Custom Fit: Future-Proofing Pharma with Precision Containment
Discover how leading pharmaceutical companies leverage bespoke solutions to optimize modern manufacturing processes
For decades, containment has been crucial in pharmaceutical manufacturing, ensuring product safety and environmental protection. However, the landscape is shifting. COVID-19 highlighted the need for rapid production, while the rise of highly potent active pharmaceutical ingredients (APIs) demands robust strategies to protect workers. Future equipment needs are set to undergo significant change.
The industry now prioritizes the swift development of new chemicals and products for early-stage trials, followed by the challenge of scaling production successfully. This shift towards flexible manufacturing demands containment solutions that seamlessly integrate with unique prototype equipment, ensuring worker safety and operational efficiency.
Two leading pharmaceutical firms recently turned to Plas-Labs, Inc. (Lansing, MI) to address the new reality of containment challenges. Trusted for over 55 years, Plas-Labs empowers researchers with innovative safety solutions, from cutting-edge lab chambers and desiccators to advanced animal care products. Learn how their commitment to custom design and extensive collaboration is elevating efficiency across multiple sectors.
Containment's role in next-gen eye health
Cataracts cloud the eye's lens, impair vision, and can lead to blindness if untreated. The evolution of cataract treatment from ancient “couching”—pushing away the clouded lens with a sharp needle—to artificial replacements known as intraocular lenses (IOLs) marks a remarkable advancement. These implantable lenses not only restore vision but also can correct common sight impairments such as myopia and astigmatism.
Modern IOLs are composed of biocompatible, foldable materials such as silicone and acrylic polymers. And as demand for cataract surgery grows—the global IOL market was valued at roughly US$4 billion in 2022 and is expected to reach US$7 billion by 2030—so does the need for advancements in lens design technology.
At Johnson & Johnson Inc., their MedTech division (J&J MedTech) focuses on developing innovative and personalized treatments for various medical conditions, with a particular emphasis on reimagining eye health. As part of their R&D efforts, J&J MedTech recently partnered with Plas-Labs to develop customized gloveboxes for the synthesis of next-generation IOL polymers.
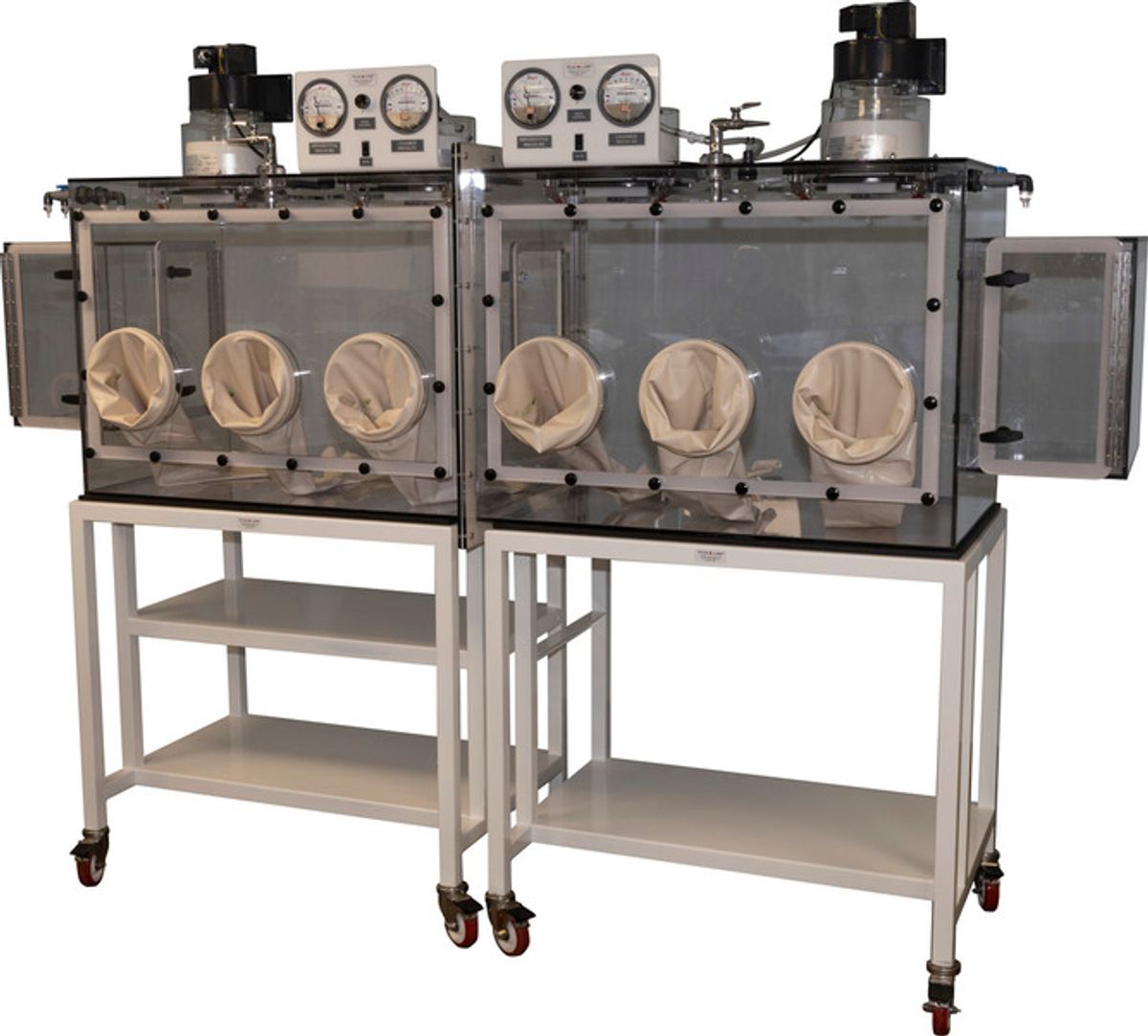
To protect scientists from exposure to monomer precursors during this delicate work, Plas-Labs and J&J MedTech envisioned a unique double containment system. The system features an inner box for reactions and curing, set within an outer chamber connected to the HVAC with at least 80 feet per minute face velocity for particulate and odor capture. The inner glovebox operates in an oxygen-depleted, nitrogen-pressurized environment to ensure safety and efficacy.
This was a 50:50 collaboration between Plas-Labs and J&J MedTech. Our main contribution was leveraging our accumulated experience in solving these kinds of custom problems.
Mirroring the essence of their work, J&J MedTech's researchers needed clear, unobstructed views for measuring and adding chemicals during polymer synthesis, requiring adjustments to perfect the viewing angle on the outer box's right side. Sufficient lighting plays a critical role, with LEDs mounted above and below the glovebox to ensure optimal illumination for the curing station.
The collaboration began with J&J MedTech sending pictures, measurements, and a full mockup of their gloveboxes to Plas-Labs for testing. The system process had to accommodate scientists' need for multiple access points and concluded with the purchase of two identical systems tailor-made for J&J MedTech’s specific research requirements.
The two firms have a history of collaboration extending over 25 years. Mike Regan, president of Plas-Labs, described their latest project as a balanced effort: “This was a 50:50 collaboration between Plas-Labs and J&J MedTech,” he says. “Our main contribution was leveraging our accumulated experience in solving these kinds of custom problems.”
While J&J MedTech has expertise in crafting their own inner gloveboxes, they turned to Plas-Labs for the outer enclosure's intricate design, crucial for achieving the necessary airflow for ventilation. Regan further emphasized Plas-Labs' adaptability: “We’re good at dealing with the ‘yes, but’ changes that inevitably happen in the design process,” he remarks.
Strategic containment for complex drug manufacturing
Hikma Pharmaceuticals, a UK-headquartered global company, has a significant manufacturing presence in North America, including one of the USA’s largest drug manufacturing facilities in Columbus, Ohio. This facility produces hundreds of solid dose, liquid dose nasals, dry powder inhaler, and high containment products. These include drugs with significant potency, such as antineoplastics and immunotherapies.
In the pharmaceutical industry, OEL (Occupational Exposure Limit) and OEB (Occupational Exposure Band) are critical for safe API handling. OEL defines the maximum airborne concentration of a substance workers can safely be exposed to during a 40-hour week, usually in mg/m3. OEB categorizes chemicals by toxicological potency into five levels, with Levels 4 and 5 for toxic and highly toxic materials demanding the strictest containment measures.
Trevor Adams, an engineer at Hikma, oversees all commercial pharmaceutical manufacturing and packaging processes at the Columbus plant, one of the few high containment facilities capable of handling OEB5-rated materials in the United States.
"We run a world class operation," Adams states. “Hikma’s Columbus pharmaceutical manufacturing facility is on the cutting edge—we handle a variety of complex tasks, primarily due to the stringent containment requirements and the complexity of the drugs involved.”
Integrating new equipment into an OEB5-rated facility requires strict validation to align with regulatory standards for containment and safety. This process includes SMEPAC testing (Standardized Measurement of Equipment Particulate Airborne Concentration) to check if pharmaceutical equipment can effectively control airborne particulate release, necessitating a clean room environment for accuracy.
“We test all our equipment with vendors before it's brought to our facility,” Adams says. “However, if a vendor doesn't have a clean room, we're faced with either constructing a clean room onsite or moving the equipment to an alternative testing facility.”
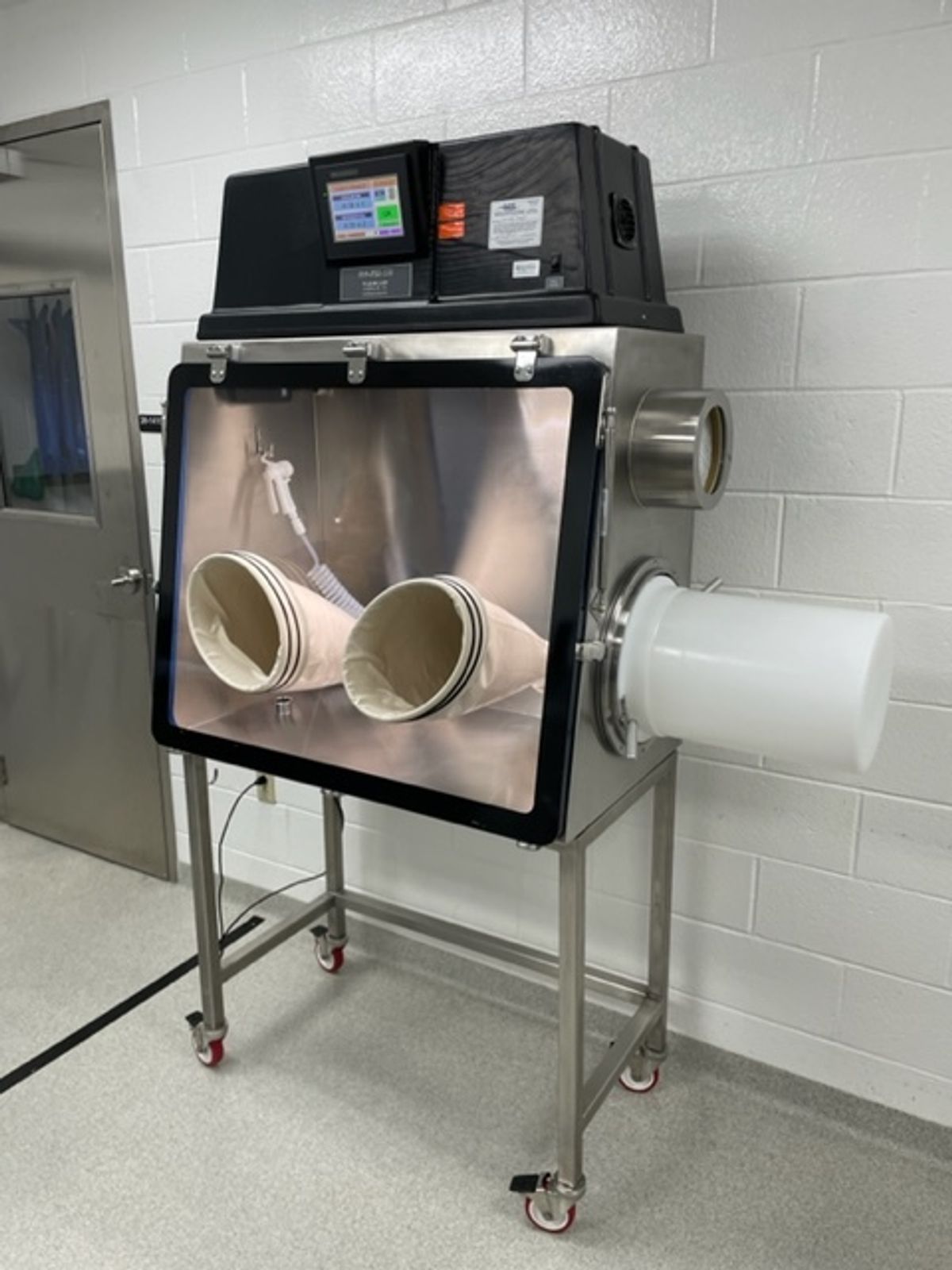
Faced with such a decision at an OEB5 equipment manufacturer in Belgium, Adams collaborated with Plas-Labs to create a portable clean room that could be directly shipped to vendors. This solution, integrating HEPA filtration for inflow and outflow and pressure control, ensured a contaminant-free environment for precise testing. The design featured HEPA filter adapters, a circulation blower, and sealed rings for secure material transport.
The new portable clean room continues to prove its worth for Hikma. For instance, the firm also partnered with Plas-Labs to construct a custom isolator for loss-on-drying (LOD) testing, a method for measuring the moisture content of pharmaceutical products. This LOD isolator, designed to be deployed into different clean rooms of Hikma’s manufacturing facility while meeting containment performance targets of 0.1 µg/m3, also needed to undergo SMEPAC testing.
Adapting pharma containment to new OEL guidelines
Customization in pharmaceutical containment is essential for meeting the unique safety and handling requirements of diverse products, especially with evolving regulatory standards. Tailored containment solutions for applications such as in-house testing enables capabilities, manufacturers to adapt quickly, ensuring each product complies with the latest safety regulations while enhancing operational efficiency.
“In this sector, there's a growing trend toward containment, primarily because of the uncertainty around OELs for new drugs during production,” says Adams. “One of my suppliers mentioned that major pharmaceutical companies are now opting for containment equipment across the board, given the initial unknowns regarding OEL.”
For those navigating the cutting edge of pharmaceutical manufacturing—where standard containment falls short—Plas-Labs offers a comprehensive suite of services. From initial design consultation and engineering, including CAD modeling, to oversight of manufacturing and testing of the final product, Plas-Labs ensures streamlined solutions without unnecessary complexity.
Start searching for your custom fit by visiting https://Plas-Labs.com/.