Four Strategies for Creating a More Flexible Lab Design
A few guiding philosophies help labs ensure they can accommodate shifts in tech, generate better results, and respond to evolving needs
Life science companies are facing either rapid expansion or consolidation due to fluctuations in market conditions, the need to adapt to new processes with rapidly advancing technology, and the increasing demands of speed-to-science—the accelerated demand to get medicines and therapies faster from bench to patient—in drug discovery. Similarly, universities and institutional laboratories require frequent renovation of existing labs as a recruiting tool to attract the brightest and best talent and adapt to the latest research instrumentation.
More than ever, lab facilities of all kinds are required to be nimble to meet the changing needs of laboratory users while responsibly using limited resources and minimizing downtime and rework. Running a flexible lab necessitates a flexible lab design—here are four strategies for designing a more flexible lab.
1. Apply flexible principles where it matters
Planning for flexibility starts at the project’s inception, as lab managers work with the design team to establish project goals and understand options that make the most sense. Lab managers can inform the team with valuable insight on day-one needs, growth projections to anticipate future needs, core processes, and future technologies that influence how much adaptability and change are required day to day and year to year. A balanced approach to flexibility yields better results in the best use of limited resources. Even small renovation projects can incrementally implement flexibility in design principles to improve the adaptability of the lab space and minimize future redesign.
For example, movable, adjustable casework works well in a collaborative open lab environment where users are enabled to modify their workspace to best fit their needs and improve ergonomics, but it is counterproductive in a lab where benches are assigned to instruments that require careful calibration and validation or are sensitive to vibration. Implementing flexible principles in lab design frequently requires a culture change associated with how the space is used. Innovative laboratories are changing space utilization models from a personnel-based bench to instrument- or process-based space assignments; this creates a culture that facilitates the sharing of resources and supports customization of the process where needed, allowing flexibility in the rest of the space.
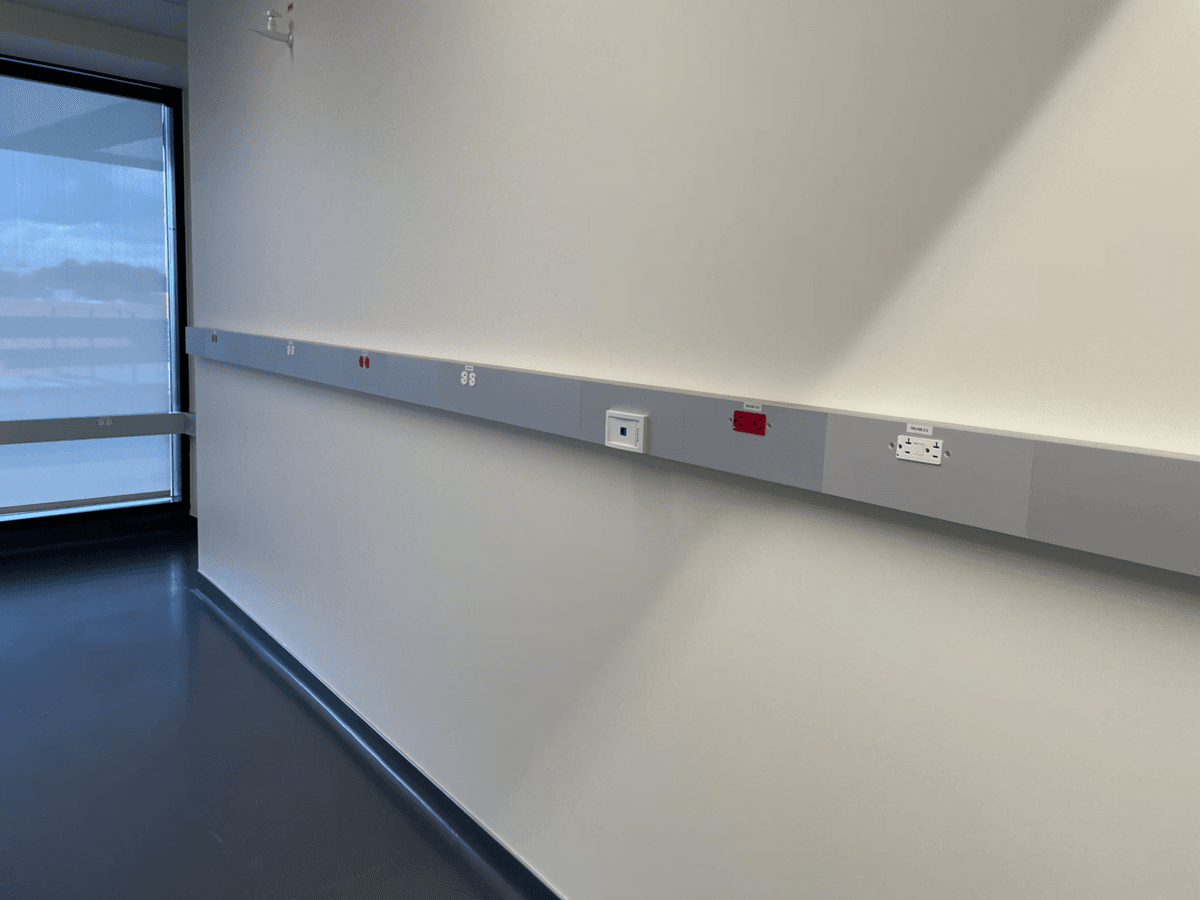
Another strategy to maximize flexibility and space utilization is the designation of wet-lab and dry-lab zones within each space. The wet-lab zones—defined as areas where sinks or other equipment that require fixed plumbing, as well as hoods that require exhaust connections or more specialized infrastructure—are generally arranged around the perimeter of a room with fixed partitions, while the center of the room is kept leaner and more generic. Similarly, specialized lab support rooms that require more intensive or customized infrastructure can be arranged closer to the core or spine of utility distribution and around the perimeter of open lab spaces. This arrangement minimizes utility runs and provides easy access to lab support areas anywhere in the open lab.
2. Modular design is your ally
Laboratory designers use certain proportions of a room’s length, width, and height, or “modules,” to organize space utilization. A typical design module ranges from 10.5 to 12 feet wide, 15 to 24 feet long, and 14 to 18 feet floor to floor, depending on the type and complexity of the laboratory. Using a module is a valuable tool to provide space allocations that can be interchangeable as program or department needs change over time, while room sizes and infrastructure allocations stay consistent across the building.
Flexibility in planning starts by designating broad categories of type and infrastructure intensity in the building program that can be accommodated with the building core and shell infrastructure. For example, a computational lab may require little to no plumbing and exhaust and high power density, while a chemical lab’s energy use will be driven by the number of fume hoods planned and the corresponding air volume that needs to be managed, as well as higher floor-to-floors for ductwork. Understanding the mix of laboratory types and the requirements of each format can assist the design team with planning for flexibility holistically in the core infrastructure.
The best design strategies extend the modular approach to flexible design across all disciplines. Structural engineers should address the design module when planning column spacing and floor-to-floor heights to maximize column-free space, selecting floor construction systems that can accommodate future slab penetrations or openings for new vertical chases or removing portions of the floor, and designating certain zones with higher loading capacity and vibration criteria to house specialized equipment, including roof areas.
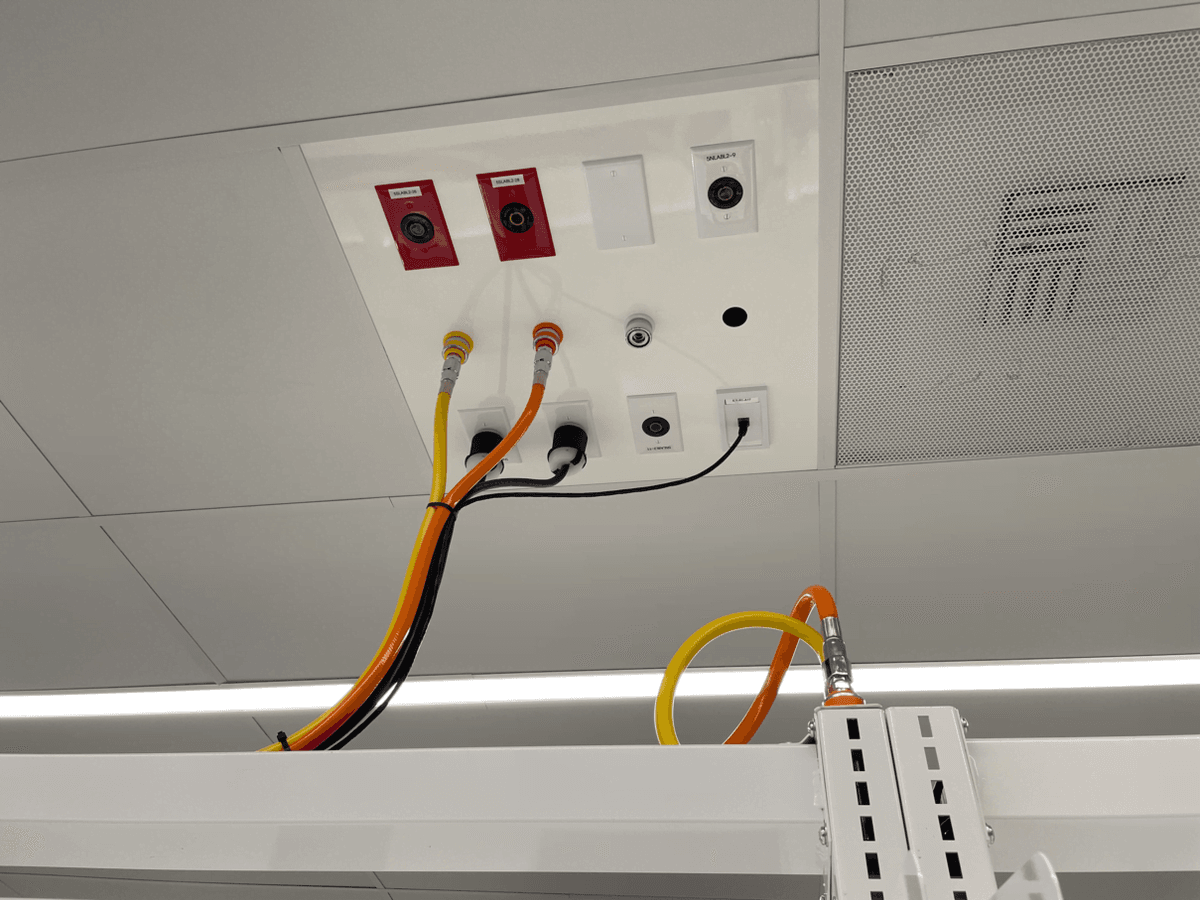
When planning mechanical, electrical, and plumbing infrastructure, HVAC and process utility equipment—as well as duct and piping distribution—can be designed with scalability and flexibility in mind. For example, running the main piping off a corridor spine allows certain modules to be valved off, enabling modifications without disrupting lab operations in other areas. It could also be helpful to reserve additional floor space and extra capacity in utility rooms to add electrical panels or equipment such as air compressors or deionized water skids. Finally, providing spare space in vertical chases allows labs to add exhaust or piping as needed.
3. Look to the future in addition to day-one needs
Many laboratories have adopted plug-and-play infrastructure systems with quick connects and plugs that allow lab users to remove a set of laboratory benches and modify the infrastructure within the utility chase without the need for demolition or downtime. This allows labs to easily integrate new technologies, such as automation or larger pieces of equipment, within the open lab environment. It is important for lab managers and users to recognize that current needs and the equipment matrix represent today’s requirements and will change over time. Spare capacity and pathways for future infrastructure are a must. For example, allowing for electrical and data outlets three feet on-center along a raceway—even if not all are designated for a specific instrument on day one—will allow for future flexibility if a new piece of equipment is purchased.
Good design strategies allow room for growth aligned with projections. For instance, reserving an allowance for “shell space,” an unfinished space within the floor plate that can be fitted out at a later date with provisions for connections to right-sized infrastructure, can be an effective way to future-proof space for a rapidly growing enterprise.
In addition to the physical space, the increasing prevalence of Internet-of-Things devices, artificial intelligence, and other data-intensive tools means that new labs are equipped with information technology backbones and data center infrastructure that can support more intensive data collection and management in the future.
4. A broad approach to flexibility can support diversity and inclusion and minimize your carbon footprint
Designing with flexibility in mind can support your company’s environmental, social, and governance goals. Flexible lab environments can reduce carbon impact and emissions by limiting the waste of demolition and renovation cycles over the life of the building—an investment that also can reduce capital expenses and downtime in the future. Additionally, providing a workspace with the flexibility to adapt to individual user needs in and out of the lab also helps support an inclusive and diverse workforce. Some examples include lab furnishings with the ability to be reconfigured to different heights, adjustable task lighting, and supportive seating for leaning positions. Outside of the lab, other examples might be providing places of respite where lab users can take a break from the harsh lighting and sterile environment of the lab, providing a variety of work settings with varying levels of privacy for collaboration as well as head-down work, and promoting well-being through biophilic strategies such as providing access to views of the outdoors.
The thoughtful application of flexible design principles in your next lab design or renovation can go a long way to positively impact workplace conditions, reduce carbon impact over the life of the building, and reduce costs associated with rework and downtime.