an instance with a friend who said, uh, one of their lab workers as a result of their training, they immediately, without even thinking about it, they ran to the shower and they, they turned it on right away without even thinking about it. So if it's part of your ongoing training, emphasize people to go to the shower, you get something on you or, or, or, uh, a flammable on you, it would trigger in immediately, unfortunately, the U C L A incident where, uh, Sherry Sanji was, uh, caught fire. She had an emergency shower within five feet of her, but she did not go to it. And since she ran elsewhere, if she would've went to the shower and turned it on immediately, uh, it would've, she probably would've been saved. She would not have died. Um, so the second question that we is, um, if there are some unique hazards in the laboratory, which requires particular training, can I deny the OSHA inspector access to the laboratory? Okay. Thank you for the question. If it requires particular training, uh, you can deny it or, or if it's a real bad hazard. So I would, uh, uh, spell out to the OSHA inspector that because of this situation, you really cannot, uh, enter that particular laboratory will be willing to, uh, uh, answer questions or provide you documents there, but you really, uh, cannot enter that lab due to a particular hazard or experiment. Okay. Awesome. Thank you so much. Uh, we have time for one more question from the audience, and that question is, if I'm issued a citation by osha, what are my recourse if I do not agree with the citation? Okay, thank you for the question. Okay. Once you're issued an OSHA citation, you have, uh, fif 15 days to file what's called an appeal. And the ap, uh, if you filed an appeal, it would go before an administrative law judge, and there would be a, a administrative hearing where, uh, the OSHA would be on one side and the employer would be on their other side. Typically, employers, they would get a, an attorney to represent them and go before an, an appeals judge where you could, uh, contest, uh, the existence of the violation, uh, the abatement date or the reasonableness of what it takes to debate the violation. So, so that's, that's the, the, the legal route you can go to. There's also an allowance for, uh, the employer to request an informal conference. And typically, uh, uh, once you receive a citation, you can request, uh, an informal conference with the local OSHA office, uh, to meet with them and discuss, uh, the, uh, citation. And at that time, sometimes you might be able to bring more documentation to show them as to why you don't think it was a violation, or, yeah, you, you didn't have that documents at the time to present to the OSHA inspector. So those are some recourses you, you can do if you receive a citation and you don't agree with it. Thank you. Awesome. Thank you so much, Larry. Uh, do you have any final words or thoughts for the audience before we close out? Okay. Well, uh, okay. Again, this is just a quick overview in terms of, uh, OSHA and, uh, coming in, visiting, uh, your laboratory. So again, it's, it's important to be familiar with some of the, these, uh, regulations, but, uh, you should look at your E H N Ss office as, uh, uh, as your resource there. They're familiar with the regulations, uh, quite a bit, and they can give you guidance. So I would highly recommend you work closely with your health and safety office. You have any health and safety questions. Okay. Thank you. Awesome. Thank you so much, Larry. And with that, this brings us to the end of today's webinar. On behalf of Lab Manager, I would like to thank Larry won for all of the hard work that he put into this presentation, and I'd like to thank all of you for taking the time outta your busy schedules to join us today. A reminder that all of the presentations from the Safety Digital Summit will be available for free on-demand viewing following the conclusion of this event. So please watch your emails for message from Lab Manager once these videos become available. Once again, thinking to our sponsors, Athas Corporation Lab, Conco Corporation, or Lab Inc. And their support allows Lab Manager to keep these events free of charge for our readers. Please be sure to stay tuned for our presentation tomorrow at 11:00 AM Eastern titled A Layered Approach to Safety Protection, wherever your science needs to be. For more information on all of our upcoming or on-demand webinars, or to learn more about the latest tools and technology for your laboratory, please visit our website@labmanager.com. Thank you all for being a part of our Safety Digital Summit. We hope you have great day.