How to Commission New Lab Equipment
Steps to ensure a smooth equipment commissioning process
Today’s laboratories are becoming increasingly equipment dense, with new instruments needed to support business direction changes, increase scientist productivity, and replace antiquated pieces. To ensure functionality of the equipment, a commissioning process should be executed when new equipment is installed.
The level of commissioning often varies by lab type; a GMP quality control lab requires a more stringent commissioning/qualification/validation than that of a research and development lab. But the steps each lab manager must take to determine and execute the commissioning activity is similar:
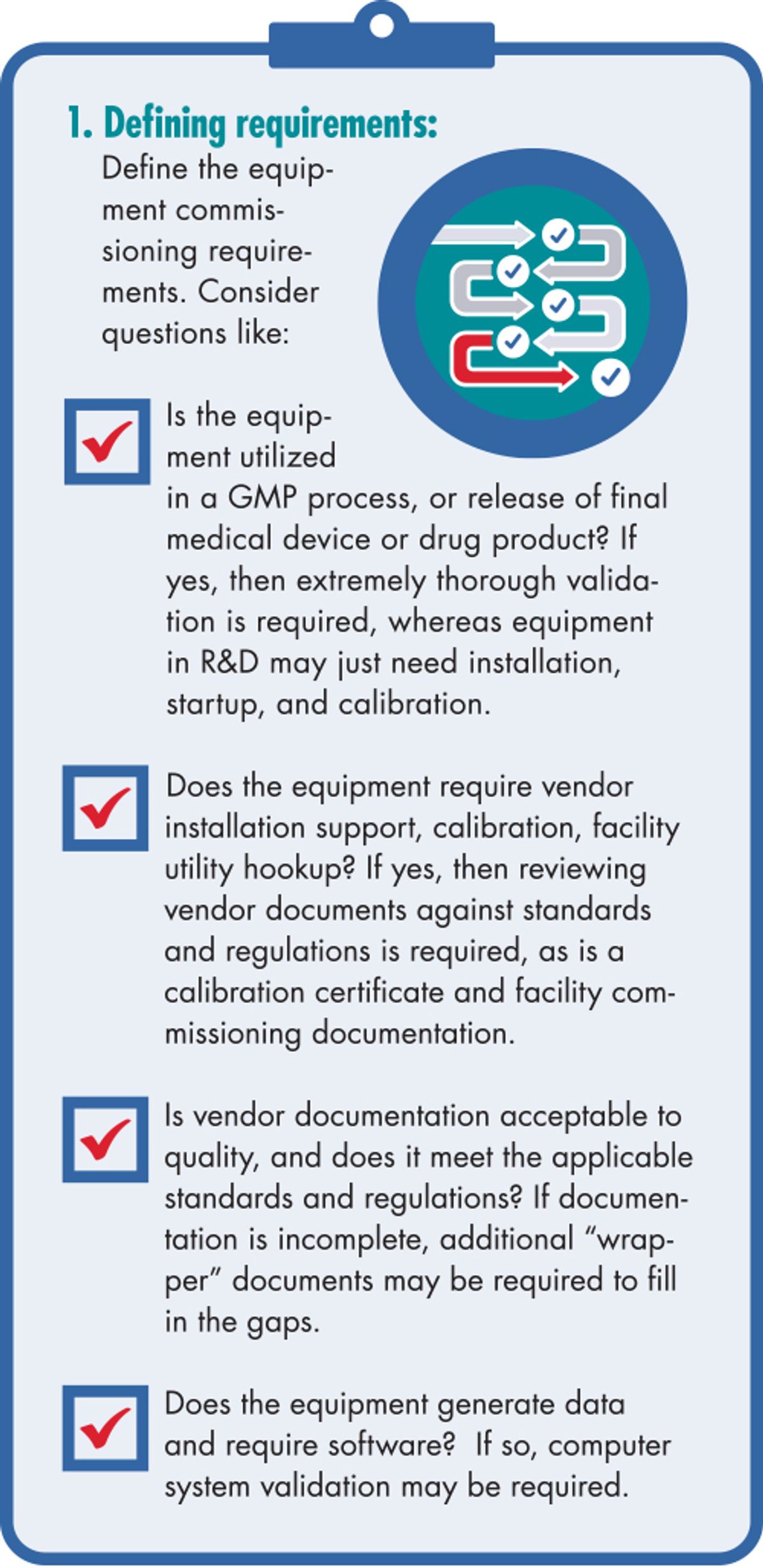
2. Planning:
Once the level of commissioning and associated requirements are evaluated and defined, the planning process can start. Typically, this is the most labor-intensive piece of the puzzle, as document development and approval are included. Planning often includes determining the “Ws” of the project: who, what, where, and when.
“Who” can be a combination of internal staff, the vendor, and external commissioning and validation suppliers. “What” refers to the executables—facility requirement verification, installation qualification, operational qualification, and performance qualification, software validation, and process validation. “Where” speaks to the environmental requirements and can also include pre-positioning activities that may be executed outside of the final equipment placement like factory acceptance testing. Scheduling the order of activities to meet the requirements falls under “when.”
3. Installation:
If we assume document development and approval is part of the planning step, next comes execution. Equipment installation is the first executable and is usually followed immediately by installation qualification (IOQ) and operational qualification. IOQ tests the requirements of installation from the vendor against the installed laboratory environment and requires a series of functional tests to confirm the equipment is operating as expected. If a performance qualification (PQ) is required, a specific method is tested on the equipment to ensure it gives an expected result. Software may require a similar test of both installation and operation, and combined with process and methods, usually relies on correct result generation.
4. Documentation:
After the execution of all protocols is complete and approved, a turnover package should be assembled. This package should contain all documentation related to the equipment, including purchase order, packing slip, operations manual, IOQ protocols and reports, and any additional PQ, software validation, method validation, and process validation documentation that supports the functionality of the equipment. Turnover packages may be retained by lab managers, operations managers, quality, facilities, or other responsible parties, and usually depends on the organization. A complete turnover package should tell the story of the equipment from inception through validation.
Once the turnover package is complete, the equipment is ready for routine use. The equipment may need preventive maintenance, calibration, requalification and validation, or other ongoing effort typically managed by a computerized maintenance management system or computerized calibration management system, which require additional documentation and effort.
The process of commissioning new laboratory equipment is vital for ensuring instrument functionality and compliance. Regardless of the lab type, careful consideration of commissioning needs, detailed planning, and methodical execution of protocols are essential steps. Finally, the compilation of a comprehensive turnover package, containing all pertinent documentation, serves as a crucial record of the equipment's journey from inception to validation. Successful equipment commissioning is a foundational aspect of modern laboratories, facilitating smooth operations and adherence to quality standards.