Look Before Leaping
What you need to know before converting commercial properties to labs
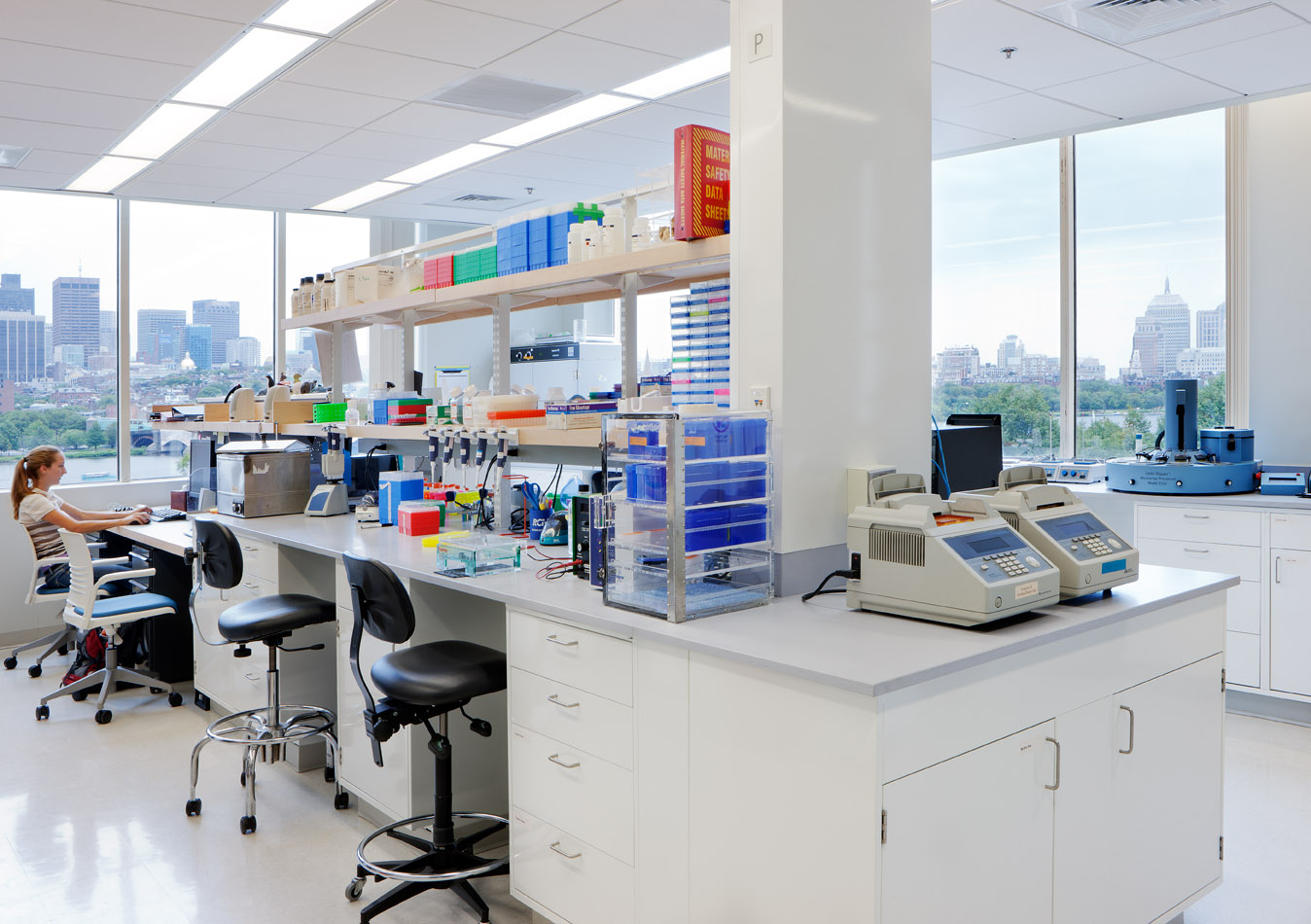
As office, retail, and hospitality tenants assess what they need for future space and building owners and developers examine supply and demand projections, one thing is clear—the supply of available commercial properties is quickly rising. Forecasts show this market shift will continue for the foreseeable future. If your company plans to expand or relocate current laboratory environments, the COVID-19-related market changes and work-from-home shifts provide an opportunity. Well-located commercial properties, including buildings planned for office use that are now in construction, are worth considering.
These opportunities also present important questions regarding the feasibility, cost, and complexity of converting them. Our advice: look carefully before you leap. Why? Most commercial buildings we review offer upside potential along with hidden peril. Here are five questions every research organization needs to be asking—and resolving—prior to committing to a conversion strategy.
Adaptability of the building’s structural system
A close look at a building’s base structure—its foundation, beams, columns, floor slabs, floor-to-floor heights, and structural bay spacing—will reveal important opportunities and constraints. For example, the ideal floor-to-floor height for a lab fit-up is typically 15 feet or higher. Mechanical duct work and above-the-ceiling equipment can be accommodated with lesser heights depending on the type of lab, though this will increase construction cost. With buildings in the 12- to 13-foot range typically seen in an office building, it becomes more challenging and costly to create sufficient above ceiling space while providing an appropriately spacious lab environment.
Weight considerations are also key. The average live load capacity in an office building is 50 to 100 pounds per square foot (PSF). Capacities in the 100 to 150 PSF range may be required to accommodate imaging and fabrication equipment in a research lab. Heavy lab equipment for imaging and fabrication require much greater capacity, typically in the 100 to 150 PSF range. It is also essential to review existing bay size; our best options exist when bay widths are in multiples of 11 feet.
Cost to upgrade HVAC and electrical infrastructure
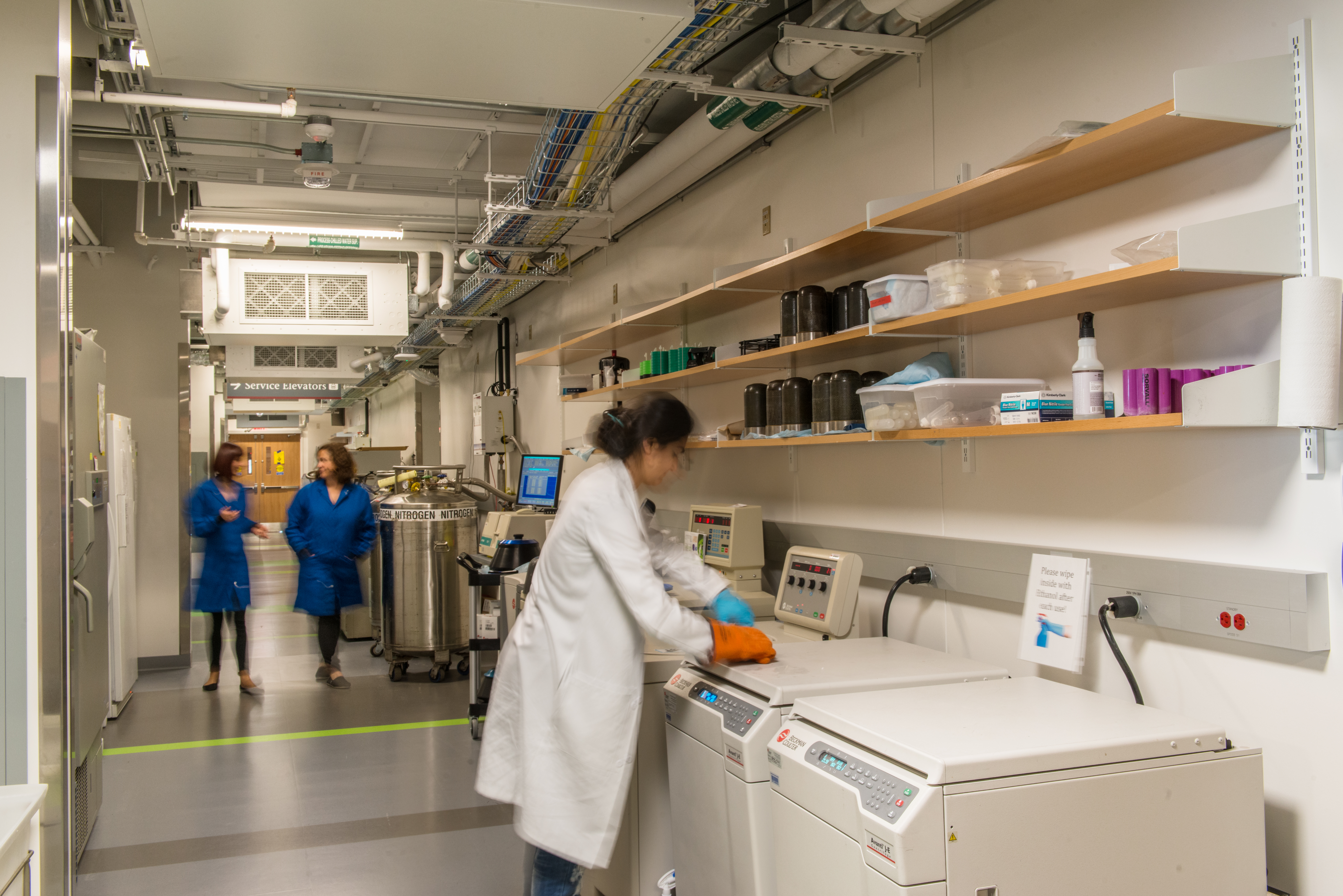
In commercial buildings, HVAC systems recirculate much of the air for heating and cooling, while in most lab environments systems are designed to move air only “once through” before it is released and resupplied. Achieving a higher level of HVAC performance, essential for contamination control in a lab, often requires larger and more complex system improvements to be designed and installed. Electrical power demand in lab environments often exceed the existing capability of existing commercial systems as well. Energy-intensive lab equipment, a reliable emergency power supply to protect ongoing experiments, and high-demand components including refrigeration units will outpace the electrical supply in most commercial buildings. Estimating the expected level of power needed, and anticipating future flexibility for adding capacity, are beneficial early action items.
Vibration risk
An objective understanding of vibration mitigation—existing and future—is a another crucial, yet often overlooked, consideration. Many conventional commercial properties are ultra-light in structure, causing even the vibration of occupant movement in a lab to be a potential problem. With hyper-sensitive tolerance standards, vibration-sensitive robotics, and use of equipment ranging from electron microscopes to nanotechnology testing, existing vibration levels and the feasibility of mitigating them for the intended research program can make or break a conversion plan.
Code issues and life safety compliance challenges
Code compliance for life safety, fire protection, and accessibility loom large when evaluating an older building. For example, understanding the limitations related to storing potentially hazardous materials is one of the big unknowns to resolve. What chemicals and flammable materials may be required? Where within the lab will safe, code-compliant storage for these materials be created?
Control areas—interior zones defined for the storage of potentially hazardous materials—should be planned in accordance with local codes and designed to provide maximum flexibility and practicality. Building codes often require that these control areas be concentrated on lower floors of a building. The largest allowances are made for the first floor and decrease in number of zones and quantity of materials as you move higher up. Understanding the compliance issues and managing materials handling will contribute to a cost-effective and predictable conversion.
Readiness for COVID-19 health and safety adaptation
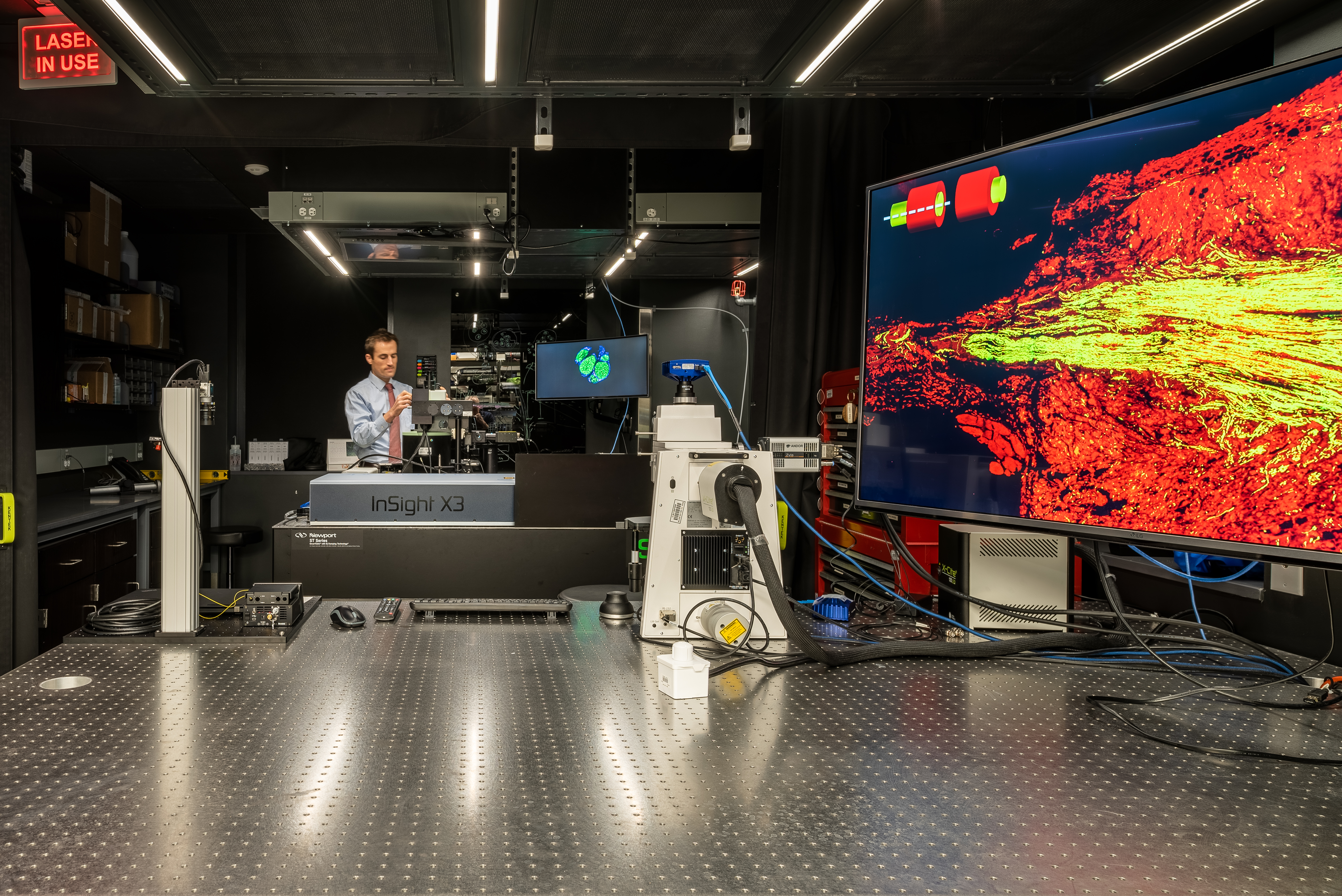
One of the challenges for every employer is gaining the confidence of employees returning to the workplace. Infection control through managing airborne contaminants is the ideal place to start. One of the advantages in updating existing laboratory workplaces is the presence of a high-performing, “once-through” HVAC system—at least in the lab side if not the office side. As noted earlier, commercial buildings typically rely on a recirculated air system for the entire building. When planning to build out a commercial space, consider the opportunity and cost parameters of a once-through HVAC design for both the lab spaces and the office and meeting areas. Improving ventilation through any opportunity, including operable windows where feasible, is a plus. Other opportunities to help reduce the risk of airborne virus transmission include installing ultra-violet (UVC) light fixtures to provide air and surface disinfection.
Summary
The reality is that most commercial spaces are simply not built for easy adaptation to laboratory use. Yet each conversion candidate property presents inherent positives and negatives. To develop a clear look and cost framework, a beneficial starting point is to establish a Basis of Design that integrates fundamental feasibility, cost, and schedule considerations. Among other benefits, a well-conceived Basis of Design allows the team to develop projections for a “level” of electrical demand, M/E/P service, and structural modifications needed to support the equipment and protocols of the researchers. To source the data needed, we benchmark equipment needs from other research facilities and seek the cost and constructability expertise available from specialty research consultants, construction contractors, and subcontractors. With an informed projection of cost, risk, and ROI, owners and developers can make a go or no-go decision more quickly, and if necessary, move on to assess other properties for conversion. Most buildings will reveal their opportunities, cost issues, and design constraints when we ask the crucial questions.
Bryan Thorp, AIA, LEED AP, is an architect and associate principal with Boston-based ARC/Architectural Resources Cambridge. He advises clients on strategy, planning, budgeting, and design for life science and laboratory projects, and provides a hands-on approach to managing these complex designs from feasibility through construction. Bryan can be reached at BThorp@arcusa.com.