Expedite Training, Technical Support, and Lab Design by Leveraging Mixed Reality
Increase efficiency with interactive video training, remote repair technicians, and holographic displays
While the capacity for remote work interactions was accelerated by the pandemic, the push for this shift has been stimulated by many global events. Companies are being mandated to reduce their environmental footprint, which comes with reducing travel and commuting costs for their employees. Enabling remote work has numerous other benefits including the ability to bring offsite repair technicians to the site of a repair virtually, as well as making onboarding, training, and mentorship of employees more efficient. The shift from in-person only to hybrid and remote work has pushed companies to be more creative than ever before in the way they structure their workforce, enable their employees to maximize their performance, and remove geographical barriers that previously limited potential. Mixed reality is a new technology that can enable all of these aims, saving time, money, and stress during seasons of peak demand.
Enter the augmented worker with AR/VR headset
Three new types of reality form the heart of emerging reality technologies. Virtual reality refers to a computer-generated simulation that immerses the user in an interactive, artificial 3D environment via a headset. Conversely, augmented reality projects holograms and other digital objects into a real-world environment, but is entirely contained within a screen. One application readers are likely to encounter are the product visualizers within a few big-name product catalogs that place 3D product models within their real environment using a device's camera. Mixed reality is a blend of holograms and the real-world environment via a headset, providing a more immersive experience than AR. This creates a seamless integration that allows users to interact with the real world and contextual holographic supplements.
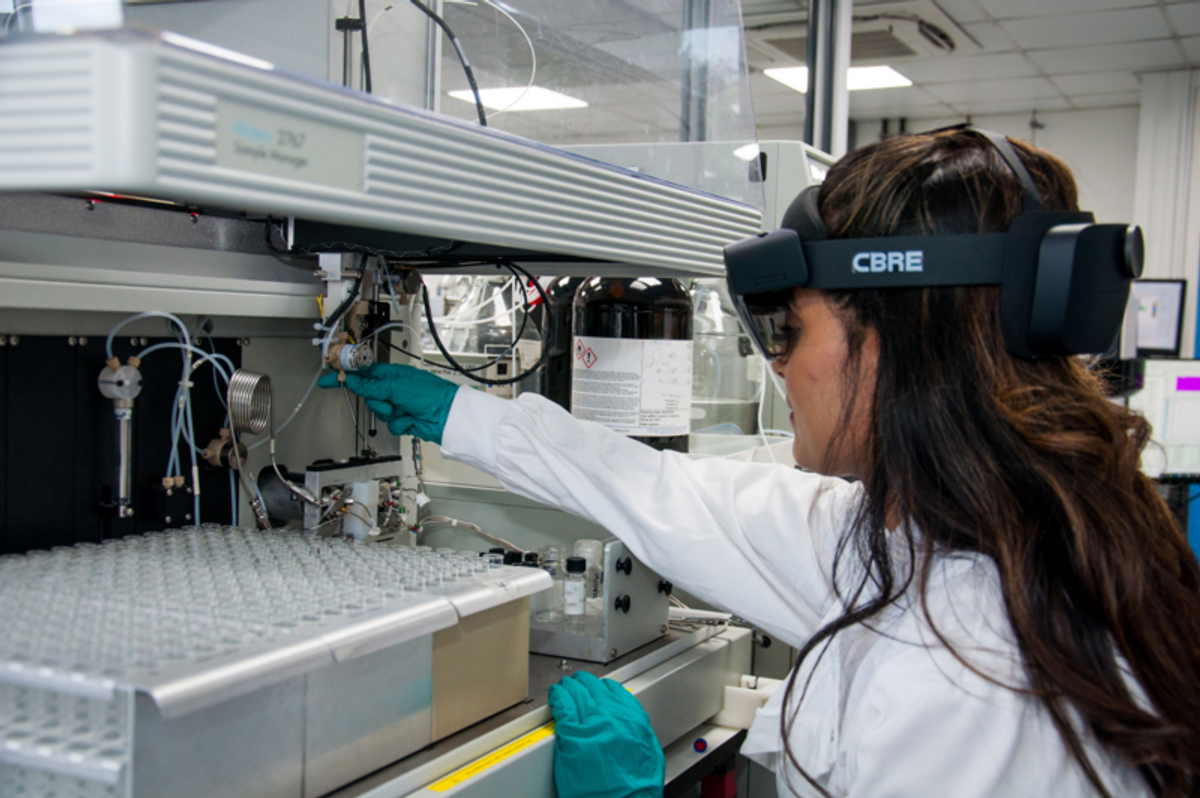
The augmented worker is one who works in the crux of technology and the physical lab enabled by mixed reality. They are more productive, able to navigate beyond limitations of geography and traditional resource formats. They can drive equipment repair from offsite locations, can create interactive training and onboarding resources that offer thorough and consistent training with reduced demands on staff, and effectively design laboratory spaces by overlaying plans on existing infrastructure.
Mixed reality headsets offered by Full Spectrum Lab Services from CBRE provide this mixed reality solution. The headset allows the user to hold a feature-rich live chat with off-site individuals that can achieve goals previously requiring in-person visits, circumventing the need for travel. The system integration enables existing training documents or equipment manuals to be referenced by the user in the same field of view as the equipment along with 3D models, video streams, and additional references to facilitate learning new techniques or troubleshooting problems. Mixed reality brings the technology of tomorrow to the lab of today, reducing down time and complications that frequently arise in all labs.
Mixed reality can aid in onboarding, repairs, inspections, and even planning new lab spaces
Case study 1: Training without physical staff
Last year, Morgan had to hire and onboard a new laboratory technician during the lab’s busiest stretch. The disruptions to workflows for training additional staff hindered productivity, delayed access to essential equipment, and increased everyone’s stress levels. Morgan decided they needed an entirely new strategy, and explored the potential for mixed reality, technology they were already considering for other needs. She had her lead technicians integrate technical training guides with OEM support and recorded training videos for interactive onboarding using an AR headset. When they found themselves hiring once again during their busiest time the following year, the lab was prepared for onboarding the new hire. The training materials walked the new laboratory technician through many of the procedures in an interactive format. Morgan was relieved at how smoothly the onboarding went. They now had a solution that would save enormous time and effort with each onboarding, that they could see easily being adapted to training staff on new equipment, cross training, and any one of a dozen other tasks that regularly arise. Senior staff wouldn’t be responsible for training each new employee from start to finish, saving weeks of focus. It reduced demands on equipment time for training purposes. It also allowed new technicians to learn at their own pace, replay videos as needed to fully understand protocols, and get the most out of their time spent with senior staff when they needed greater clarity on complex issues.
Case study 2: The broken plate
George had dozens of 96-well plates they needed to scan with a plate reader before tomorrow to submit his grant proposal on time. Nineteen plates in, George heard a loud, grinding sound, and looked down to see an “error” message on the screen. George couldn’t wait days for a repair technician to arrive on-site. Not only would they miss the grant deadline, but with their only plate reader down, other experiments in the lab would come to a standstill.
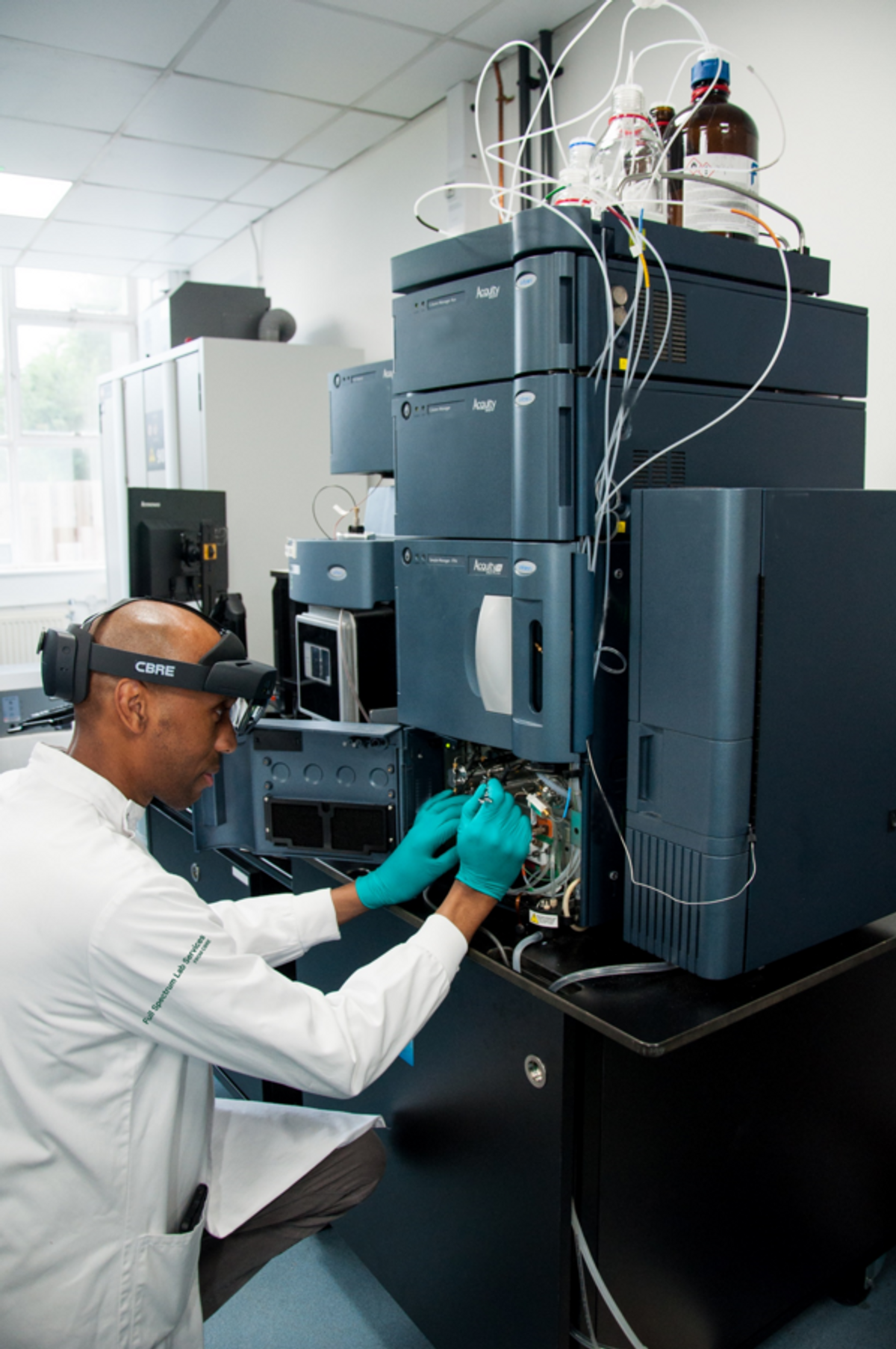
Thankfully, George’s colleague reminded them that they’d just received an MR headset from their new Full Spectrum Lab Services provider, who covered support for several instruments including the plate reader. George was able to quickly connect with a remote repair technician, who walked him through the full process: performing the diagnostics, removing the jammed plate, and the cleaning and reset steps needed for the machine. In what felt like no time at all, George was scanning the rest of the plates, back on schedule with no further delays.
Case study 3: Designing the ideal lab space
Brenden was thrilled to be redesigning the lab, after many long years of working in an outdated space. Using a mixed reality headset made it very easy to see where equipment would sit, and how it would fit into the existing infrastructure. As they performed MR walkthroughs of the space, Brenden realized that they had placed two of their busiest machines beside each other, creating an uncomfortably crowded area. They had also placed the reagent fridge too far from the biosafety cabinet. After some quick revisions and one last walkthrough, Brenden was able to generate new blueprints for a highly functional and efficient laboratory.
Mixed reality can reduce expenses, work, and stress
Mixed reality can assist with a variety of tasks in the laboratory. It can reduce delays and their associated expenses, make the laboratory more efficient, and improve the training experience. Using mixed reality can take the guesswork out of planning, and the waiting out of the laboratory work. This can help labs meet funding, environmental, and productivity goals without sacrificing the integrity of the work.
One company who used the mixed reality headset noted that they were able to provide more transparent service, saved over 112 on-site visits over only 18 months, and reduced 403 kg of CO2 emissions by reducing travel. The company saved over 7,000 consumables, secured more than 6 million samples, and saved a $500,000. Their clients reported improved reliability, their service reputation improved, and both their investor interest and output increased as a direct result.
While mixed reality seems futuristic, it’s already here, and those taking advantage of this technological advancement are reaping the rewards.