Solving Safety and Sustainability Challenges with Ductless Filtration
When a safety crisis triggered by aging lab infrastructure needed immediate action, a leap of faith delivered
Just before Thanksgiving in 2010, a safety incident in an organic chemistry teaching lab at Butler University changed everything. The context is familiar within academia: aging infrastructure formed a growing health and safety concern until it reached a breaking point. They had to accomplish the seemingly impossible—overhaul lab safety with an effective, fast, and affordable solution without disrupting activities.
Gallahue Hall, home to Butler’s chemistry department, is the 1960s Brutalist architectural style common to North American universities. Small, isolated labs were custom designed to suit specific research interests of the day, creating inflexible work spaces with insufficient safety features and design for new research interests and evolving curriculum.
A thriving chemistry program was straining the dated safety equipment by the early 2000s. Teaching labs ran at 90 percent capacity with over 20 student hours per week in each room. The rooms were equipped with two 12-foot-wide fume hoods that had sported the horizontal sash design. After frustrated users removed—and subsequently lost—the sashes, the fume hoods provided ineffective containment, despite moving large volumes of air. Inadequate ventilation spread noxious fumes through the labs during use.
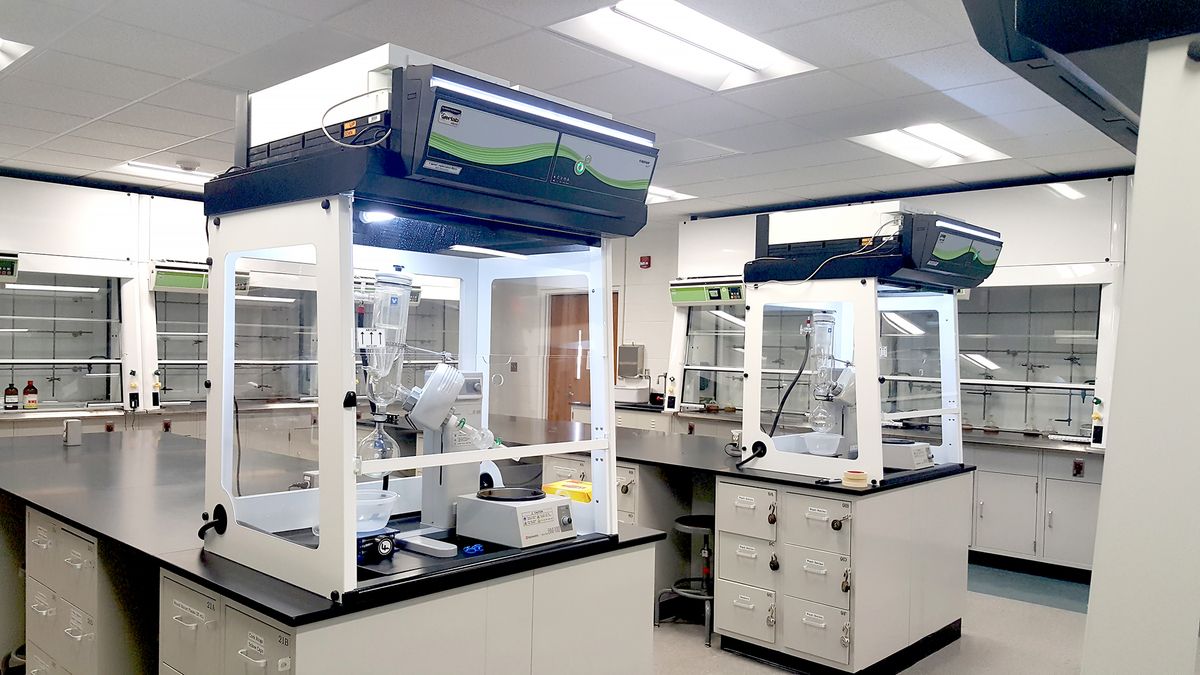
The department followed a green chemistry approach to reduce hazards with the space and resources available. The lab environment was deemed safe enough for students based on expected exposure over the length of their program. Faculty and staff, however, spent three times as many hours in labs for their full tenure and began to experience health complications including asthma, illness, and skin rashes. In 2010, the department began planning for the renovations and additional space required to meet safety and capacity needs.
In late November, a faculty member overseeing students in an organic chemistry lab came to Stacy O’Reilly, PhD, then chair of the Department of Chemistry, for help. She was experiencing a severe allergic reaction and struggling for breath. The faculty member received immediate medical attention, but the damage to her breathing capacity would prove permanent and career changing. In addition to needing daily asthma medication, she experiences immediate breathing complications on entering the organic chemistry labs.
The incident report prompted a swift response. In late December, Stacy was called to a planning meeting. The Board of Trustees charged the university administration and Facilities with improving the lab environment prior to the start of the next academic year, or else shut down the organic chemistry labs. The task: develop a plan to overhaul the teaching labs within eight months on a $2 million budget, without disrupting classes.
The solution had to maintain safe air quality levels, meet current teaching and research needs, and add flexibility. While Stacy pushed for one fume hood per student, they didn’t have the budget for the extensive HVAC rework required nor could they fully gut the space or disable the HVAC system without disrupting labs and research. They also couldn’t increase facility maintenance costs.
Facilities brought in an architect with BSA LifeStructures, Jim Hill, to aid solution design. Jim, having seen the technology at a conference, recommended Green Fume Hood filtration technology to add fume hoods without HVAC alterations. Though reactions were mixed to the unfamiliar technology, it was the most promising solution, and Erlab was brought in to assess the requirements of the space, project, and lab work. Together they designed a safe, effective solution meeting all parameters.
The timeline required a very tight turnaround. The detailed project plan and cost assessment were completed in February and approved in April. The clean-out of the two lab rooms, instrument room, and stock room slated for renovation started over spring break. Classes ran through the summer, requiring creative planning. BSA LifeStructures and Erlab began renovation in May, completing one lab room while the other lab remained in use, swapping spaces in July. All spaces were finished by mid-August.
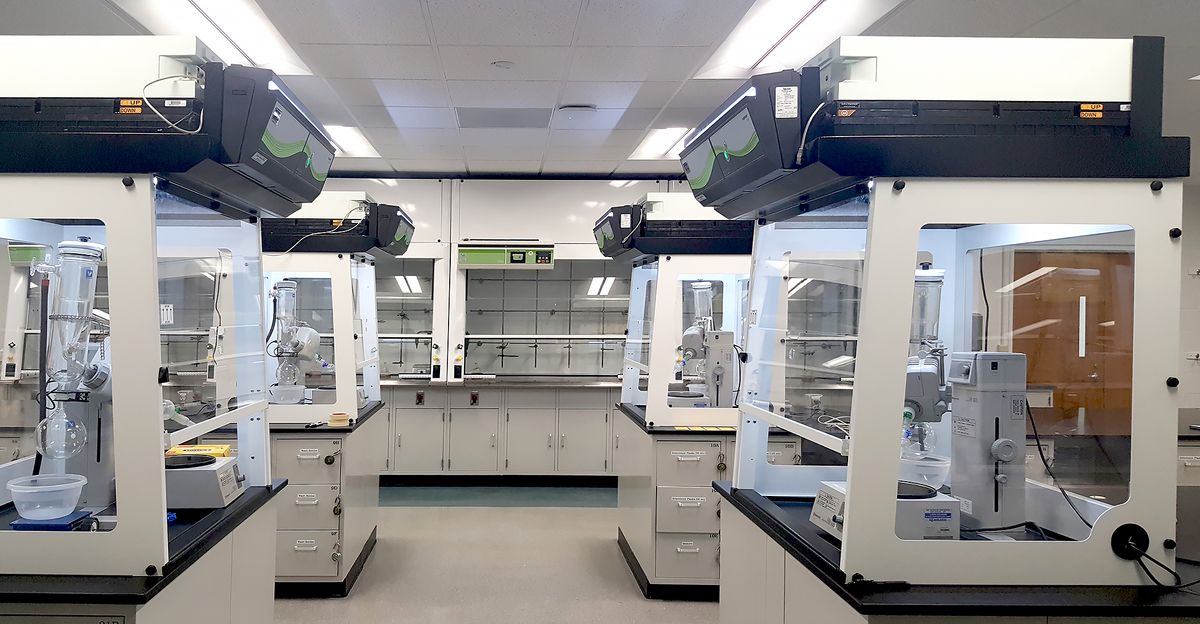
The project was a resounding success, completed on time and under budget. The energy savings from removing the old fume hoods reduced operating costs by $51,000 per year, covering filter and sensor replacement costs. Lab safety and air quality were improved through far greater hood capacity and the filtration, detection, and alert technology, with balanced airflow in the rooms. Faculty began to see improvements to their overall health.
The success of the lab renovations inspired continued improvements to lab spaces over the following years. Filtered hoods were added to the synthetic organic research labs. Captair filtered benchtop fume hoods, portable, clear-walled units that didn’t break line of sight across the lab, were deployed to house rotary evaporators and boost safety in the general chemistry labs. A HALO whole room air filtration system was installed to capture solvent recovery system emissions.
The project became a proof of concept aiding the planning and design for the building expansion and remaining renovations needed, which feature a balance of ducted and filtered hoods. Ducted fume hoods are required for some research applications, so incorporating both styles improved flexibility while reducing energy expenditure in the labs. Since completed, Gallahue Hall now offers a multifunctional, interdisciplinary space that facilitates collaboration, and importantly, has supported continued improvement to faculty health.
Why filtered fume hoods?
The idea of relying on filters to recirculate air rather than venting outside when working with hazardous materials can seem terrifying to those unfamiliar with modern fume hood filtration technology. When initially proposed at Butler, the Environment, Health, and Safety department opposed the use of filtered fume hoods in the organic labs, believing they couldn’t be sufficient for the applications and chemicals used. Installing them marked such a change in conception that Stacy describes it as a leap of faith, though she found approaching the rest of the department with details on the design and why the technology will work helped to get ahead of objections before they formed.
Safety is always the primary focus for fume hoods. Erlab technology follows the strict AFNOR filtration safety standards that dictate performance criteria, and is independently tested to validate chemical retention, filter efficiencies, and enclosures. Every fume hood is assessed for the specific chemical handlings to be performed and issued a certificate of validation with projected filter lifespan. Further, filter performance data is documented for 700 chemicals with list of approved chemicals and retention capacity.
The energy efficiency of filtered fume hoods has also contributed to their popularity. Traditional ducted fume hoods consume the most energy of any common lab equipment, potentially accounting for half of a lab’s energy consumption. This is primarily due to the conditioning of replacement air through the HVAC system. By recycling the already conditioned air, filtered fume hoods massively reduce HVAC load.
Lastly, designing labs with a balance of filtered and vented hoods, as done in the Gallahue expansion project, allows for excellent “future proofing.” Lab spaces are far more adaptable to changing needs and sustainable.
With their improved safety, financial savings, energy savings, and potential for rapid deployment, filtered fume hoods offer an ideal solution for new and old spaces alike. Their greatest impact, however, may be on all the labs contending with aging infrastructure and constrained resources that desperately need improvements in safety and air quality.