Looking Beyond Routine Lab Equipment Maintenance
The right partner will work with you to develop an equipment maintenance strategy
Equipment downtime—whether planned or unplanned—is costly to any laboratory. Downtime can result in lost operational time, lost resources, lost or delayed samples, and increased frustration for lab personnel. A study by Frost & Sullivan showed that lab managers ranked instrument maintenance and downtime as their top challenge. They also ranked planned and unplanned downtime as two of the top five factors limiting productivity.1
Scheduled maintenance and performance monitoring are important steps in ensuring that lab equipment operates optimally and that samples are processed and analyzed consistently, efficiently, and within regulatory definitions. Still, such efforts can disrupt lab productivity and cause other instruments in that same process to remain unnecessarily idle.
Unplanned downtimes, meanwhile, are just that: unplanned. They significantly reduce lab productivity and can jeopardize samples and slow analysis, disrupting downstream processes and timelines. Backup instruments can help to mitigate this risk, but their impact in an unplanned downtime can be limited.
A recent study at a Dutch clinical chemistry lab showed that the loss of a single instrument in an analytical process, even when backup instruments are available, can significantly delay obtaining results for high- and regular-priority samples.2 Given these challenges, the researchers suggested a review of preventative maintenance policies to improve lab instrument reliability.
The role of equipment service providers
Building a relationship with a trusted service partner is the first step in such a maintenance review. Such a partner can offer ongoing assistance with instrument maintenance and repairs and guide preventative measures and pre-emptive troubleshooting. This advice can significantly reduce the frequency and severity of instrument repairs, and therefore the costs of those repairs, resulting in significantly reduced lab downtime.
A service partner will work to understand the processes and applications of the lab equipment, potentially predicting unusual stresses or strains on the instruments. The traditional approach to maintenance schedules has been calendar-based maintenance (CBM), using rules-of-thumb from the instrument manufacturer or institutional experience to determine how often consumables should be replaced and systems maintained. CBM can work well for controlled lab settings when the number, type, and workflows of samples are predictable. CBM becomes less effective, however, in scenarios where there may be variable sample loads, a variety of complex samples, multiple operators, or harsh solvents.
For scenarios like this, usage-based maintenance (UBM) may make more sense. UBM involves monitoring and measuring the usage and performance of individual instruments, such that maintenance is aligned with the actual wear and tear an instrument experiences.
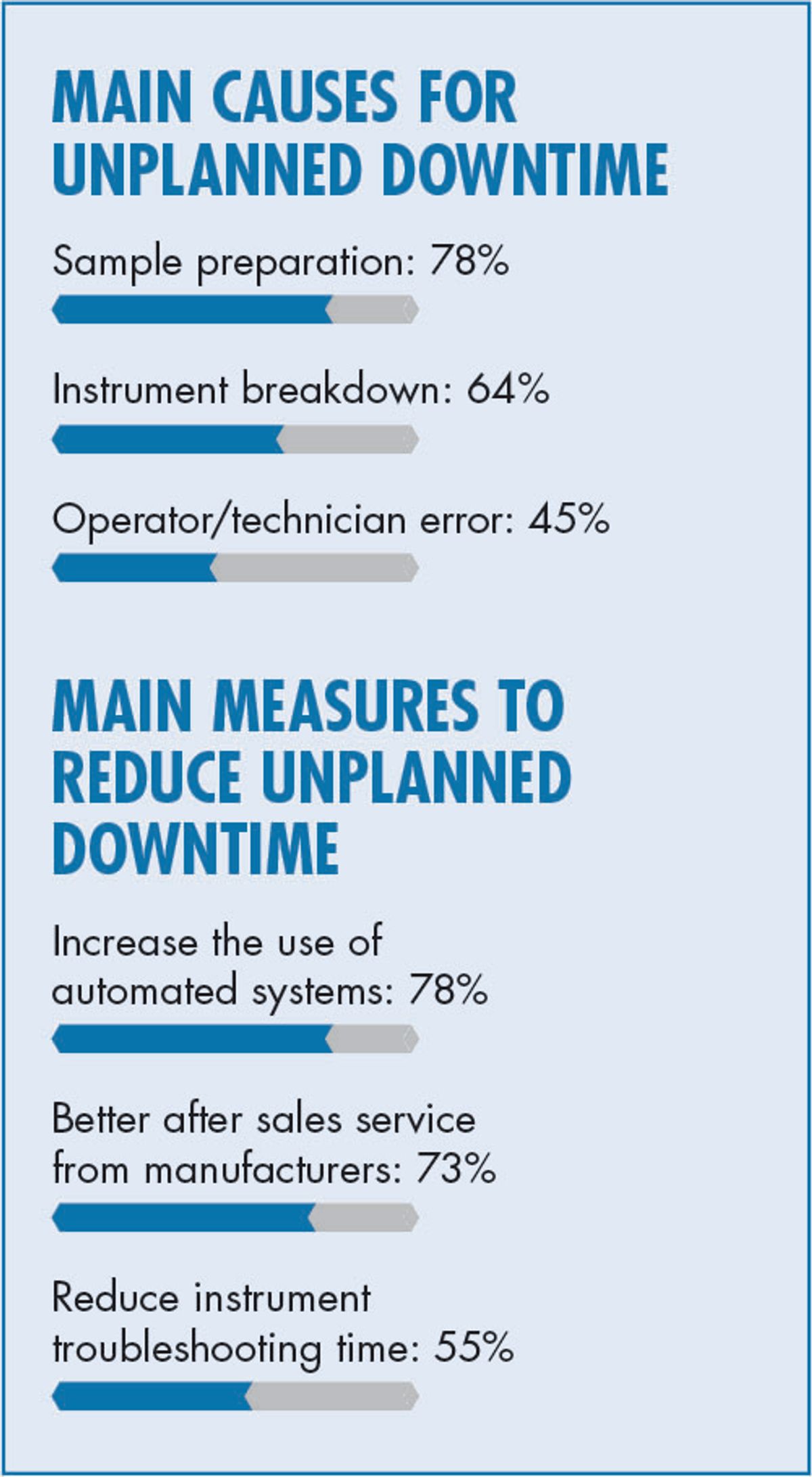
Usage questions may include: How many samples are run in a typical week? What types of solvents are routinely used? Is the equipment used for a single application or multiple ones? In what environment(s) is the equipment expected to perform? How do you define instrument performance and analytical precision?
UBM can accordingly help optimize the preventative maintenance schedule and scope. And because it is based on an instrument’s active use, application changes, sample type, or testing load usually translate to adjustments in the maintenance schedule.
To elucidate the relationships between instrument use in the lab and system degradation, a service partner can help to identify the appropriate metrics for workflow diagnostic tests. These tests’ results can then establish maintenance and consumable replacement schedules.
Once these metrics have been defined, software available from many manufacturers can help monitor these measurements in real time, providing regular updates and warnings when an instrument approaches the maintenance thresholds that have been established. The software also keeps a complete record of previous maintenance events and practices, information that can be accessed from anywhere, making it possible for organizations to monitor in-house performance and develop best practices without adding undue burden to lab personnel.
Tapping into broad expertise
Because many service partners work with a variety of labs and have access to a broad network of service personnel, they can offer access to invaluable insights that may be inaccessible to personnel within the lab. Such insights mean that during scheduled maintenance, the service partner may be more likely to identify problems that might otherwise have precipitated later unplanned downtimes.
Also, because only some labs or lab processes rely on instruments from a single manufacturer, finding a service partner who can provide expertise and support across instruments from multiple manufacturers may be advantageous. Such capacity can help ensure the integrity and efficiency of lab operations and minimize downtimes due to failures at numerous points by reducing the need for service or preventative maintenance from multiple sources.
Integrating a services partner into lab operations will increase confidence that the instruments are performing optimally and reduce concerns about the potential for and impacts of scheduled or unplanned downtime—whether on lab productivity, analytical output, or the organization’s reputation.
References:
- “Key challenges and pain points in the global laboratory market”. June 2017. www.agilent.com/content/dam/about/newsroom/infograhics/pdf/fact-sheet-lab-manager.pdf
- Tsai, E. R., Tintu, A. N., Bocherie, R. J., de Rijke, Y. B., Schotman, H. H. M., and Demirtas, D. “Characterization of laboratory flow and performance for process improvements via application of process mining”. Appl Clin Inform. 2023;14:144-152.