Does your lab manager's attitude about safety matter? Is talking about lab safety in the department important? Teaching laboratory staff the safety regulations is one thing, but ensuring compliance is another feat altogether! Attendees of this session will learn methods to improve your lab safety culture and ways to get staff to adhere to practices that protect them. Discover how large and small organizations can benefit from having a lab safety representative group as it works to flourish your lab safety culture.
Speakers:
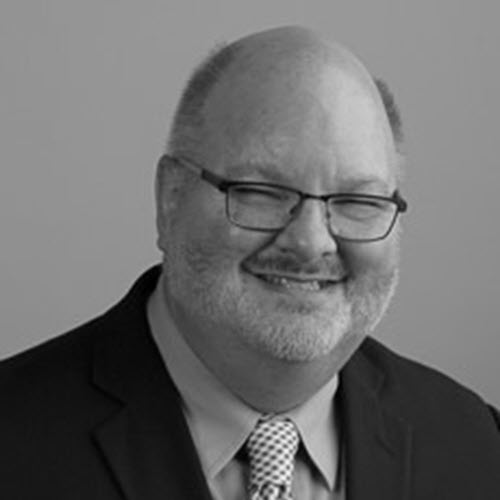
Dan Scungio MT(ASCP), SLS, CQA(ASQ)
Lab Safety Consultant
Dan The Lab Safety Man
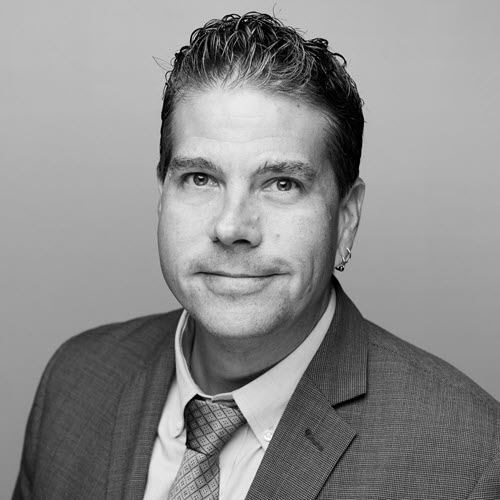
Jason Nagy PhD, MLS (ASCP)CM ,QLS
Lab Safety Coordinator
Sentara Healthcare
This Summit Talk was part of Lab Manager's 2023 Safety Digital Summit.
Lab managers are tasked with keeping their lab staff safe, which means anticipating and mitigating various hazards around the workplace. Heavy equipment, dangerous chemicals, sharp instruments, and mental stress all present varying levels of risk. Managers must develop a comprehensive lab safety program to protect their personnel, equipment, and products—this will help prevent tragedy, as well as benefit a lab’s bottom line by decreasing product loss and costly downtime. What are the steps needed to develop an effective safety program, and how can managers convince their staff to achieve compliance?
Lab Manager recently hosted industry experts who spoke on these issues and more during its Safety Digital Summit. Industry experts shared their personal experience and stories to help you achieve a safer lab. Learn the steps you need to take to properly assess levels of risk in your lab, keep your equipment in working order, and recognize signs of distress among your staff and yourself. Watch for free on-demand to gain the valuable guidance you need as you improve your lab’s experience and create a safer environment.
Hello everyone, and thank you for attending Lab Manager Safety Digital Summit. My name is Michel and I'll be moderating this discussion today. Welcome to this session on fivefold proof Ways to make your Lab Safety culture flourish. Please send us to your questions or comments at any point during this presentation. Our speakers will address these questions during our q and a session following their presentation. To ask a question or leave a comment, simply type your query into the q&a box located on the right hand side of your screen. We'll try to address as many questions as possible during our time together. However, if we do run out of time, I'll forward any unanswered questions to our speakers. They may respond to you directly if possible, lab Manager would like to announce that the admissions to our Safety Excellence Awards are now open and available for entry. Please see the handout section for more information and direct link to our Safety Excellence Awards page to learn more. Additional resources and certificate for this presentation are also located on the right hand side of your screen. In the handout section, I'd like to remind you that the recording of this webinar will be available for free OnDemand viewing following the conclusion of this event. I would also like to extend a special thank you to our sponsors who support allows Lab manager to keep these webinars free of charge for our readers. So with that, I'd like to introduce our speakers for this presentation. Dan has more than 30 experience as a certified medical technologist and a bachelor's degree in medical technology from the State University of New York at Buffalo. As Stan, the lab safety man, he's the superhero of lab safety, providing onset education, inspection readiness and safety training for labs of all sizes, with a mission to help organizations everywhere creates safety savvy laboratories. And our second speaker for this presentation is Jason Na. He is a lab safety coordinator for Sentara Healthcare, a hospital system with laboratories throughout Virginia, North Carolina. He's an experienced technical specialist with a background in biotechnology, molecular biology, clinical labs, and most recently focuses in laboratory safety. Dan and Jason, thank you for joining us today. Well, hi everybody. My name is Dan Gio. I am a laboratory safety officer and also a laboratory safety consultant, also known as Dan, the Lab Safety Man. I do some consulting, teaching onsite audits, and always answering questions that people might be asking about laboratory safety. My goal is to make your laboratory a safer place to work. And I'm Jason Nge. Uh, my background is in clinical laboratory science or medical laboratory science. I have since moved into the realm of laboratory safety. I am the laboratory safety coordinator, support coordinator at Sentara Health. Today, we're gonna be bringing to you five foolproof ways to make your lab safety culture flourish. That's right. And the objectives for today are to maximize safety goal achievement through a process-focused approach. We're going to improve lab safety culture through discussion, and we're gonna revisit p p E usage. And finally, we're going to expand lab leader participation around lab safety issues. Right? So why are we bringing this to you today? Why is lab safety and improving your safety culture important? There are a lot of reasons, but there are a lot of whys that have happened in laboratories out there. The first major one we wanna bring to you today, you today happened 15 years ago, uh, at the University of California in Los Angeles. A student was working on a chemical synthesis in that laboratory. And one of the reagents she was using, uh, was something that ignited spontaneously when it comes into contact with air. It was probably only the second time she had used that hazardous substance when she was transferring it using a 60 ml plastic syringe. And according to her lab notebook, for unknown reasons, the plunger came out of the syringe and the chemical inside was exposed to the atmosphere that ignited started a fire on her clothes. Uh, she was wearing nitro gloves, no lab coat, no eye protection. Another person in the lab tried to use the lab coat to smother the fire, uh, and they started pouring water on her. But, uh, there were too many burns. And that employee, that student, uh, unfortunately did not survive that incident. It was a research lab accident, and it became quite famous, uh, and started, uh, a look into lab safety around the world. Yeah. And in some instances, uh, and incidences are not caused by an instantaneous action or some spontaneous reaction. Some are actually the result of growing issues in the lab that weren't addressed in a timely manner. For instance, in 2018, a 32 year old engineer died, and three others were injured when a gas cylinder exploded at the aerospace department's laboratory at the institute, uh, the Indian Institute of Science. Now this explosion was massive. It sent shock waves throughout the building, shattered windows, and even the roof. Now the explosion is believed to have either been a gas leak or a fluctuation in pressure in a high pressure hydrogen cylinder. Now some issues can grow and those dangers can creep up. So if a system goes unchecked, that small, that small issue might not be caught in time. And this is proof that routinely monitoring or not routinely monitoring your physical environment and lab can have some pretty devastating consequences. In 2018, in another laboratory in Pennsylvania, uh, there was an employee who was found unresponsive in the laboratory. And when they, uh, finally got to the employee, they, uh, tried to revive him and they were unable to do it. He did not survive. What happened? Well, he was working with some potassium cyanide, uh, and that's of course a very dangerous substance. It releases hydrogen cyanide gas, which interferes with oxygen use in the body. And so whatever that, uh, lab employee was working with, they were not prepared for the danger of that substance. And there was an accident and that person did not survive the accident. Lots of things have been happening in labs over the years. Yeah, we can prepare for incidences. We can do physical environmental routing, make sure our instrument maintenances is all performed. But you know what? Sometimes there's going to be the unexpected. Like in August of 2020, hurricane Laura devastated the biolab facility in Westlake, Louisiana. Now here, this category four hurricane literally blew the roof off the facility and it allowed rainwater to enter the, the building. And in this particular building, it stored more than 450 metric tons of tri chloro iso cyan uric acid, or T C A. This is a product that's usually normally used in hot tubs and swimming pools as a sanitizer to either kill bacteria or algae just to keep it clean in large bodies of water, this chemical will dissolve easy and it's pretty stable. But when small amounts of water are introduced to, uh, the chemical, it does not dissolve. What it does is it, it undergoes a severe chemical reaction and it generates toxic chlorine gas and explosive nitrogen tri chloride. Now, thankfully, nobody was injured in this incident, but the fire and the toxic gas that were generated and released caused a shelter in place for the immediate area. It closed a nearby freeway for well over 24 hours. And not to mention the closure of the facility, which was finally rebuilt in 22, but it came with a $250 million price tag. So it's important to make sure you have your emergency plans well defined, especially in if you're in a hurricane or tornado prone area. 'cause you never know what could pop up. All right, so those are just some of the publicized lab incidents that have happened over the past several years. But I bet if you think about it, you probably know of some others, some that have happened in labs that you know about some that may have happened in your own laboratory. Think about minor incidents, maybe that involve some injuries or exposures or some dangerous chemicals. What accidents have been happening in your lab. We wanna prevent those, and that's why we're talking about today, these five foolproof ways to make your lab safety culture flourish so that we don't have accidents like that. All right, so our first goal that we wanna talk to you today, I wanna impart to you that you should focus on the process and not the goal. Of course, we have goals, right? We live in a goal-oriented society. We strive to get the best house. That car we dreamed about when we were kids, the family, we always thought we'd have that salary. We think we deserve, or, or maybe, you know, we want the money for this vacation or to do that. We have goals. Uh, we have lots of different goals in our society, and we, that's just the way we live. That's how we focus. But also in our laboratories, we have a lot of focus on the goal. We have a lot of different goals, right? Turnaround time. Hey, you better make sure that it's lower productivity goals. Hey, make sure we don't have any mis IDs. If you're in some sort of a clinical laboratory, blood culture, contamination rates, Hey, we need those to go down. We need, we need lots of different goals that we have in the laboratory. We have to hit those monitors. So we live in a goal-oriented environment at work, and we live in a goal-oriented society when we go home. So we're always thinking about the goal, but that's not what we should be doing. What we should be doing is focusing on the process. So when I, uh, first started working in the world, I was a cashier in a grocery store, and, uh, I had a goal. I wanted to get rid of those people in my line. I wanted my line to go down, uh, because, hey, if I could, uh, have fewer people in line, uh, I could get a break more often, a little bit more downtime. But, you know, sometimes you could work as a cashier for eight hours and your line never ends. It just keeps going and going. So really, I should have had a focus on the process. And that meant focusing on the customer that you have now, not clearing the never ending line. If I'd done a better job with that, paying attention to that customer, paying attention to their needs, one at a time, I would've been a better cashier. What could I do to move one step closer to my goal of clearing the line focus on the process the customer I have right now? Yeah, this mentality works great in life too. So, take for example, dieting. What can you focus on today when dieting? So if you weigh yourself right now, go work out for an hour or two and then come back and reigh yourself. Do you think you're gonna see immediate results? Of course not. So rather, why don't you ask yourself, what's one thing I can focus on today? And that dieting example, if you focus on the process, focus on caloric intake, exercise routine behaviors, you'll find yourself getting closer to the goal without even focusing on the goal. You know, sometimes when we focus on the goal, we can actually set ourselves up for disappointment. So take for example, someone who's goal oriented and work in that chemistry bench. Eventually, if they stay in that mentality, they're gonna become disappointed. If they keep that in their minds, focusing on the goal, like Dan, with the, with the checkout line, focus on the process, focusing on getting those qc that QC in, getting those samples on, and you will eventually reach your goal. So while we're talking about focusing on the process, I do wanna look at one specific goal and kind of, kind of do a little sidebar with it is zero injuries and exposures in your laboratory, a realistic safety goal. And you know that there are people who think that it can't be done. Hey, we work with human beings. Uh, people make mistakes. There's no way you can work in a laboratory and never have any injuries or exposures. And I would question you there, if that's your argument, are you really having a safety mindset? If you don't think a zero goal is possible, do you really believe that there's no way to overcome safety issues and human behaviors? If you saw a laboratory who had zero injuries or exposures over a few years, would you believe it? Maybe you wouldn't. Uh, it's, you know, injuries and exposures and looking at the goal, it's always a lagging indicator, right? Because those have already happened and you have to respond to them. It's always better to have leading indicators, and we'll talk a lot more about those later. But I want you to think about your mindset when it comes to having a goal for injuries and exposures and incidents in your lab. Can it be zero? Think about that as we move ahead And as we're talking about focusing on the process. Uh, I want you not to live in a fast food world. What the heck does that mean? Well, don't try to tackle too many projects at at once and keep going, uh, over and over from one project to another, and bouncing back and forth. You're not going to get any kind of proper focus. You're really biting off more than you can chew. If you have multiple, multiple safety goals, multiple safety projects, you're not really gonna be able to get them all done because there are too many things you're, you're focusing on at the same time. Pick one, prioritize and start working on that, right? And don't forget the condiments, right? Don't forget the things that make it good. Keep your attention on the details. If you put, uh, mustard mayonnaise on your hamburger, those are the details, right? And so, if you make a great safety policy change, that's what you're working on. Don't forget to communicate it. That needs to be part of your project. If you have an action plan for a safety project, include all of the details that make the project go smoothly. Know your complete process. That's gotta be in place in order for that project to be completely successful. And also, I would say to you, while you're focusing on the process, savor the experience. Enjoy the ride. Be a part of the excitement. That's really, uh, in making safety improvements in labs. You're protecting people. You really are a hero when you're doing this kind of work. And if you keep your focus on the process the whole time, those results really will follow. So our second foolproof way to make your lab safety culture flourish is to be where the action is. Now, I want you to ask yourselves, where is the action that forms the safety culture in your lab? Now, Dan and I are lucky to travel once or twice a year to to speak or maybe to go to a different conference. And one of the things I love to do is to ask our Uber or Lyft driver, Hey, where's a great place to eat downtown? Now, 90% of the time, our driver will say, oh, well, I really don't know that much about downtown I live. Let's say on the north side, I can tell you a great place to eat around my neighborhood, but it's 25 miles outta your way. Well, that does us no good here. We have a person going back and forth to the same area day after day, but knows very little about the great or maybe potentially not. So great things happening there. Now, the same thing applies to the lab. How often do you as safety leaders, be it a safety representative, a manager or a director, how often do you go down into the lab and sample the culture in your lab? So, can you truly be able to speak about the lab safety culture if you spend all of your time in your neighborhood? Just imagine how many managers or directors are locked away in their offices or the C-suite and they can't really speak to whether they have a decent safety culture. Look, we know you're crazy, crazy busy. Uh, there's staffing shortages, turnaround time monitors, performance indicators that, that Dan was mentioning earlier. There's a ton to do throughout the day, but you have to be present to see how it really is in the lab, and you have to be present if you want to make those changes. So how do you rate your lab safety culture? How can you determine that? Well, one way is to simply ask, you know, a quick assessment can tell you exactly how the team feels about your safety culture. So you can utilize maybe SurveyMonkey, Microsoft Forms. Just send something out, get some feelers. Now, if you send this to both lab staff and lab leaders, you're probably gonna get two different opinions. This is because they're, they're basically two different groups with two different people looking at things a little bit differently. And they're gonna have that mentality. So make sure when you take that information, you understand the difference and you act on it accordingly. So when you go out into the lab, you are gonna have a tremendous impact on your lab safety. Just by getting out there. You get a firsthand view, a firsthand look of just how things are in the lab. All you have to do is make rounds and be present. You don't need a cell phone, you don't need a clipboard. Just observe for one to two minutes, maybe walk around and measure and rate your culture. You know, you might be surprised at what you see when you really just focus on the lab. So when you're out on the floor in the lab, how do you present yourself? Do you don a lab coat? Do you have on the correct shoes? You know, it's best to model the behaviors you expect for your staff. Take for example, if a manager goes into the lab and let's say, pulls a report from the chemistry analyzer and does not wear gloves, what kind of message do you think this is gonna send to the staff? You know, they're probably gonna think, well, if they don't need gloves, then neither do I. Or perhaps even worse they may have in their mind. Well, I guess safety policies and procedures really don't matter around here. So it's essential to set a good example and have that example when you go out into the floor. That's right. And the third way to work on your lab safety culture is to lower those power distances in your laboratory. Now, you might be wondering what power distance is, and that is when you have different people with perceived different positions, uh, considered like lower and higher in the department. So you might have a medical director or a professor. You might have a, um, a bench technologist who's working at the bench, uh, a lab assistant, a phlebotomist, depending on what kind of lab you're working in. And everybody has a different job level. And there are some older perceptions out there, and some people are afraid to speak up to somebody who's above them. And I'm using air quotes when I say that that's a power distance. And that can be dangerous when it comes to safety. So if the laboratory assistant's working on the bench and, and, and the doctor walks in and, uh, they're afraid to say something to the doctor about wearing p P e, that can be dangerous. That power distance, uh, that perceived power distance needs to go away. That's never good for safety. Everybody needs to be able to talk to everybody in the department about safety and coaching about safety. Yep. Another great way to increase your lab safety culture is to show your staff that you care. And, you know, there's no better way to show your staff that you care, especially about their safety, is when you act on unsafe scenarios swiftly. So it shows that you take the, the issue seriously and that you really wanna, uh, make a difference. So if somebody comes to you with an issue, you want to take action right away. If your safety audit reveals maybe some stained ceiling tiles that could be a leak or maybe an electrical problem, show your staff that you care. Put a ticket in, remove that. Take that that unit off the floor if it poses a risk and let them know, Hey, wow, this, this is pretty unsafe. And I see them taking it off. They're making it safer for us. So that's gonna increase lab safety culture as well. It's gonna help lower those power dis distances in addition. That's right. And you're also gonna want to generate staff involvement in the lab as well. Encourage your staff to actively participate in maintaining your overall safety culture. Well, that might mean helping, asking your staff to help with physical environment rounds or shadowing with inspectors as you're doing audits or as other, uh, external inspectors come in. And also talk about safety stories during lab huddles or meetings, and bring up safety issues that you might notice. It's really important to constantly use the language of safety, but also to get all, as, as many staff members as possible involved in that conversation so that there's more involvement with safety and overall awareness raising in the lab. So I've had physical therapy a few times in my life. I've had a sore shoulder, a sore knee, and I was never really impressed my doctor would send me, and I was like, oh, that really didn't do a lot for me. But a few years ago, I had a total knee replacement. And when I went to physical therapy, that for me was really where the rubber hit the road for pt. Uh, it was excellent. I couldn't have serv, I couldn't have, uh, recovered as well as I did without the, the things that they taught me. They, they taught me how to walk again. They taught me how to use my knee. Again, things you never think you would need to relearn, uh, until you go through something like that. But it was really the essence of what physical therapy does for you and how they work. It was awesome. And I have a whole different perspective, uh, on physical therapists now. So what about in the laboratory? Where for you and for lab safety, uh, where does the leader need to be to see where the rubber hits the road? So in the lab, it's watching, what can you learn from looking around your lab and using your safety eyes? Where do you work? Are you in the office all day and not really getting out in the laboratory? You're not going to be able to see what you need to see. You're not really where the action is. So take a look around. You can learn a lot from just looking around. You can look at signage. You can look at the physical environment of the laboratory. Are things too close to the ceiling? Are aisles blocked? What other things can you see just by walking around? Can you see unsafe behaviors going on? Right? So if you're only looking at your indicators in your office, those lagging indicators we talked about before, you're too late. Um, there's a high reliability organization idea out there. It's called rounding to influence. They want leaders to be out there in the lab witnessing safety in action. That's being where the action is. So when things look good, praise your staff. When things don't look good, when you see unsafe conditions, correct that right away. Lead by example, look around, walk around. You might accidentally do some damage to your safety culture. Uh, you might not mean to do it. You could walk out into the lab and you just have to ask Johnny a quick question. But you walked right by Susie, who was doing some work without a lab coat on. You didn't mean to do that. You didn't mean to not mention anything to Susie, but you've inadvertently done damage to your safety culture as a leader. So you've gotta get out there, but you also have to pay attention when you are out there. We're gonna wrap up this section, uh, and talk about safety indicators, specifically leading safety indi indicators. So most lab safety programs deal heavily with those lagging indicators that Dan was talking about. So they look at safety incidences and they react to them, or they put them on some report that you're reading in your, in your office. So these unfortunately are after the fact. And these lagging indicators can be costly to employees and the lab, and they can even send a negative message to staff. Furthermore, if your incident rate drops, what? Hey, which, hey, that, that, that's a good thing. But unfortunately, you now have less data to review. So just because something doesn't make its way to the surface doesn't mean that it's not a safety issue and that it won't pop up in the next week or so, or month. So what are some leading indicators that we can utilize? So the first one we'll mention is meeting attendance. Do you think this is a solid indicator? Well, it is fact a leading indicator. And some may seem it, you know, maybe a weak measure. It's actually quite powerful. So are your safety representatives routinely going to their meetings? You know, at Sentara Health, we require our safety coaches to maintain a 75% attendance rate for our lab safety committee meetings. Okay? As managers, do you allow your safety representatives to attend these team, uh, these meetings? Do you make time? Do you cut out time on their schedules? So think about this. If you don't set aside time for training and learning, do you think that's gonna have a positive or negative effect on their safety? It's probably not gonna do too well. The next leading indicator is centered around safety audits. So in the study conducted by Carnegie Mellon University, they showed that organizations can use four different predictors for safety. And the first one is the number of safety audits. So it's simple, the more audits predict a safer workplace. So are you performing safety audits once a year? Well, if you're having safety issues, safety culture issues, a lot of injuries, that's probably not enough. It's easy to see. The more audits are gonna increase safety. Now that's provided, they're not done by pencil whipping. If you know what pencil whipping is, it's where they go and they just mark yeses for everything down the columns, just so they can get the best score. These audits must be honest. So you can't do any pencil whipping. The second predictor for a safer workplace is the number of people who perform these audits. Now, that doesn't mean you need to have five safety officers for each one of your labs. This, this can include people from outside of the safety realm. So for instance, our hospitals require physical environmental routing, uh, in all departments. You know, these are audit checks of your physical environment to, to look for any physical safety issues, lightings, electrical trip hazards, things like that. In some labs, safety, safety coaches perform this exclusively. But in others, managers actually assign a rotating monthly schedule. Now, what's the benefit of this? Well, here you have more eyes that are checking on the staff. And you know what? More people will be looking at that checklist and they'll then know what to be on the lookout for. So more eyes, fresher eyes looking for something means that an issue is more likely to, uh, to get spotted and then corrected. So the the last two predictors that we're talking about from this Carnegie Mellon study are negative predictors. The third one, uh, says that, Hey, if you have a workplace, uh, and you perform audits, but your workplace, your upper management insists on perfect scores, you know, that automatically creates a poor safety culture. Uh, we, Jason talked about pencil whipping, uh, that, you know, you mark every item yes on your score. But some people do that out of fear or because they know their leadership wants a perfect score. Uh, that's terrible because, uh, you're not going to catch any of your safety issues and your, your bad safety culture really is gonna flourish. And that's not what we want. The workplaces that encourage reporting real safety issues, of course, are going to have fewer safety incidents. And that last predictor on the study, it's kind of the opposite of number three. Uh, you might have some audits and you've got a workplace that lists too many problems, right? So you've got an unsafe environment. Let's say you've got a score, you've got a hundred different questions on your audit, and 90 of them are marked. No, there's a problem. Okay? So you've done an honest audit, but what that really means is that you've got safety problems that have been going on for a long time and they haven't been addressed. That doesn't do anyone any good. Uh, there's no point in, in keeping, uh, a record of audits where, where there's no responses or there's no follow up. That's not good. The, the, the workplaces that are going to be the safest are gonna be those with maybe a medium amount of safety violations. Then of course, those have to be taken care of right away. So you might've seen these, these letters, this little acronym before, but we, we put a little twist on it and we did that because the next full proof way to make your lab safety culture flourish is to emphasize and encourage proper p p e. Why? Because something as simple as p p E compliance can say a lot about your staff's opinion of safety. But it also says a lot about how willing you are to keep them safe. So first, you have to determine your P P E non-negotiables. And this is done by examining the risks in your lab and your expectations. So first, we have to determine the risk. And this is the good old P p e, uh, risk assessment. This is something that's actually OSHA mandated under their task assessments inside of the bloodborne pathogen standard. So do you perform these? Have you done one recently? Well, they should be done and performed annually. They should also be performed anytime you change instrumentation or change a process. Anytime you do that, you want to go back and revisit your p p E risk assessment to see if you're opening yourselves up to any risk. And just to make sure that you have that p p e there to make sure that you're covered. So next, let's, let's set the expectation with your non-negotiables. Now, we got the common things that we always see in the lab. Lab, coats, gloves, eye and face protection. We have policies on this, but what about other things such as shoes and clothing? So does your lab or your organization have a dress code or a lab policy specific around shoes? 'cause people try to sneak things in if it's not clearly defined in their SOPs. You allow, um, open toed shoes. What about open back shoes? Ballet flats. So you wanna make sure that your shoes, you know, include your shoe policies. Include things like no mesh. Nonabsorbent covers the entire top and back of foot when you're wearing 'em. And what about clothes? You know, do you allow Capri pants or skirts or, or dresses? You know, you have to take in, into consideration those with religious beliefs, head scarfs or, you know, they have to wear a skirt or a dress. And that's great. But you wanna make sure you include in those policies that hey, head scarfs need to be tucked in for safety so they don't get caught in instrumentation or anything like that. And that skirts and dresses are ankle length so that they cover the entire leg. Again, adding more protection for your staff. You know, one of the most common issues we see from clients is p p e compliance. So make sure you have things spelled out and written out. Those are your non-negotiables. So the first piece of p p e that we'll talk about is lab coats. Now, this sounds crazy, but we actually have to remind staff how and when to where a lab coat. Hmm, the lab can be a dangerous place. So we're gonna anticipate that this danger is everywhere and we're gonna wear our lab coat anytime we're in the lab. Now, there's no hard, fast rule about how long you have to be in the lab before you put on a lab coat. Um, you know, I know we've heard people, I'm sure we've heard somebody say, Hey, if you're gonna be in the lab for more than five minutes, you need a lab coat. Well, we know a lot can happen in five minutes. So if there's a risk of splash, there needs to be a lab coat. And this applies to managers and guests, especially. You know, you wanna set that standard high and model the correct behavior. So when you're wearing your lab coat, you're instructing your staff about lab coats. Make sure they keep it buttoned. Also, make sure their sleeves are rolled down overlapping the glove. You know, an unbuttoned lab coat or sleeves that are rolled up. They do nothing. You know, chemicals, biological splashes, they're gonna go right to your clothes or to use or to your skin. Another thing to consider is encourage lab codes to cover smartwatches. So smartwatches and other electronic devices have kind of been a workaround to the no cell phone policy that we have in the lab. So keep it outta sight outta mind, keep it covered. Uh, and if you do see staff utilizing, you know, their, their smart devices, uh, talk about it, mention it, say, Hey, there's still a chance of contamination, you know, with your gloves. So keep it covered. So let me ask you this. What surfaces in the lab would you consider dirty? You know, I can see whole blood when it's spilled on the counter, but what about serum or urine or c ss f It's pretty hard to tell if one of these, uh, products have made their way to the bench. So it's best to consider that all surfaces are considered contaminated. Yeah, so space might be limited in the laboratory and, you know, you might wanna have some, uh, clean areas where people can work. And I know we, maybe we have some, um, workspaces in the lab. Maybe a senior tech or a scientist has a work desk or a cubicle in the corner of the lab. Can you label this as clean? Uh, you can if you don't have any chemicals or biologicals near that area. But the person who's working there, they can get away without having gloves on. If you label the computer and the foam clean, but you still have to wear a lab coat, you're still in the lab and there's still a potential for something to happen where you might need the protection of that lab coat. So be careful about that. When you see gloves or, uh, being used on one contaminated surface, that means gloves always need to be used there. If you have a clean area marked out, uh, you wanna make sure you never wear gloves with those, uh, phones or computers. You can't have it both ways. And you do have to be careful. So if you see a questionable behavior in the lab regarding glove use, make sure you question it and address it sooner rather than later. So our last component of P p E that we're gonna talk about are goggles. During the pandemic, our hospital system required all employees to wear goggles or face shields at all times. You know, 'cause no one wants. I covid this eliminated the guessing around deciding when goggles were needed. This was great it, but did it prevent all blood or body fluid exposures to the eye? Unfortunately not. You know, looking back at the data, I was really hoping to see a drastic reduction in eye exposures, but we found no evidence of such. There were still exposures due to lacking of P P E, lack of wearing p P E. Now, we don't know how many potential exposures it prevented. So we're gonna stay positive and say it prevented a lot, but the data wasn't there, didn't go all the way down. So if your lab doesn't require face or eye protections at all times, when is it required? Well, most employees, you know, if you ask them, they'll say, oh, during capping and uncapping, which is great, but the risk of splashing and potential exposure, it doesn't go away just because you're not capping or uncapping. So let's take, for example, you're working in the chemistry area. You're probably loading an instrument, right? You're gonna put specimens into racks, you're gonna load those racks into a tray, then you, you're gonna load that tray onto the instrument. Well, we know racks can tip over. Trays get dropped. Someone could bump into you on your way to load up the analyzers. You know, all of these scenarios can, and you know what they do happen in the lab. So make sure you're using your goggles and face protection at all times. Now, what about instrument maintenance? Some people will say, well, I'm not working with an open specimen. So you know what I don't need. Eye protection may reduce, uh, the chance of biological encounters, but there's still a need for eye protection. You know, emptying waste containers, loading up those caustic reagents. Something as simple as connecting or disconnecting tubing can all have a potential for a splash. Bleach in the eye is just as bad as blood in the eye. So you don't wanna forget about those tasks and the risk involved and just make sure you're training and educating staff to anticipate those dangers. All right, so now we're up to our fourth foolproof method to make your lab safety culture flourish. And that is normalizing safety. What the heck does that mean? How do we normalize safety? Well, the first thing I want to talk about is, uh, normalizing failure, right? So one thing we can do to, to, to help ourselves is to talk about our failures that happen in the lab. I'm not talking about praising staff members, you know, when they're eating and drinking in the lab or wearing open toed shoes. What I mean about that is we need to accept and learn from the failures that happen in lab safety. No one in the lab is perfect. We've already determined that, right? We're human. No lab is without its safety issues. You might have an inspection that's revealing that your lab is storing strong acids and bases next to each other, or your hazardous chemical waste isn't properly labeled. Take this information and run with it. This is an opportunity for growth. This is an opportunity to learn and strengthen your laboratory safety program. So while you're doing that, you're also showing the people who work in the lab, your, your staff, your team members, that you're not discouraged, you're not mad that the inspectors maybe found something, whether they're external or internal inspectors. You're, and when they watch you learn from this and make corrections, your staff, the people who work there every day, they're more likely to bring up safety issues because you've sort of broken down that barrier of fear. Fear about talking about unsafe things, or fear about reporting unsafe things. You want that barrier broken down. So one way to normalize safety is to normalize talking about failure. So how do we go from normalizing deviance to normalizing safety? Well, let's start at the beginning. Safety should be one of the first topics introduced during new hire orientation. By starting off with training and educating around safety, you're actually setting a precedence and emphasizing the importance of safety in your lab. Maybe you do your new hire fire extinguisher training on day one. Perhaps take your new hires on a walk, walk their fire evacuation route, all the way to your muster location. Another thing that you can do is, uh, kind of boost things up when you're doing your computer-based training. You know, a lot of labs now utilize technologies. Their SOPs are online. They have these modules, these training modules, and it's great. But what do you do? You put somebody in your room, you say, Hey, go read these procedures, read these policies, do these modules, and then come back. Now, what do you think this says about the importance of safety in your lab? What do you think it says to that new employee? And really, how much do you think they're gonna remember? So one thing you can do is maybe try to break up those modules, have them do a couple, and then come out. And when they come out, ask them questions about what they learned or maybe turn it around. Ask them questions about, uh, or ask them if they have any questions about what they just read or what they just learned. Maybe ask them what they did in their previous lab or at their previous school. You know, the more engaging you make it, the more impactful that training will be, and the more likely they're gonna remember the things that they're reading and learning. That's right. And the other thing you can do to normalize safety is make safety, uh, incorporate safety into your policies and procedures in the lab. So if you, uh, are starting an instrument maintenance procedure, make sure you write in a step in the procedure to don that face shield or put on some goggles. If the last step of a procedure is dispose of waste and clean it, uh, with, with just, you know, clean the waste container with some bleach, write that in the procedure so the people know what to do and include the p p e that may be required for the process. Uh, there's lots of things you can do. If you're talking about wiping down the bench with 10% bleach after the procedure's done in the biological safety cabinet, make sure that that's included as well. Set that expectation and training. But while you're doing training, incorporate safety into those lab policies and procedures. Another great way to normalize safety is to simply talk about it. At Sentara Health, we begin every meeting with a safety story. And that's not just our safety meetings, our safety huddles, it's manager meetings, quality meetings, whatever. We started all with a safety story. Now, most of the time they are, they're work related, but sometimes we do get stories from the outside. The important thing here is that we're talking about safety and we're engaging others. You know, you should bring up those near misses, those great catches, but also talk about the bad incidences that occurred as well. You know, share those anecdotes. Those are excellent learning lessons. Help others learn from those mistakes so they don't make the exact same mistake. You know, the more you normalize safety into, into conversations, the more people will do the same. You know, it won't be forced, it won't be painful. You don't have to pull it out of people. These conversations around safety, Hey, they're just gonna come naturally. That's right. And finally, make it fun. We know that safety can be boring. Oh, I hate to say that, but it's true. Not everyone loves to sit around and talk about lab safety. So if, if you can make it engaging and make it fun, people are far more likely to get involved and take something away from your conversations about it. How do you make it fun? Well try some safety eyes pictures. Take some pictures with a lab authorized camera, uh, and post them and say, Hey, what's wrong with this picture? Use your safety eyes and find out what's going on here. Uh, share some images of maybe people doing some not so safe behaviors in the laboratory, and ask other people to determine what that is. Uh, you've got a picture of an overfilled sharps container, maybe a rip in a lab chair. What can people find? Make a contest out of it. Make a poster with multiple pictures and see who can find the most errors. There's lots of things you can do. Do you celebrate lab week in your laboratory? Hey, make some gains around lab safety, decorate. Have a lab coat decorating contest. Decorate some goggles or do something like that. There's lots of things you can do to make safety fun, interesting and engaging so that you can normalize safety throughout the lab. Alright, and our last method, our last foolproof way to make your lab safety culture flourish is manager buy-in. So if you work in a laboratory, no matter what kind of laboratory it is, you know that there's a different sort of hierarchy, a different arrangement with lab leaders, different people who are responsible for different things. This person, the lab manager, might not have any say about expenses. Uh, they, the person, the clinical lab assistant might not have any say in what we purchase in the laboratory, or maybe they do. But there's a lot of different levels of people making a lot of different, uh, decisions. And not everybody has the same focus on lab safety. You can't always blame them. Uh, like we said, it just depends on their position and their job. And sometimes you have to sort of help others understand what's going on in the laboratory and what's going on with lab safety, especially if they don't work in the department. Some upper leadership and some organizations never get into the laboratory. And so what are you gonna do if you need a change or if you need have to have a project done that involves, uh, safety or some kind of a fix that you need, but they don't understand it, you've got to get their buy-in. So it's important to manage up or get that manager buy-in. You have with sphere of influence, there are people you can influence. And if you're the one who's pushing for the safety change, there are ways that you can get others to buy into it as well. So the bottom line, don't forget about your sphere of influence. You're not helpless with getting these leaders to help make decisions about lab safety and help you get some changes made. So one thing you can do is create a presentation for them. Use slides, use a PowerPoint. When you submit a request to the organizational leadership, you need to make sure you've got solid good reasons for your change and why this is necessary for safety. So don't write in your presentation, Hey, you know, I really feel it would be nice if we could do this, or, you know, I think the lab would look a lot better if we made this change. No, those are sort of touchy feely and you're not really gonna sell your project with those kinds of thoughts. So you need to make sure you include real solid reasons why the current situation is unsafe for your staff and why you need the money to make the change for the project you're proposing. Money's important. So you have to talk about cost. A lot of decisions are based on numbers alone. When you're looking at upper management, that's how they think. That's what they're dealing with. And their job is like that. They sort of are forced to think about the money. So when you're assessing this and you're assessing your safety issue and the change you need to make, make sure you include the cost if the request is approved, but also include the cost. Hey, if the request is not approved, would there be a fine by an organization like OSHA if they saw this problem? Could there be in an injury or exposure with somebody who's working in the lab? And what are the follow-up costs for that? What other costs could be incurred in the long run? If you have to replace staff or you have to do some other workarounds because the safety issue isn't being addressed, think about all of those costs together. And remember lastly, in your presentation, use a picture. A picture's worth a thousand words. Sometimes the words alone, don't tell the complete story, especially to those who work outside the laboratory. That upper leadership, that administrative department. If they never step foot in your lab, they may not understand at all what you're talking about unless you use pictures. That's okay. A picture's gonna help you tell that complete story. So I'm gonna tell you an example story that I worked with once, uh, you know, if you've ever worked in a hospital or worked with a morgue, you know, it's an area with multiple ownership, right? Lot of people use the morgue. The nurses bring bodies down. They do that with the help of the security department. Funeral homes have to get in there. The medical examiner needs to get in there. Uh, if there's any sort of organ donation, uh, organization, they need to get in there and do some work. The pathologist in the lab might need to do an autopsy. There's lots of things that happen in the morgue. A lot of different people own it. Well, there's a situation, uh, in one, uh, hospital where, uh, there were multiple employee injuries near the old autopsy table that was in the morgue and in the storage box where the bodies were kept. It was a small, uh, body refrigerator. The pathologist went to hospital administration several times. They wanted to obtain funds and get an updated morgue. They really felt they needed it for safety reasons, but nothing was done for many years. So a new safety officer came in and she thought, you know what, I'm gonna use this process of managing up. She got her camera out. She took pictures of the old corroded autopsy table, uh, that was rusted, and people were getting cut on that table. And she took some up close pictures of that. She took some shots of the morgue refrigerator, uh, and the size of it and showing people, placing bodies on the upper shelves. When people were doing that, they were getting back injuries because the, the, the lifting was just so difficult with the size of the fridge. And so when she put her project together with those pictures embedded in that PowerPoint presentation, administration really quickly signed off on the money needed to update that morgue. They got a new autopsy table, they got a lift, a body lift for the refrigerator. It shouldn't have had to take so long. But with that manager buy-in with, with putting that presentation together the right way, they were able to get that action that they needed as, uh, so that they could update that more. Yeah. And not all projects come with a high upfront price tag. Like Dan mentioned. You know, you need to consider the downstream cost. What kind of fines are we gonna get? What do we have to pay if somebody gets hurt? Um, what are those downstream costs of not completing that safety related project? So for us, in 2021, there were a couple of spills and, and leaks at some hospitals within our system. And it was discovered that the response to these events were not the same at across the system. So our system hazmat committee was then tasked to perform system-wide education on spill response. You know, we went out to 12 different hospitals, provided some spill response training at various times throughout the day, try to capture as many people as we can. And we ended each of one of our visits with a spill drill. Now we utilize actors or like volunteer lab workers, and we were even able to call the spill overhead as if it were an actual event. We used water to simulate some type of hazardous liquid, whether it's methanol or formin or, or whatever. And we did this to gauge, you know, a couple of different things. We wanted to know how the departments responded, but we, we also wanted to see how receptive the learners were to the information that we just presented a few hours ago. And, you know, in fact, we did discover there was a lack of standardized response by teams, not only inside the lab, but outside of the lab. And here we saw an opportunity. We saw an opportunity to help not just the lab, but hey, we're gonna increase safety throughout the hospital. So we jumped on that opportunity. Now, lucky for us, we had a hospital VP representative on our hazmat committee. Hey, that's sphere of influence. And we knew we would have their support if we presented our findings in the correct manner. So when we did our spill drills, we performed evaluations, written evaluations, we submitted all of these results to our committee, and it showed the various ways that hospitals were responding. And with this evidence, we were able to clearly define that we have a need to standardize our spill approach. We kind of base it off of fire drills and evacuations. You know, staff need to know what to do, where to go, who to call. If some type of e uh, emergency comes up, well, this was a, a type of emergency that needed, uh, that education. We know that a faster response and that's gonna lead to less property damage. It's gonna impact our patients far less. And you know what? Overall, you're gonna spend less money cleaning up after that event. So we demonstrated the need for a system-wide s o p and continuing education training for, for our employees. You know, and our reasoning was the more you do something, the more you practice a task becomes muscle memory, you know, the better off you're gonna be when that real event takes place. Now again, we had something in place in the lab. We had a document specific to laboratory spills. So we thought we'd benchmark this, make it a little more general, uh, to the hospitals and office spaces. And we were very able to very quickly send it up through our document control teams and get it approved. Of course, with that support of our VP representative, you know, we were, we were able to demonstrate that we need this at new hire orientation. Not everybody knows what to do when there's a spill. There's a high turnover rates. So we need to get, uh, employees engaged and educated as soon as they enter our system. But we also knew that we needed to have a computer-based training module, uh, for continuing education that talked about what to do in various spill response scenarios. 'cause there's different types of spills. It's not just blood and chemicals. What about large volume spills? It's raining in the lab. That's not normal. We need to act fast and we need to show that this is something that we need to have education on. All right, so there's your five foolproof ways to make your lab safety culture flourish. I hope you can think of those and think of some others. Remember number one, focus on the process. Think about what you can do today to, to move one step closer to improving your lab safety culture. Yep. And in order to increase that safety culture, to make it flourish, you have to be where the action is. You gotta step outta your neighborhood. You gotta go downtown, you gotta go to the lab. You gotta sample what's going on. Otherwise, you're not gonna know if there's an issue. And how can you fix something if you don't know there's an issue? And if you know anything about the hierarchy of controls, you know that p p e is the last level of protection. It's the last thing there is to protect you from the hazard you're working with in the laboratory. So you've got to prioritize P P E. Make sure you're providing it and make sure your staff is using it appropriately. Yep. And we need to normalize safety. We need to normalize discussions around safety. Don't make it weird. Make it part of your everyday life. Talk about it during your huddles. Talk about it during your meetings. Get them talking about safety and it'll come naturally. That's right. And lastly, manage up for safety. Think about those people in the C-suites, in the administrative suites in your organization. How do you get them to move so that you can get a fix on safety? There are ways to do that. Uh, and there are ways to make that, uh, to, to influence them so that you can get those safety projects taken care of. Thanks very much Jan and Jason. At this time, we're ready to move into our question and answer portion of the webinar. A reminder for those of you who came late, you can send us your questions and comments by typing them into the q&a box located on the right hand side of your screen. This is another reminder to please visit the handle section on the right hand side of your screen for more information about this event. Let's start with our first question from the audience. So the first question that we have from our audience is, can you recommend any good safety audit template? Uh, well, yeah. I know you can utilize, uh, your cap checklist. You can take some of those items from the CAP checklist, and I believe it's the GP 17 Clinical Laboratory safety. Um, Dan, there's, there's a checklist at the back of that, correct? Yeah. That's a document from C L S I, if you're part of that organization, the Clinical Laboratory Standards Institute. And of course, like you said, the the cap checklist, if you're a cap accredited laboratory, maybe a clinical laboratory. There's a good safety section on that checklist as well. Awesome. Thank you so much. Another question that we have here from our audience is, I have a few staff members on off shifts that are not consistent with using their p P e. How can I get them to comply with our safety policies and procedures? Yeah, so there are a lot of different, uh, methods you can use. Uh, one of them is to make sure you're, if you have a laboratory that's operating 20 24 7, make sure you're visiting those laboratories, uh, in during those hours to see what's going on with that P p E use. And if you have a lack of consistency when using p p e, uh, it's time to do some education, it's time to talk about what the consequences are to not using that p p e. Now, there are actual studies out there with the C D C where people have been exposed to, uh, different organisms and different chemicals because they're not using their, their P P E. And if you look at data from the Bureau of Labor Statistics, they actually have, uh, information about actual lab, um, incidents and exposures that have occurred, and they know what the numbers are throughout the nation. Uh, it does happen, and it's time to talk about those consequences if you're not getting the compliance you need. Okay. Awesome. Thank you for that insightful answer. Uh, we have another question here from our audience, and it says, as a manager, I can control lowering power distances with my staff. How should I approach issues with upper management? And those not receptive to safety conversations? Power distance is a tough one. Uh, Jason and I have worked with that, uh, in a couple different in our organization and a couple others. You know, there are actually some other cultures in the world where power distance is really big in the airline industry. So the, uh, the copilot doesn't dare speak up to the pilot because of fear and that power distance, and that's actually created some safety issues and even airline, uh, crashes. Uh, so think about that. If you're having a struggle with that in your organization, it's time to have that conversation with upper leadership. It may be time to talk to them about what power distance creates, the negative things it creates when it comes to safety. And it's time to start having those conversations with an upper leadership and asking them if they'd be willing to accept any kind of coaching when it comes to safety, if they do enter the laboratory environment. Yeah, I I think it's great that you're, you're lowering that power distance and you're inviting others to come in and ask questions, but like Dan said, you know, maybe, maybe some of these upper management just don't see it, or are they even getting down to the lab enough? Invite them down, you know, and maybe have a discussion again, you know, to talk about it in your, in your one-on-ones. It's a great, great thing to do. Alright. Awesome. It looks like we have time for one more question from our audience from that final question is gonna be, I often see staff use their cell phones while working in the microbiology lab. I brought this up to our manager in the past, but it doesn't seem to have any effect on the culture. Any suggestions? Yeah. Uh, it's great that you're, you're talking about it, you're, you're working with the managers, um, again, maybe they don't see it or maybe they do and, and they may not understand it. Uh, I think it's great to keep bringing it up, have them see it firsthand, you know, again, lowering that power distance, see if they're welcoming it. Um, Dan, any more insight? Yeah, and maybe like you said, Jason, maybe they're afraid, uh, to say maybe, maybe employees are seeing it and they're afraid to say something to the manager or their coworkers because the power distance is the other thing you need to do in this sort of situation. Is it, it seems like there's a lack of education in the laboratory. People are doing something that's clearly dangerous, but they don't seem to understand the consequences. You know, the c d C has put out studies about, uh, lab employees who've been infected, uh, by doing things like using cell phones in the laboratory and they've actually ended up, uh, hospitalized with, uh, bacterial infections because of that unsafe behavior. So it's time to talk about those things we mentioned about, you know, telling safety stories, but you have to provide the, the education about consequences, real consequences that happen, uh, in the world so that they understand that those behaviors are not safe. Yeah. I know a lot of our policies and procedures don't allow cell phone use in the lab, but if you see somebody using a cell phone and nothing happens, uh, is your safety culture really allowing it? Your policies say no, but you're accepting it. So, you know, it's important to make sure that you, you talk about that when you're talking with your managers and, and bringing these safety issues up. Okay. Awesome. Thank you guys so much. Are there any final thoughts that you would like to leave the audience with before we close out? Yeah, I, I just don't want anybody to feel like you can't make a difference in your safety culture. If you're the only person who's thinking about safety in your laboratory, the only person who's concerned about it, you can make a difference as, as that lone person, uh, take any of these things that we talked about the today to improve the safety culture, that all starts with one person and that person might be you. You can make a difference. Alright, awesome. And with that, this brings us to the end of this webinar. On behalf of Lab Manager, I'd like to thank Dan Sgio and Jason Nay for all the hard work that they put into this presentation. And I'd like to thank all of you for taking the time outta your busy schedules to join us. I'm reminded that all of the presentations from the Safety Digital Summit will be available for free on-demand viewing, so please watch for an email from Lab Manager once these videos become available. Once again, thank you to our sponsors at OAS Corporation Lab, Conco Corporation, or Lab Inc. And Size Shield. This support allows Lab Manager to keep these events free of charge to our readers. Please be sure to stay tuned for our next presentation today at 12:30 PM Eastern titled, investing in Your Lab Safety, how to Choose the Best Biosafety Cabinet for Long-Term Success. For more information on all of our upcoming or on webinars or to learn more about the latest tools and technologies for your laboratory, visit our manager. Thank you for being part of our digital summit. We hope you.