A New Lab Is Helping the Pharmaceutical Industry Safely Adopt New Workflows
The USP's Advanced Manufacturing Technology lab can help you safely move to a methodology that better fits your lab
In the wake of the COVID-19 pandemic, long-standing weaknesses in medicine supply chains became even more obvious. This has helped spur increased stakeholder interest in advanced manufacturing technologies—like pharmaceutical continuous manufacturing (PCM)—that allow potential efficiencies that can help increase geographic diversity in manufacturing and reduce over-reliance on the sourcing of medicines from just a few countries to improve supply chain resilience. However, interest in these new workflows has come with a host of new challenges for many pharmaceutical labs. Some small- to medium- sized facilities in particular may not have the resources, capacity, or expertise to easily take on these challenges alone. Fortunately, the US Pharmacopeia (USP) Advanced Manufacturing Technology (AMT) lab is on hand to assist in the development and qualification of new analytical methods required for new manufacturing processes, along with facilitating market access to quality medicines made with both advanced manufacturing technologies and traditional batch manufacturing.
A new facility built with researchers in mind
Now more than 200 years old, USP is an independent non-profit organization with a mission of improving global health. Towards that goal, USP helps supply quality medicines worldwide. Built as part of USP’s Global Health and Manufacturing division, the AMT lab began development in early 2021 in Richmond, VA. Designed to leverage the growing life sciences sector in the region, the AMT lab was built with researchers in mind.
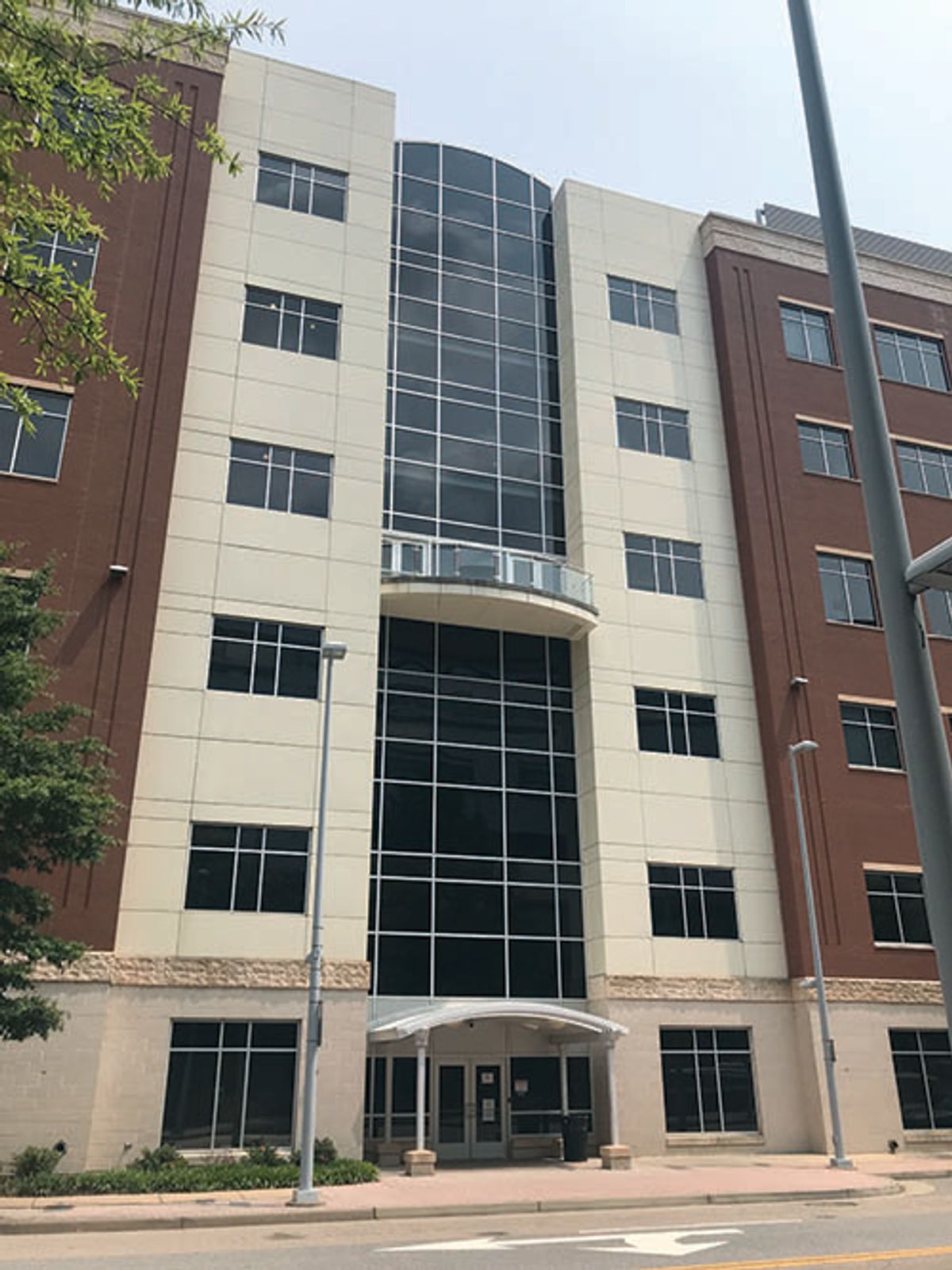
“[It] really was a scientist-driven design,” says USP’s Stephanie Mabry, PhD, senior manager, advanced manufacturing technology lab services. “There was a big focus on ergonomics and energy efficiency. [The lab] was designed for the work that would be done in the lab by the scientists.”
Mabry goes on to explain that the scientists were extensively consulted on the design of the facility so that it would be built for the researchers, rather than the equipment. “…There were a lot of meetings that we would have with the project manager…on what was going to be happening in this lab,” continues Mabry. “How people were going to need to move inside the lab, how materials would be transferred, so kind of doing the spaghetti diagram before the lab was built. A lot of times you'll have an existing lab, and then you'll do a diagram of workflows to figure out pinch points and any issues and we said, ‘Let's do that upfront.’ We put in a lot of thought on how we were going to work in the lab.”
Moving from batch methods to PCM
Upon its completion, the researchers and scientists at the AMT lab began their work in earnest. Their current focus is on analytical method development for active pharmaceutical ingredients (API) that are being converted to new methods, typically moving from a traditional batch manufacturing method to continuous manufacturing.
“One of our areas of expertise at USP is analytical methods for evaluating the quality of pharmaceuticals. So, we're building on that and trying to get ahead of the curve of when you switch from a batch method to more of a continuous method. For example, how does that change what the analytical methods need to do to ensure the quality of the API? Our initial focus is really strong on that,” continues Mabry. “We're also moving into process analytical technology (PAT) techniques and how those will be implemented.” PAT is a means of designing and assessing pharmaceutical manufacturing that focuses on monitoring parameters that impact product quality. This could mean, for example, assessing the needed criteria for a good PAT method with regards to a facility making the shift to continuous manufacturing from batch methods.
“Then we're going to expand from just looking at APIs to looking at drug products, reaction monitoring, and other aspects of pharmaceutical continuous manufacturing,” concludes Mabry.
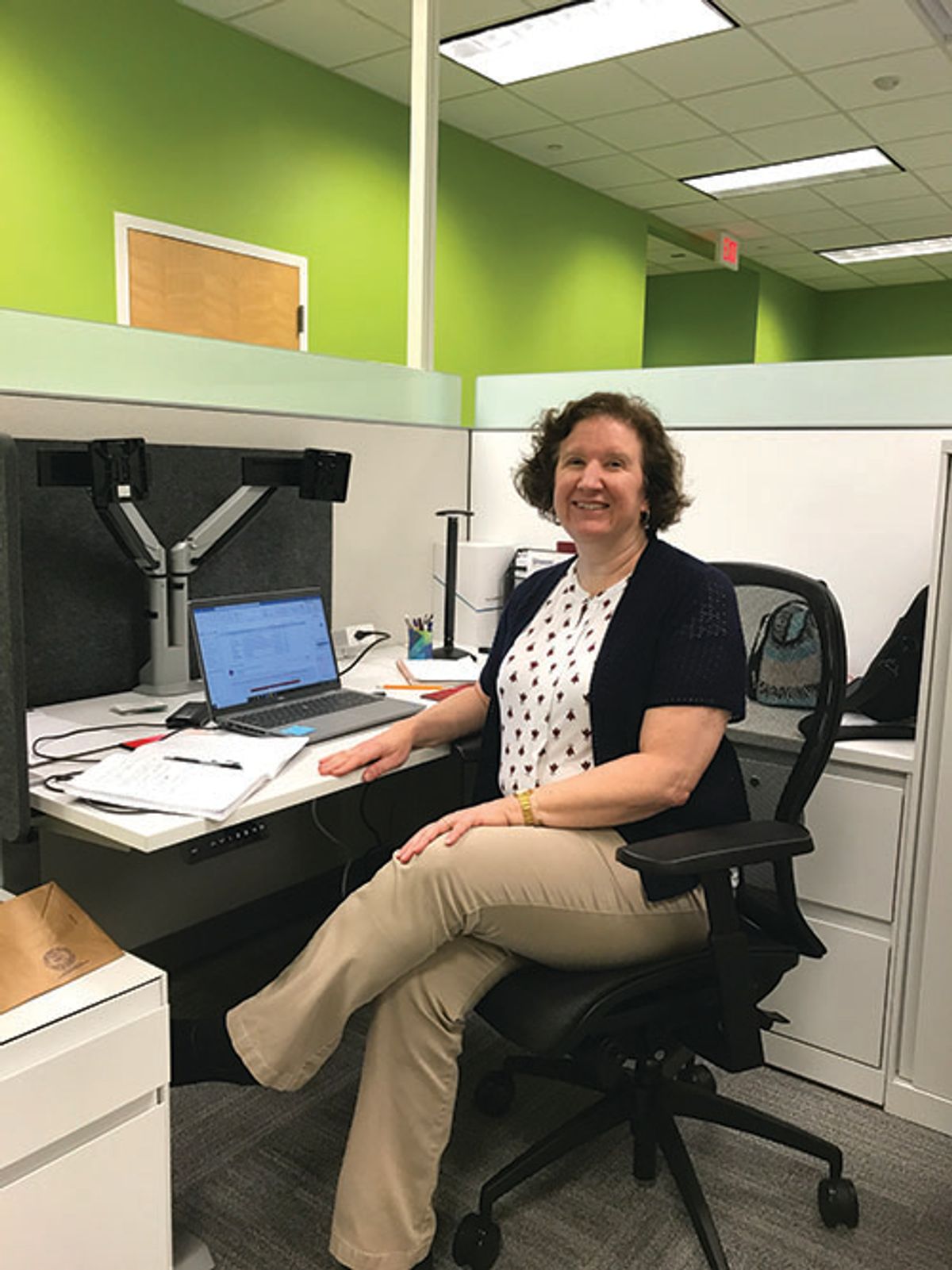
In short, the AMT lab is bringing USP’s 200 years of knowledge and expertise as well as state-of-the-art equipment to help the pharmaceutical industry develop more modern and secure workflows without compromising quality of the end product. “Our initial efforts are focused on supporting small- and medium-size pharma companies that may not have the resources to evaluate what's different about these new routes that they're going with from a quality monitoring perspective,” says Mabry.
Resources and equipment
In addition to leveraging USP’s years of experience, the AMT lab is also equipped with a wide range of testing and analytical equipment. This includes a full portfolio of chromatography instruments and mass spectrometers, ranging from single-quad up to high-resolution quadrupole time-of-flight (QTOF) mass spectrometers. “We can do full structure characterization…and then on the PAT side, we're really excited, we have probe instruments for doing direct reaction monitoring,” explains Mabry. “We also have a benchtop [nuclear magnetic resonance system], which we intend to use…with a flow cell for reaction monitoring. So, the idea is that you can actually take the measurements in the reactor in the vessel and monitor those over time.”
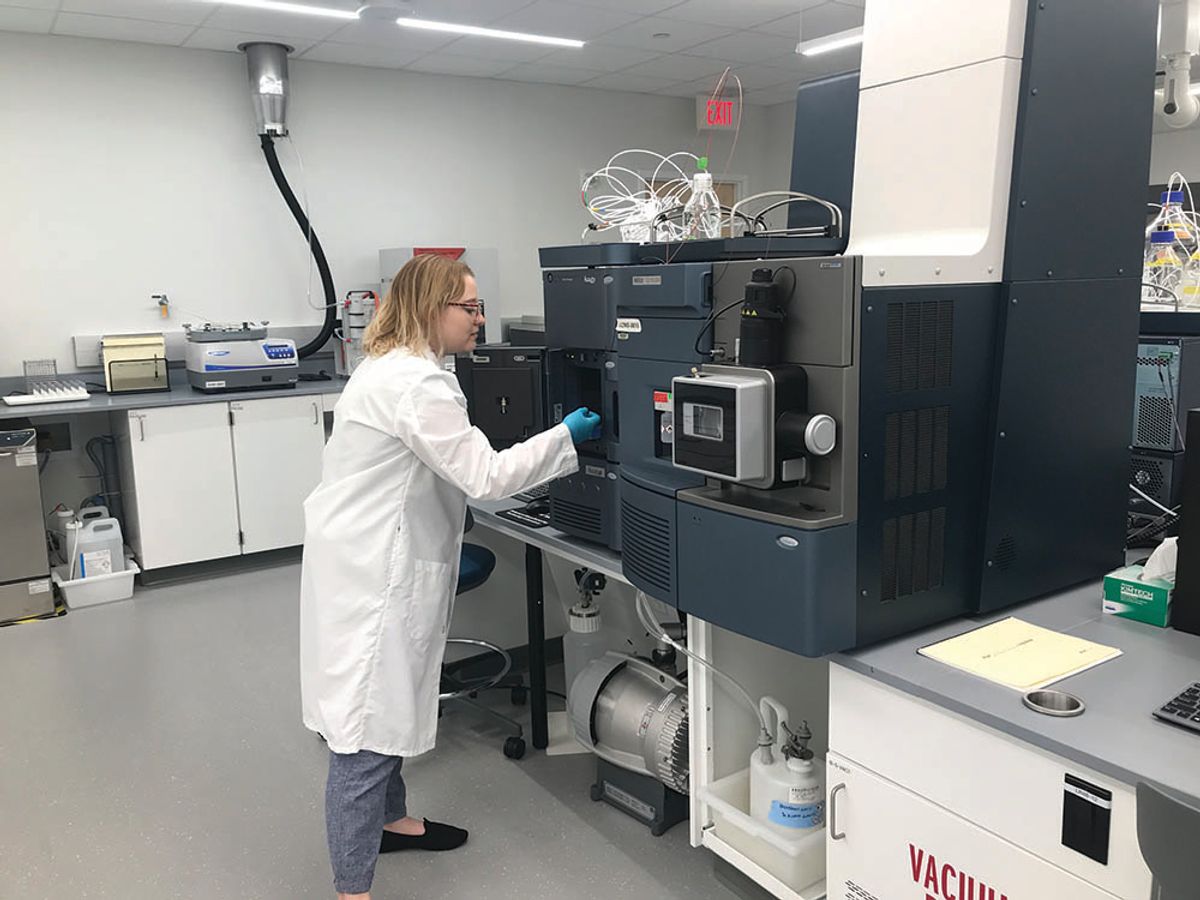
Current projects
The AMT lab handles a wide variety of different projects that can take anywhere from several weeks to nearly two years to complete, according to Mabry. “We have several projects that are collaborations on projects for developing continuous manufacturing routes for APIs that are considered critical for supply reasons. And we're also really emphasizing PAT method development.”
While much of the current work is focused on APIs, Mabry emphasizes that the AMT lab is eager to grow more in the PAT space and hopes to add more instrumentation to facilitate that growth.
Moving into the future
As the pharmaceutical industry looks to the post-COVID future and continues to innovate not just through the medicines they make, but also how they’re made, it’s facilities like the USP AMT lab that will help bring drug manufacturers into that new future. The knowledge, experience, and equipment that the AMT lab and USP provide can play an essential role in supporting innovation and supplies of quality medicines made with advanced manufacturing technologies like PCM.
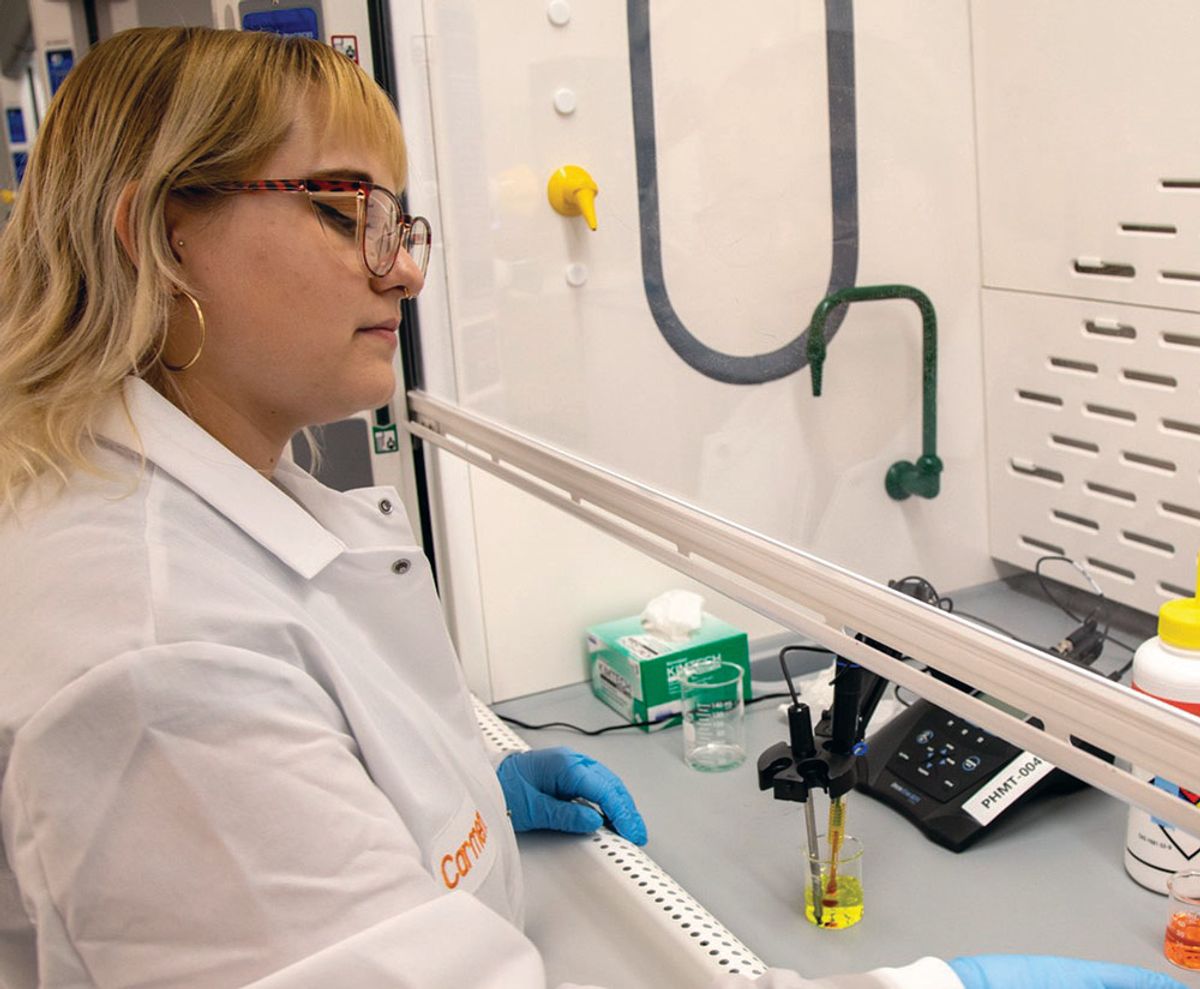
As Mabry puts it: “To foster supply chain resilience, we need diverse sources of supply, with more medicines, made in more places, using more manufacturing methods. USP analytical lab services can help manufacturers considering adoption of PCM to drive innovation, contain production costs, and optimize efficiencies in staffing and resources. These R&D analytical solutions can also help ensure availability of trusted, quality medicines made with PCM alongside those made with traditional batch manufacturing technology.”
On a more personal level, “it's exciting to be in a part of pharmaceutical development that is a new, vibrant field,” Mabry continues. “There's a lot of energy and that's really something that I like a lot. I've been involved in a lot in my career—a lot of lab renovations, a lot of team building. And what excites me the most about this role is it was combining it all together, it was lab construction, getting it set up, hiring the team, getting quality systems in place. It was kind of like all at once, let's do it all, you know? So, it had to be built in from scratch.”