Ask the Expert Webinar
Available on demand now!
Maximize your workflow—even with limited space at the bench. This webinar features innovative solutions for streamlining the chemists’ everyday needs, including reaction monitoring, purification, fraction collection, and evaporation. No matter what your application, the session will address some of the most common bottlenecks and how to avoid them to improve your process.
In this webinar, you will learn:
- How to use TLC plates to make flash purification faster and more efficient
- Software hacks leveraging sophisticated algorithms for better purifications
- 30-second fraction ID to speed up the process
- How evaporation can be easier, faster, and more reliable
Speakers
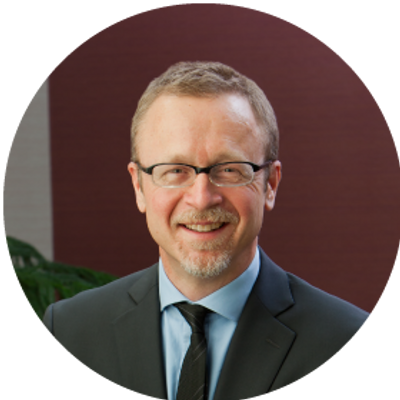
Gary Williams
Vice President, Chemist & North American Sales
Advion Interchim Scientific
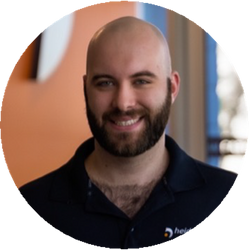
Nathaniel Kunzer
Product Specialist
Heidolph
Hello everyone and welcome to lead managers ask the expert webinar series. My name is Mary Beth de Donna and I'll be moderating today's discussion, streamline. benchtop chemistry faster workflow from reaction to fraction. We like our webinars to be very interactive, so we encourage you to submit your questions to us at any point during today's webinar. Our experts will address these questions during the question and answer session following this presentation. To ask a question or leave a comment, simply type your query into the q&a box located on the right hand side of your screen. We will try to address as many questions as possible during our time together. But if we happen to run out of time, I will forward any unanswered questions to our speakers and they can respond to you directly if possible.
I would like to remind you that this webinar recording will be available on demand shortly following this presentation. So please watch for an email from land manager and how to access this free video once it's available. I would also like to extend a special thank you to our sponsors at beyond intership scientific and high off their support allows land manager to offer these webinars free of charge to our readers. So with that, I'd like to introduce our presenters for this webinar. Gary Williams has over 25 years of direct sales and management experience and the life science instrumentation sector and has led several successful sales teams in Europe and North America. Prior to joining IBM, he was general manager Europe for biotage and has also held sales and distributor management positions at PerkinElmer, silicon kinetics and contract instruments. He graduated with an honours degree in chemistry from Thames Valley University in the United Kingdom, and spent six years as analytical chemist chemist specializing in optical and magnetic resonance spectroscopy before moving into sales. Nick conserves in the North America is North American product specialists for all of hydrops products. He has spent five years working with benchtop and industrial size laboratory equipment for both research and process scale. He is based in the North American headquarters in wooddale.
Gary and Nate, thanks for joining us, Gary, please get us started. Thank you. Thanks for the kind introduction. And good afternoon. Good morning. Good evening, depending where you you may be, thanks for joining this webinar, delighted to be partnering with heidolph today on this webinar that combines the benefits of our two technologies in the process of benchtop chemistry from making something to characterizing it to cleaning it up to finally then evaporating it and making it ready for for next steps. And so given that the chronology of the techniques would start with mass spectrometry and purification, I will go first.
And that's what add the only addition scientific do. And then Nate comes from heidolph USA, who's very kindly with us on the line as well. We'll take over on the evaporation side of things when I've done so. I'm hoping you can all see my see my slides in so I'll get started so streamlined, benchtop chemistry, faster workflows from reaction to fraction. So in this webinar, we'll learn about how to use TLC plates to make flash purification faster and more efficient software tools with some clever algorithms, the better for purifications. And that's a part of that I'll spend a little bit of time on very quick and easy way to identify flash fractions, again to speed up the process. And again, Nate will cover the evaporation process how that can be made faster, easier, faster and more reliable.
So adding interesting scientific a quick bit of background, we deliver tailored solutions to improve customers most challenging identification, quantification and purification needs. And we offer a combination of mass spectrometry and purification technologies for complete reaction monitoring and purification workflow. So on the right, you'll see a collection of images centered around an image of a mass spectrometer, and these pieces on the outside represents some of the sample introduction techniques pertinent to the chemist, I'm going to be spending a little bit of time on three of them. First of all, the TLC IMS system, a product we call plate Express, which allows you to take mass spectra directly from a TLC plate without having to do any sample preparation. We'll also talk about the ASAP atmospheric solids analysis probe, which is a little dipping probe that you can dip into reaction mixtures, Flash fractions, which will be the thing I concentrate on for that technique today, and then also purification by a flash
SFC or prep LC ms, we cover all of those techniques and but I'm going to cover flash today. And heidolph Apologize for stealing some of your words and eight. Hi it offers a wide range of laboratory equipment including the high evap series of rotary evaporators. With an emphasis on the essentials, well thought out details with a focus on features and functions to facilitate every day laboratory work.
Okay, so in this presentation, the basics of flash, the versatility of multimode mass spec to break down the flash purification process into simple bite sized chunks, learning tips and tricks to make the most of your flash system and learn the fastest method to final product using intuitive evaporation technology. So flash foundations of flash chromatography and considerations for combined mass spectrometry techniques. So, I'm sure I'm largely preaching to the choir. But just in case I'm not flash chromatography flash column chromatography is a specialized chromatography technique that uses compressed gas such as nitrogen or air to pump solvent through a column.
The legacy technique is a glass column filled with a silica slurry. That's kind of old school these days, it still persists as a technique. But commercial flash systems such as ours, now, pre pack columns of silica and other media into plastic tubes to take the mess and the fuss out of doing that. It's the gold standard technique for fast efficient purification. It's available in a range of scales from using cartridges, the size of my pinky finger to something much, much larger that can purify hundreds of grams, and perhaps even more.
And it's a popular method for isolating isolation and purification of compounds from reaction mixtures and natural product extractions. But it comes with it can often be time consuming and difficult in the sample prep, the method building and the actual execution. So before in Flash, before you even get started, you need to prepare your sample and the legacy way of doing you do your reaction, you'll spot something onto a TLC plate, wait a bit, and then you might have to scrape the contents of that plate off, submit for LCMS before you even move on to the next step. So that's time consuming before you even get started.
Similarly, the method creation in Flash chromatography can be a labor of love as well. This requires some expertise in knowing what type of cartridge to use the size, what's in the plastic tube, what type of media you're going to use today, you will then need to tell it what solvents to use, you define the proportions of those if in fact, more than one solvent is required.
And if indeed, you'll be running a gradient, you might need to know how to define those, calculate the RF values, ie the extent to which there is separated on the TLC plate, which translates into the separation on a flash cartridge.
And you might need to make some adjustments if your TLC isn't very well separated. And then you might need to know which product on the TLC plate is which. So you can ask the system to design a gradient, or a separation that targets the thing you care about most and doesn't prioritize the other components there as well. So all of that equals effort, knowledge, time, and work. And then lastly, once you've purified it fraction ID so Okay, now you've purified it. Where is it? What is it? Which one is it. And so you'd have to calculate the fraction location, extract the sample, prepare a direct injection, and then wait for LCMS. And we say there's a better way than all of this faster, easier way is where we've taken the heavy lifting away from the chemist. And so in our streamline workflow, we're going to show you how fast mass spec tools mitigate the need for lengthy Sample Prep. So how we can go straight from a TLC plate to an answer, how we program the flash method faster how we can use some of the information that is resident on a TLC plate, for example, to automatically build you a method and then execute it.
And then afterwards, how to quickly identify a fraction to make sure you are in fact going to dry down the right one. How we can do that without having to do LCMS. And then lastly, how and this will be Nate's domain, of course, how we utilize fast evaporation techniques for drying down your final product.
So the the mass multimode mass spec with expression system, compact mass spectrometer coupled to the pure flash flash purification system, and high evap evaporation platform, that's going to be our route to success. So, experimental setup, and system configuration. So, the first of all the compact mass spec, that's the slightly taller device you see on the left in deep blue.
This is a single quadrupole mass spec, equipped with both ESI and or APCI ion source types. And for those who are not familiar with the alphabet soup that sometimes resides in mass spec circles. That's electrospray ionization and atmospheric pressure chemical ionization. And the short version is, with those two ion sources, you pretty much cover everything, there's almost nothing we can't ionize with those two, we have positive and negative ion capabilities. And we can in fact, do both in a single run if you're not sure which one to choose.
Two instruments, one that goes up to mass range 1200 and the other 2000, fast scan speed so that this would be compatible with very rapid chromatography techniques such as UPLC should you wish to, and sensitive down to very low levels of of reserving. So they're pretty powerful instrument.
What we do that is rather a departure to other mass spec platforms is we offer a range of sample introduction techniques. And it's not it's beyond the scope of this presentation to mention all of them. But the ones that are pertinent to the synthetic organic chemists workflow are those highlighted in red. So atop the plate Express, TLC IMS plate reader, then the ASAP probe, and then the flash system at the bottom. specifications of the flash system, we have a number of these, the one that gets attention today is the pure flash xS 520.
This operates up to 20 bar, and up to 300 mils per minute, which will probably indicate that this can purify quite a lot of material if you want it to. We have UV detection on this it can take multi wavelengths whilst also scanning. And there is also a version of this, which goes up into the visible range as well in the detector. The detector being used, of course to observe peaks as they elute from the flash column, prior to going into the Fraction collector, and the detector can be used to tell the Fraction collector whether to collect or not.
So basically, it's a streamlining of the of the fraction collection and product isolation process. flow cell fairly standard geometry there, we have a valve an automated four port valve, which allows you to toggle between standard liquid sample introduction or a solid dry load switch into the column as well. So we support both of those. And we go up to columns, as I mentioned, with that fly right up to 90 millimeter ID.
And this has got a pretty small footprint as well this instrument what we have in here, which is going to get more detailed mentioned in a moment, a couple of pieces of interesting intelligence, the TLC to flash app here, using your cell phone, you can take a photograph of a TLC plate that you used to that you spotted on a reaction mixture, random the TLC plate, you can take that develop TLC plate, take a photograph of it, and then Bluetooth that image to the flash system where it meets what we call the genius software. And that software takes over at that point, you tell it where the solvent front is on the image of the plate and the origin. You tell it which of the spots if in fact there are more than one and which is obviously likely to be the case. You tell it which one you care about so it will tailor its its workings to isolate that component has priority over the others and then it will execute that method for you. It'll even tell you what cartridge to use. So that's
You're huge time saving right there. So in this worked example, we're just performing a simple Suzuki reaction, combining bromo AnnaLena, and phenol boronic acid into the product shown on the right, which I can't remember what it's called. But it's that product. We monitor that reaction by TLC, taking our quotes at various time points, putting them onto a TLC plate, and then submitting those to the TLC ms platform to determine which spot is which. And then after that, we take that TLC plate, and submit it to the flash purification system using the genius software and the TLC to flash app.
And then we have a very quick way of identifying the fractions afterwards. So the TLC IMS system, this schematic here, little bit busy, but in actual fact is slightly simpler than it looks, we have a compact mass spec on the bottom left connected to an isocratic pump, that pump delivers an extraction solvent of your choice into a valve that switches between a TLC plate reader and directly to the CMS and when it's in its analysis mode, it switches in solvent down the TLC plate reader, which has made contact with the TLC plate washes off the spot of interest takes that spot through a fret, so you don't pick up any loose material from the TLC plate that would not be good.
And then pumped it directly into the mass spec. In in less than one minute, you get a spectrum of your TLC spot, and you didn't have to do any sample prep, no scraping. And somewhat fortuitously, in almost all cases, the amount of sample on a TLC plate is a pretty good match for the amount of sample that mass spec wants to see. So overloading is rarely a thing, ideal for multi user labs, simple to IE to use. And with any luck, and then slide or two, there'll be a brief video of that working.
So here, we see some fairly jagged looking profiles on the top. And this is the total iron current from an extracted TLC spot. So there's just the maximum signal over time. And the middle one where you might see on your screen a slight a small green underline period, we dragged underneath that to get the average spectacle which is sown shown at the bottom of the Brahma aniline. And you can see the characteristic doublet for bromine in there. So that gives us the spectrum of that TLC spot. So that's characteristic for that. And in a moment, at the end of the run, you'll see the spectrum also for the product. So those three humps that you see in the top are three successive runs. So you can just keep repositioning the TLC plate, inside the TLC plate reader, pressing the button to analyze, and it will just give you another profile. And you can keep doing that until you until you're done. So this should be a brief video of this working.
I've taken off the voiceover on this, in order that I can talk over it. So direct mass analysis of TLC plates. So this is the TLC plate reader. So the system is in the reader, you press a button the head lowers onto the TLC plate. So this is you'll see that again in just a moment, click head lowers liquid extraction happens. And through tubing, the contents of that TLC spot will arrive in the TLC plate, excuse me in the mass spectrometer moments later.
But after this, you can then take that same TLC plate once you've identified which spot is which. And you can say now tell the flash system, what to do. So what does the sequence of events here is you photograph the TLC plate and add a title for file purposes, indicate the origin in the solvent front. So in the bottom right, you'll see it's slightly difficult to see on this slide digitally, but you indicate where the origin is in the solvent frontiers. And you click on the spots that it's found and tell it which one you want you care about most. You tell the system how much to purify because it's not a mind reader in that room.
Spell it seems the TLC image, but it doesn't know whether you want to purify milligrams or 10s of grams. So you need to tell it that so that it can tell you what type size cartridge to use, you indicate the solvents that we use to run that TLC plate, because that will be used as the starting point for for conditions generation. And then you send the data to the pier refresh system, and then genius software takes over. This will calculate the RF values, it will automatically suggest the column size to us. And if you have the database of our columns loaded into the system as well, which we advise you do, it will tell you which cartridge to use as well. So it takes all of that guesswork out. It suggests the gradient and then runs it and following the run, you can quickly review the total UV profile using the touchscreen and find out where the fraction is. And then up next, you can identify the fraction using the ASEP Pro.
Okay, so this is just a summary of what I just mentioned. I'm going to jump past that. And so then, the final part of the short circuiting process here is the fraction idea less than 30 seconds using a dipping Pro. So you may be accustomed to doing LCMS. Once you've purified, and you have some fractions,we say no need to do that there's there's a simpler way using a dipping probe. So there's a little probe that uses APCI ionization, I'm not going to dwell on this. Now in fact, I'm going to jump right past this slide. ASAP probe uses a probe that looks a little bit like an Eppendorf pipette. Except that the business end is not a plastic tip it is in fact the closed end of a glass melting point capillary.
You touch that probe into your sample, which in the worked example we're talking about today happens to be a flash fraction, pull it out, and you push it into the entry port of the mass spec where it meets heated nitrogen that will vaporize the sample off the glass melting point capillary. And then a corona discharge pin, which I always liken to the sparkplug in a car, same kind of idea will charge that vapor and give you a spectrum in substantially less than one minute. So this is an ideal way of analyzing flash fractions, because when you dip the probe into the flash fraction and remove it, the majority of the solvent will just evaporate off the glass capillary at room temperature, certainly as you start to introduce it into the warm innards of the mass spec. And then what's left is your sample on the glass which then gets baked off and then then charge. So it's a technique that just lends itself very obviously to analyzing flash fractions. So you see on the left there poking out of the front of the mass spec next to the flash system.
And afterwards, after the run, we actually analyze flash fractions in the same way that we did with the TLC plate reader, we can just leave it running, leave the mass spec running, dip the probe into a sample and then into the mass spec and you get a spectrum. So the top one shows the the characteristic doublet of the brominated starting material again, and the bottom spectrum is the spectrum of the product, which happens to be the larger fraction on the right, so we made some as you can see, there's also some starting material left and both of those have been separated on the flash system and so this should show the ASAP pro doing its thing.
So here I'm just showing you dipping into a white powder but this could equally be the flash question or you can wipe it over the surface of fruit if you want to look at pesticides is a very versatile technique. Just go straight into the mass spec. No alignment is needed. The system stops you pushing the probe in too far. It takes you to the right place every time. So just wipe, dip and you go okay, so the summary of the workflow should be shown in this little video which I'm going to turn that sound off because that's annoying okay, we call it intelligent mass spectrum.
Tree and purification workflow where the two techniques are talking to each other. Okay, so we run a TLC plate faster than real life, of course, this has been speeded up. And we take the TLC plate, do TLC ms on it to find out which spot is which make sure that we're going after the right thing within Bluetooth that image, take a photograph of it rather on the smartphone Bluetooth to the flash system.
The fact flash system takes over the heavy lifting for you purifies it. And then at the end of the run, dip it into the flash fraction, the probe that is and then directly into the mass spec. So that's the summary of the two techniques mass spectrometry with those two accessories, the ASAP probe or the TLC plate reader, talking to and telling a flash system, what to do. So react, purify an ID.
So I've gone over time, I apologize, I always do that. I'd like to thank you for your attention and great pleasure to hand over to Nate who's going to share with us how Hydrox evaporation technologies are takeover at this point. So thank you, Nate. Over to you please.
Thank you very much, Gary. So following that process, we're going to have a product with a solvent that was used in the purification process that we're going to need to remove rotary evaporation is one of the more effective methodologies of doing so. So I'm going to give you a little bit of information on rotary evaporation process as a whole. Go into a few of the different methodologies for evaporation, and then a few recommendations and tips for further maximizing your evaporation. What we're looking at here is an example of a full evaporation setup. You've got your rotary evaporator itself, you've got a chiller that usually
is the companion to the rotary evaporator. If you're using a coil condenser, depending on what solvents are working with, you can also swap it out for a dry ice condenser, and then a vacuum pump which will allow us to pull a vacuum over the process to make it a bit more efficient.
So we're re evaporation the the main components that go into the order of evaporation are the heating of the heating bath. This will help facilitate the evaporation by getting us to the boiling point of our solvent, the vacuum that will be overlaid over the evaporation. And the purpose of this is to reduce the boiling point. So that one, we can have a bit more of an efficient evaporation run a little bit cooler of a temperature. But also it allows us to prevent thermal degradation of our product.
We will have the chiller component which will cool those coils so that we can re condense any vapors that go through and then we will have the evaporation flask on the far right side, which is where we will be putting our product solvent mix into and then the receiving flask on the left hand side, which is the collection of our residual solvent either for reuse or repurpose.
So when it comes to solvent recovery, there are a few questions we have to ask to try to figure out what our process parameters are gonna look like. First and foremost, what is our end product? What compound is it? Is end state a powder? Is it a wax and oil? Is it aqueous? Do we need to leave some of our solvent left for extraction of it from the flask? These are some of the kinds of questions that you want to keep in mind when going about your evaporation process.
And the next step after that is identifying what solvent it is that we're going to be removing. Is it a single solvent? Is it multiple solvents? Is it a low boiler or a high boiler?
Following that, now that we've kind of got those two questions in our mind, it's about choosing the correct evaporation style and glassware. Are we going to be using dry ice? Because it's a super low boiler? Are we going to be using a chiller to cool those coils? What kind of flasks are we going to need to use? What type of volumes are we working with? Do we need a small evaporation fast large evaporation flask things of that sort.
And then finally, once we kind of have all that in mind, we can kind of identify our evaporation parameters. Multiple different solvents have many different evaporation points, we need to know you know at what vacuum level we want to be at what heating bath temperature we want to be at. And we can start to kind of dial in those parameters so that finally we can begin solvent removal.
So first and foremost, like I mentioned, after we identify our solvent, and our end product and the kind of state it is we need to pick the correct glassware for the job. On the evaporation side, there are a multitude of different methods that we can use. First is to kind of determine what volumes are working at because we want to evaporate ration size to be about three times the size of our volume that we want to be running in that evaporation flask about a 1/3 fill level. The reasoning behind this is if we fill it past that, we will not be getting to use the full surface area of flask will have a large kind of base layer, where some of that evaporation has been going and then the evaporation over the top half of the flask.
But if we have a 1/3 level film, now we're using the whole curvature of the flask with our evaporation, and then dialing in if it's a liquid, a powder wax or a solid that we're running with at the end. As you can see, we have a flask with a removable lid. If we are working with solids and the end phase or a wax that we need to scrape out, there are spider flasks that are the ones that have the multiple flasks attached to what kind of looks like a cow water, or the same thing with the test tubes that allow you to do multiple samples at the same time, so long as they have the same solvents in them.
There's also powder and baffle flasks that really do a great job of flipping over powders, during the evaporation process to allow you to get a much more even dry, so that you have a quicker and more and more dry end product as opposed to going outside in we're kind of working through that whole powder. So first thing is to identify, you know what flask is going to do the best job for us in the evaporation phase.
And then going into evaporation itself. On the most basic level evaporation has a heat and a vacuum, the vacuum to adjust our boiling point and the bath temperature to facilitate that boiling.
Rotary evaporators added another component which is rotation. And that rotation increases the speed of evaporation because now we have a larger surface area to evaporate from because at the top level of a liquid. That is the only place where you're going to be getting the evaporation from it's not going to evaporate from the bottom of the flask it's going to work its way up and have a greater vapor pressure than the vapor pressure inside the flask and coming to a vapor. So those are the three main parameters that we're going to be working with.
Typically, you will need to use either some experimental methodologies such as testing different vacuum levels and heating bath temperatures. In order the dial in what is going to be most efficient for your evaporation process, you can consult the chart online in order to kind of get an idea of what different values your different solvents will evaporate off at. But we have a couple of more easy to use methodologies for doing this. The first is the addition of a vapor temperature sensor, which will give you a good idea of what your boiling point is because right on the flip side of the boiling point is the temperature that your vapor will be at. So that'll kind of allow you to dial in what our bath should be at and what our chiller should be at in order to facilitate an efficient evaporation.
What the hives also provide is a solvent library. So as opposed to doing guessing check in order to find your parameters. There's already pre loaded solvent library that can give you for doing ethanol, the bath temperature, chiller, temperature, rotation, speed, and vacuum pressure that you need to work with. Same with a cyclohexane standard hexane dimethyl ether, a wide variety of different solvents to kind of give you a head start and allow you to get right into your evaporation. It's particularly effective when you're working with multiple different types of operations, multiple different solvents, multiple different end products. And what's great is if you were to dial in your parameters further, those can also be saved so that they can be reused more readily.
But sometimes basic evaporation isn't the quickest and easiest methodology. For example, if we're doing a multiple solvent removal, you can't evaporate both solvents off at once, it'll go by the lower boiling point solvent, followed by the higher boiling point solvents followed by the higher if it's three solvent evaporation, for example.
What you can do with some of the more advanced rotary evaporators is with integration of the vacuum, you can create ramps ingredients. What this is is basically a time parameter that has different variables set for each predetermined amount of time. So we can set a rotation speed, a heating bath temperature and a vacuum pressure for the first solvent. And after a predetermined amount of time, it'll go then to a next set of parameters that will be set up for our next solvent. This is very effective for multi solvent evaporation, because now I know you'll now you no longer need to sit in front of your evaporator wait for the first to evaporate off and adjust the parameters yourself. I can all be pre programmed.
What this also provides is linear ramping. So if we have a product that is prone to bumping or foaming due to the application of the vacuum, we can actually set a ramp so that it'll more slowly pull down that vacuum level to get us there in a more linear manner. instead of a harsh poll, this is fantastic for preventing bumping or foaming. What it also allows us to do is in cases of powder drying, for example, is we can do a majority of the evaporation at the standard parameters for that solvent, and then do a gradient deep below the recommended typical parameters for that evaporation to ensure a very even and full drying of our powder in a substantially shorter amount of time.
Another great methodology is some automatic evaporation methods. If we're running in a lab that is constantly using different solvents with different mixes, it can become a bit much to identify all of those points in which the evaporation is the most efficient. There are a few automatic evaporation methodologies out there that can facilitate this in a much more simple way. With the high back rotary evaporator, for example, the unit itself will take control of the vacuum for you with a predetermined heating bath temperature and predetermined rotation speed to do all of the evaporation, whether it's single solvent or multi solvent without needing user input. It does this through facilitation of a temperature probe, which can basically take a snapshot of what the temperature is inside of our cooling coils, so that as that vacuum gets pulled further and further, a vapor will finally be created, which will trigger a temperature increase on that sensor and basically tell the system Hey, we'll hold the vacuum. Here we have evaporation occurring. And once that temperature drops back down, we'll begin searching for the next solvent. So this type of automatic evaporation is great when we're using multiple different solvents at multiple different points. And we don't want to be pre determining all these parameters every single time.
So with those kinds of methodologies in mind, I wanted to go through a few recommendations for maximizing the safety reliability consistency of our evaporation process. The first is the delta point rule. When in doubt, this is the best way to determine initial optimal conditions for our evaporator, we will start with a vapor temperature usually found either through a calculation or through a vapor temperature sensor within our unit, we will have a vacuum level that gets us this vapor temperature. And at that vapor temperature, basically our new boiling point, we can then adjust our bath temperature to start about 20 degrees Celsius above that, and our chiller temperature to be 20 degrees Celsius below that, that will get you a very nice initial stable condition for you to do efficient evaporation. And then once you have that starting point, you can you know, decide on if we need to be going a little bit quicker in our preparation to maybe crank up that bath temperature or speed up the rotation, it gives us a good baseline for what our evaporation process is going to look like.
The next very important thing to consider is our condenser usage. During rotary evaporation we do have that vacuum component. And during evaporation we are creating a vapor that will typically be cooled in that those condenser coils. Now if we were to over evaporate what the condenser can condense, we run into the issue of vapor being pulled through our vacuum pump.
Were using the the vacuum pumps that are PTFE diaphragm such as the vacuum pumps that provides the vacuum pumps themselves are incredibly solid resistant. However, you're still pulling solvent through the pump and potentially into your atmosphere where an operator can be harmed, or it could lead to corrosion on the interior of your lab or your fume hood. So a great rule of thumb. To minimize that and prevent it almost completely is to take a look at the condensation height basically where the liquid is being formed around our condenser coils. The rule of thumb is that the condensation should not exceed three fourths of the height of the condenser. By keeping it below that level, we're basically ensuring nothing is making it through our vacuum pump protecting the operators and the environment around it.
And then if we need to get more out of a rotary evaporator than what our standard flask is providing, say for example, we have three liters of volume that we're doing in a one liter flask and we don't have a five liter flask, we can make our process semi continuous. We can do this through an accessory such as a refill valve. Now given that the rotary evaporator is under a vacuum, what this valve can do is use that pressure differential to pull through the tube container of a product solvent mix into the evaporator while it's running.
There'll be a tube from that right side of that valve into the evaporation flask and a tube from the bottom side of that valve into that proximal mix. And by opening up that valve, the pressure differential basically pulls that product in our evaporation flask for us so we can continue to evaporate off the solvents
Add more products, all that mix in there, remove the solvents and do that continuously until we have a large amount of products in the flask that we would like to get rid of. This is also great from a safety aspect as some solvents, we want to minimize contact with as much as possible. So by using this, we're allowing the PTFE tube to contact with the solvent product mix as opposed to an operator leading to greater overall safety and efficiency in the process itself.
So that concludes my presentation on the evaporation process following your chromatography. I appreciate you all for coming in and listening.
All right, great. Thanks, Nate for that wonderful presentation. I'm going to invite Nate and Gary to join us for audience q&a at this time. If you'd like to turn on your cameras, Nate and Gary feel free to do so. Gary, let me get your mic on for you. Carry your mic is on if you want to join us for the video. Just let me know I can turn it on for you if you'd like.
I gotta God. Alright, we can see you, Gary. Hi. Okay, I'll make sure I don't fidget.
Alright, great. So thank you both again, for a great presentation. At this point, we are going to move into the question and answer session with our audience. So again, for those of you who may have joined us late in the presentation, you can send in your questions or comments by typing them into the q&a box on the right hand side of your screen. Even if you don't have a question, please leave us a comment. Let us know how you enjoyed this presentation. And if you found the information useful. So Nate and Gary, thanks again. Let's dive right into the first question here from the audience. This one says what types of TLC plates can you use with the plate Express?
Okay, that's a good question and quite a common one. So analytical TLC plates, as opposed to the thicker property of ones, they can be glass, aluminum or plastic backed doesn't matter. And we can also cope with different analyze from different types of media. So reverse phase, normal phase alumina plates, etc. So almost no limit to what you can run in it just just not prep plate is that the head isn't optimized for preoperative TLC plates.
Okay, great, thank you. Here's another one that says what quantities can be purified using the pure flash system. So it depends which type of cartridges you use, we have cartridges, smallest, like 12 grams, which would be used for, you know, 10s to hundreds of milligrams, right up to 1.5 kilogram cartridges, I think which could purify a lot more sort of, you know, 10s, or possibly even hundreds of grams, depending on the nature of the separation. On a slightly different instrument, we have units that go up much, much higher that are used in process. But in the lab, the instrument that we chatted about today would be in the high milligrams to low mid grams range.
Okay, great. Thanks very much. Let's go on to another question. If you scroll down a bit, unless this one says related to the TLC reader and the CMS, is there a limitation on the matrix of the TLC for example, silica base alumina base or chiral TLC matrix? Right. So to the to the first question, really same, same, same thing applies. So know that those TLC plates will work just fine in the TLC plate reader, no issue with those at all.
Okay, great, thanks. Let's go the next question at the top of the list here. What is the best way to control bumping and foaming? Oh, that's a great question, I can take that one. So with your rotary evaporation processes kind of quick summary of bumping and foaming, if there is too harsh a pull the vacuum or if the parameters are kind of uneasy for an evaporation your product solid mix might start to bubble over and foam over which can lead to it contaminating your selected solvent. In order to kind of prevent this. Our take is to adjust the parameters in the first place to prevent foaming and bumping from even happening.
This can be done in a couple of different ways. The first is by using a RPM regulated vacuum pump. And what that means is a vacuum pump that is smart in that it can adjust how strong it pulls vacuum as it gets closer and closer to the setpoint. So as opposed to pulling it 100% Every time a valve opens and closes this pump will gradually and more slowly pull your vacuum down incredibly helpful for precise evaporation. Another way might be to use the gradient function. So we can do more of a linear vacuum poll, basically just getting to our parameters a little bit slower.
And then of course, worst case scenario, if we cannot prevent the bumping and foaming, a bump tramp, between the vapor tube and the evaporation flask is a great tool, which will catch that bumping and foaming before it makes it into the collection vessel. If you over bump and overflow, you can still make it through there. That's why we take the preventative kind of methodology first. But if there's a small amount of that occurring, that bump trap will do just great for preventing that bubble over.
All right, great. Thank you. Let's go on to another question here. There's one near the bottom of the list that says what type of flask is suitable for waxes? That's a good question. My personal preference when it comes to waxes is to use a evaporation flask with a removable lid. We have an evaporation cylinder that has a lid that can be popped off the top when the evaporation process is finished. And that's great, because then we can get our hand in there with the scraper and pull those waxes out, as opposed to either heating the flask and holding it upside down. or something of that sort, which could just take forever. So my personal preference, a flask with removable lid is great for waxes.
Okay, great. Thanks. Thanks, Gary, we have one coming during your presentation. So I'm not sure if you'd like to share your slides again, or maybe just respond to this person offline. They're asking if you could please, once again, explained slide number 29. So maybe that's something where you'd like to touch base with them later or unless you want to do share your screen again.
See here. See if we have it. We actually have it up if you want to go to your Yeah, just let me know when you have the slide up and I'll move over to it. Okay. Slide 29 Got it. This one, this one right here. So am I am I sharing my screen? Yes, you are. Okay.
All right. So, yes, so the question, Was there a specific part of the question I can help with or just wanted me to go over this slide again, the person just asked me, you could go over it. Again. I'm going to invite this person if they have a specific question to enter another comment in the q&a box. But in the meantime, maybe just go over it again, if you don't mind. Sure. Sure. So what you're looking at here on the right is the flash chromatography system that generated fractions of purified sample.
On the left is the mass spec, the PCC sticking out is the ASAP probe. And what we're doing here is instead of the traditional method of analyzing a fracture flash fraction, which would be LCMS, that would involve an HPLC system, coupled with mass spectrometry, in order to characterize that fraction, that's a process that is slowed by the chromatography that precedes it. So the analysis can only happen as quickly as the sample coming off the analytical column for LCMS. What we're saying with this is, forget the LC ms, you don't need to do that a flash fraction is sufficiently clean, to just go straight in with a direct analysis probe with no chromatography. And so we touch the probe into the flash fraction, pull it out and go into the entry port in the mass spec, such as you see in that photograph, and you get a mass spectrum directly of that flash fraction without the chromatography and that that you'll be looking at a result in approximately 20 seconds, something like that.
Okay, perfect. Thanks so much, Gary, I'm going to stop sharing your screen for you. And you can go back over to the the big marker screen with all the questions on it. So let's go on to the next question from the audience, which is right under the one we just asked. This one says for dry ice type condensers. Is there any advice to maintain a constant temperature when the dry ice has evaporated out? Well, that's a good question.
Dry Ice condensers can be a bit tough in that regard. Honestly, the best way to keep up that constant temperature is to just make sure that the dry ice is consistently and constantly filled. And then using a mixture such as acetone or ethanol to kind of maintain that temperature. Something else you can attempt is to try using different solvent mixes with that dry ice to achieve a different temperature that might be a little bit more consistent to use. But the easiest will always be dry ice acetone and dry ice ethanol kind of mixture. For our super cold temperatures, you'll pass that your best bet for a constant temperature is going to be to use a circulator or a chiller out
I can maintain a constant temperature in those ranges with enough cooling power to counteract that rotary evaporator.
Okay, great. Thanks. We have another question here that says with your evaporation system, is it possible to evaporate high boiling point solvents like DMV or DMSO?
Excuse me, D MF or DMSO? I'm sorry. That's a good question. Those high boilers can sometimes be type difficult in some types of systems in our rotary evaporators, we can do DMF and DMSO rather easily. The first and most important question comes down to what are your bath limitations, your temperature limitations? Can we run our bath at 70 degrees, or do we want to keep our bath at 40 degrees. If we're running at a 70 degree bath temperature, we might select a vacuum pump that can run it seven to 12 millibar, to reduce that boiling point down to around 40 or 50 degrees Celsius. If we have very temperature sensitive material, we may provide a vacuum pump that can get us down the two millibar that can then take the DMF or the DMSO. With our 150 plus degrees Celsius, boiling points down to a much more manageable 10 to 20 degree boiling point where then we can use a 30 to 40 degree bath temperature to evaporate it without thermal degradation of our product.
Okay, great. Thanks. I think we have time for a few more questions here. This one says, What happens if I get solvent in my vacuum pump.
I can take that one as well. So it depends on what type of vacuum pump you are using. If you're using a huddle type pump that uses PTFE diaphragms, it's incredibly solvent resistant, and there should be no damage to your pump. My recommendation in those cases are at the end of your rotary evaporation process, you disconnect the evaporator line from the vacuum pump and turn that that can pump on by itself for 510 minutes, just let it all dry out, then it should be running just as well as it did you know the day you bought it. If using an oil type pump or something of that sort, you may lose a lot of your performance. And you may have to swap out the oil on the pump in order to get a good vacuum again.
Great, thanks. Here's another question that says how do I clean my evaporator evaporator and my vacuum pump.
So with the evaporator, the easiest way to clean the inside of your glassware is to use either the solvents that you are using with your product and run it by itself. And it'll pull through and pull out everything from the evaporation flask and the condensers because we already know that it's compatible with it. Otherwise, you can run an acetone or an ethanol through the system. And that should pick up everything pretty well as well.
If we want to get into a more thorough cleaning of the system, you know, disassembling the glassware running with soapy water or ethanol or acetone, the heating bath stainless steel, you can clean it using either a citric acid and a warm bath temperature with the rotation on flasks to kind of provide some turbulence or you can pull it out and use a stainless steel cleaner. As for the vacuum pump, running it dry should be enough for that cleaning process. But you really want to make sure there's no residual solvent left in there using something like an ethanol in small amounts to drip through there. Pull everything out and then running it dry for 20 or 30 minutes would also do a good job of picking up any residual solvents that might have made its way into the pump.
Okay, great. Thanks. I think we have a couple more questions before we close our time here today. What size flask should I use for my evaporation, my recommendation there, whatever the size of your vault, whatever that your volume is, say you want to evaporate 300 milliliters or 500 milliliters basically make that 1/3 The size of your flask for a combination of efficient evaporation while also not doing very small volumes at a time. So 300 milliliters for example, great one liter flask, two liters you know kind of the high end of what I would do in a five liter flask
Okay, great. Couple more here. This one says what type of fluid should I put in my chiller.
The most simple fluid you can put in your chiller is a ethylene glycol and water mixture. But I recommend going with your chiller manufacturers fluid as that will have additives in there such as anti algae agents, which will help you increase the longevity of your chiller. You know, if you go with just a pure mono ethylene glycol and water, you might want to replace those that fluid every three to six months. Well if you use manufacturer fluid, it can last a substantially longer time.
Okay, great. Thanks. We have one last question here. This one says for the mass spec part. How do you set up positive and negative modes simultaneously?
Through software basically there is an inversion diode in the system that allows you to change polarities really quickly. So there isn't anything hardware that you need to do It'll basically just do it if you ask it to through a software toggle. It's very, it's a handful of milliseconds to switch between polarities, he goes backwards and forwards very rapidly. So it'll give you a negative ion scan and a positive ion scan from a single injection.
Okay, perfect. Thanks so much. So that does bring us to the end of this webinar. And I just like to remind all of you that this webinar will be available on demand shortly following the slide presentation, please watch your email for a message from lab manager once this video is available. On behalf of lab manager, I'd like to thank Gary Williams and Nate concert for all the hard work they put into this presentation. And I would like to thank all of you for taking time out of your busy schedules to join us today. Once again, thank you to our sponsors add me on intership scientific and heidolph whose support allows us to offer these webinars free of charge to our readers. For more information on all of our upcoming on demand webinars or to learn more about the latest tools and technologies for the laboratory, please visit our website at lab manager.com. We hope you can join us again. Thank you and have a great day.
Thank you. Thank you