Automation Digital Summit Talk: Now On-Demand!
You don’t need to start your automated workflow with printing labels yourself. You have options when it comes to creating an automated system in your lab.
In this webinar, we will explore how options in identifying samples can streamline your lab operations. We will uncover the pitfalls and best practices associated with barcoding implementation and how a barcoding system optimizes sample preparation, enhances throughput, and reduces errors. The importance of assigning each sample a Globally Unique Identifier (GUI) will be emphasized, ensuring complete traceability and data integrity throughout the laboratory workflow.
Key learnings:
- Learn how implementing a quality barcode system prevents errors, mix-ups, and lost samples. Eliminate repetitive manual tasks and free up valuable time for your laboratory staff.
- Gain insights into common pitfalls related to barcoding and learn best practices to ensure successful integration and utilization within your laboratory.
- Uncover how implementing pre-barcoded labware into your automation system can streamline your operations ensuring accurate scans and automated instrument uptime.
- Hear real-world case studies of laboratories that have successfully integrated an automated barcoding system into their processes, resulting in significant gains in productivity and resource optimization.
Join us for this insightful webinar and gain practical insights, best practices, and actionable strategies to increase the productivity of your laboratory.
Speakers:
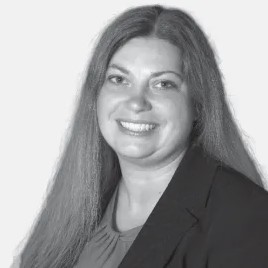
Becky Guza
Technical Services Director
Computype
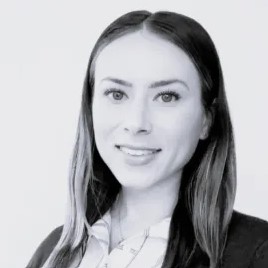
Julia Weisbrod
Technical Sales Manager
Computype
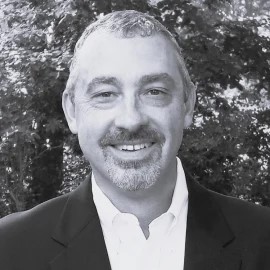
Dave Harris
Vice President Business Development
Computype
This Summit Talk was part of Lab Manager's 2023 Automation Digital Summit.
Laboratory automation systems provide increased precision and standardization and free up time for laboratory staff to perform other work. Automation also offers a virtual option for staff working in other parts of the lab, or working remotely. Lab managers are tasked with selecting the right system for their lab, which can be a daunting prospect. What are the steps you need to take to transition your equipment and staff to a new automated system? What questions should you ask a provider in order to determine if you’re choosing the right system for your facility?
Lab Manager recently hosted industry experts who spoke on these issues and more during its 2023 Automation Digital Summit. Industry experts offered insight and education on how you can choose the right automation system and software for your lab, and what you need to know about the use of robotics in lab automation. Discover the process behind transitioning into a cloud lab system, and what the future holds for lab automation. Watch for free on demand to gain the valuable guidance you need as you evaluate your lab’s automation needs.
Hello everyone and thank you for attending Lab Manager's Automation Digital Summit. My name is Marybeth DiDonna and I'll be moderating this discussion. Welcome to this session, redefining sample preparation for automation. Harnessing the power of bar coding options for streamlined efficiency. You don't need to start your automated workflow or printing labels yourself. You have options when it comes to creating an automated system in your lab. In this webinar, we'll explore how options and identifying samples can streamline your lab operations. We'll uncover the pitfalls and best practices associated with barcoding implementation and how a barcodes a bar coding system optimizes sample preparation, enhances throughput, and reduces errors. The importance of assigning each sample a globally unique identifier will be emphasized ensuring complete traceability and data integrity throughout the laboratory workflow. This webinar will allow you to gain practical insights, best practices, and actionable strategies to increase the productivity of your laboratory. Please send us your questions or comments at any point during this presentation. Our speakers will address these questions during the q and a session following their presentation. To ask a question or leave a comment, simply type your query into the q and a box In the right hand side of your screen, we'll try to address as many questions as possible, but if we run out of time, I'll forward any unanswered questions to our speakers and they may be able to respond to you directly if possible. Additional resources and a certificate for this presentation are located on the right hand side of your screen in the handout section. Please be sure to answer our special poll question at this time for a chance to win a gift card courtesy of Lab Manager. I'd like to remind you the recording of this webinar will be available for free on demand viewing after the conclusion of this event, and I'd like to extend a special thank you to our sponsors who support allows Lab manager to keep these webinars free of charge for our readers. So now I'd like to introduce our speakers for this presentation. Becky Gza PhD is the technical services director at Copy type. The technical services team provides expert support and product recommendations to the sales team and customers. They're subject matter experts in identification and tracking of items in laboratories and manufacturing. Before joining copy type, Becky spent 11 years at HB Fuller, a chemical manufacturing company where she held r d roles of increasing responsibility. Julia Weiss Broad is technical SER sales manager for comp type and has been in the life sciences industry for almost 10 years. She has several years of molecular and cell biology research, both in academic and industry labs. This experie has allowed her to be passionate about accelerating science and given her the perspective to provide support to the science community. Today, Dave Harris is a business development manager, currently leading copy types, LabWare prep services channel partner solutions program. Dave has been with copy type for 30 years helping companies in the life science and industrial space identify and address gaps in their workflow related to both the physical and digital identification of critical assets and work and process identification. Dave has supported hundreds of successful project implementations in the automatic identification and data collection space, solving a, a plethora of challenges that range from identifying the proper marketing technology to survive in harsh environments, barcode labeling, automation, supporting best practices and benefits of the technology choices between barcodes and R F I data outsourcing LabWare identification and sample collection. Kidding. Becky, Julian and Dave, thanks for joining us today. Thank you. Thank you for to all of you for joining us to learn about some important considerations in sample preparation for automation. Our talk will be focused on bar coding options that will ensure identification and tracking through your process. During this webinar, we'll talk about the laboratory automation continuum, the importance of globally unique identifiers, barcodes, and bar coding options, and finish with some examples of people and organizations that have implemented the best practices we are presenting. To get us started, let me take a moment to look at a brief history of getting ourselves and things from point A to point B. Early methods were well pretty manual. The wheel was the big technological achievement and relatively unchanged for a few millennia. Then came the industrial revolution and soon much of the world experienced increased precision and standardization. With travel and logistics, people have more time to perform other work or simply get more work done more quickly. Fast forward to today, cars are practically automated with G P s remote start and even hands-free driving. Let's take a mental leap from transportation and come back to the lab. What does the journey from point A to B look like in the lab? When I was in grad school, we did almost everything in the lab by hand. There were areas that were automated like the auto sampler on the H P L C, but today, automation's becoming more common and includes areas such as storage, liquid handling, and even labeling. As automation continues to increase, some labs are moving towards integrated or orchestrated solutions that bring manual and automated workflows together in a unified way. So you might be wondering why automate Through laboratory automation, the people and organization experience tangible and intangible benefits? Automating processes increases quality and throughput while decreasing cycle time and downtime. Moving to automation also provides an opportunity to update and tweak old workflows and procedures that boost efficiency by eliminating repetition or redistributing staff. Automation results in having unmanned operations and reduces labor by allowing scientists to focus on the science. There's a positive culture and mindset shift among employees, which leads to improved retention and less time and money spent on hiring, onboarding and trading and training. Automation leverages high precision of equipment, thereby reducing errors and computerized and smart machines track data, making it possible to measure product production closely, find and fix problems quickly and adjust to demands in real time. Let's hear from the audience. How are you looking to improve efficiency in your lab? Please select all that apply. We have a few answers coming in. We'll give everybody a couple more seconds to respond. Well thank you to those who responded. We have a good number of people, um, with their responses put in, and it really looks like many of you are looking to organize your laboratory and automate processes. Um, we're really excited, um, for you to be here today. So let's, um, to especially with, uh, those, uh, particular responses in mind. I think you'll find the rest of our presentation to be very helpful, um, in finding ways to do both of those things even better are So given all the benefits of automation, let's take a closer look, um, at things to consider on your laboratory automation journey. So regardless of where you are on the continuum here, the things that are moving in this journey are your samples which are held typically in consumable LabWare. So for your samples to make the journey they need to be uniquely identified, but what does that mean and how do you achieve that? Let's again start, uh, by hearing from all of you, please let us know how you are identifying your things today. Again, select all that apply. We have a couple of answers coming in. A number of people are printing labels and hand applying. We'll wait a few more seconds. All right. Thank you to everyone who responded to the poll. Um, so in addition to, uh, printed labels that are hand applied, there's also a number of you that are hand labeling with sharpies or handwriting labels that are manually applied. Um, so really interesting to see and and typical of what we experience with many of our customers, but to advance in laboratory automation and the journey of, um, that we've talked about in the laboratory automation continuum unique identification that's machine readable is a must. And so as we continue this presentation, we'll review with all of you how you can achieve this. We'll start with unique identification. A global unique identifier is an identifier formatted following special conventions to support uniqueness within an organization and across all organizations that are creating the identifiers. An example of a globally unique identifier that you may have encountered is a donation identification number or d that's used to track blood donations. So labels tracking a documentation of donated blood and blood products is critical to the wellbeing of donors and patients. But prior to the 1970s, blood donations were hand labeled looking something like the picture here. Hand labeling was labor intensive and prone to human errors. Combi type got involved in the mid 1970s to help solve these challenging problems. So in collaboration with various blood collection and testing organizations, we helped create a new standard for blood and blood product identification. Today, din label sets are made so that each blood bag and blood product can be uniquely identified. What looks like a single label is multiple labels that can be moved to identify associated blood and blood products. The pre-printed din goes through a vision-based inspection system at a production facility to ensure no duplicates and guarantee first time scanability. The changes in donor blood identification have improved the track and traceability of the nation's donor blood supply. Your research and the items you're working with are valuable and benefit from being uniquely identified as well. So whether contained within a single lab or shared across multiple labs or multiple organizations, understanding how one will manage the unique identification of items requires thoughtful planning about the scope of where your item might end up and need to be uniquely identified. Here are some important characteristics you need to consider in your organization or environment. So in working with CAPI type, we can help you work through these considerations and help you make the best choices for your organization. The first thing to consider is what does the globally unique identifier represent an assay plate, each individual sample or a container, whatever the globally unique identifier represents, the reference needs to be unambiguous. Another consideration is persistence. A globally unique identifier should be assigned to one and only one item. Reso. A globally unique identifier should be, should, um, be allow you to use the globally, sorry, lemme start that again. So for resolvable, you should be able to use the globally unique identifier to find out more about that item, um, and that item that it's identifying. So you should be able to find test results or data specific to that item. Using that globally unique identifier. Physical placement is another consideration. So will the globally unique identifier be attached to the item? And if so, how? This is an area that Compu type has over 45 years of experience in and that we'll be discussing in the next section of the presentation. Opacity is another consideration. Do you want the globally unique identifier to be opaque, meaning that it contains no apparent, uh, human decipherable information and is constructed as a seemingly meaningless string of characters? Or do you want the globally unique identifier to be transparent, meaning that it contains some sort of human decipherable text? So this could include a prefix that will identify the type or subtype of sample or a suffix that could be used to identify batches or passages of an item. Another very important consideration is creating and minting globally unique identifiers. How will the identifier be created? Who will manage the sequence to ensure no duplicates are produced? Within what scope will your identifier be unique? You'll also need to anticipate the sample collection size and ensure that your globally unique identifiers large enough to accommodate all of your items. One of comp type services is sequence management for its customers. So as you consider opacity and creating and minting globally unique identifiers, the resulting globally unique identifier can be a string of letters, numbers. It can contain prefixes and suffixes. So handwriting a globally unique identifier would be very labor intensive and likely not readable by automation. So barcodes can be used to ensure that that globally unique identifier are machine readable. So Dave will now share some things to consider regarding barcodes and barcoding options. Thank you, Becky. So let's get into the barcode a little bit. Over the next few slides, we'll review barcode fundamentals. And for those of you who are directly involved in tracking system implementations or know a colleague who does have some, we have some helpful tips to consider when planning a traceability project. Troubleshooting a gap within an existing system or just somewhat you want some assurance that you're working smart. At Compu type, we have a very deep bench of technical resources on all aspects of physical and digital identification of assets like samples. Beyond the information you'll learn in this webinar, we're offering up our support to you and your organization should you have needs or questions on how to get started best practices for an existing workflow or a troubleshooting, an existing gap in how you identify and track what's important to you and your organization. So let's dive into the topic of barcodes. The most popular tool used in what's called A I D C, automatic identification and data collection to support unique and accurate identification of your assets like samples. Before we get into the barcode, a little bit of history. The barcode was first invented and patented in 1952. Norman Joseph Woodland and Bernard Silver developed the barcode by mimicking Morris code and extended the concept to thin and thick bars and spaces to create a unique pattern for characters that could be machine read. It was 20 years later before the invention became commercially successful. The first practical application for barcodes was implemented in the sixties by the Association of American Railroads, sponsored by Sylvania, who built a system called Car Track where they would have large linear barcodes mounted on the side of rail cars with a reading device that would automatically read those cars as they went in and out of the rail yard. The first retail application for barcoding was in 1974 when a 10 pack of Wrigley's gum was scanned at a checkout counter at a marsh supermarket in Ohio. Next. So with this graphic, what you're looking at is really the two basic types of code structure. On the top you'll see a linear barcode, uh, that looks like a microwell plate label, and below it you see linear barcodes on a vial below are four different, what's called two dimensional barcodes. Now, all these codes really do the same thing. They're just different advances in technology. The two d b barcodes on the bottom were developed to really compact and get more information into a small space. If you take a look at the barcode on the top, the linear barcode, you'll see that the bars are redundant vertically up and down the code. So when you scan it with a scanner, whether you're scanning the top of the code, the middle of the code, the bottom of the code, you're still gonna be able to interpret the data that's encoded. Now, the chief benefits of using a barcode over handwriting or keyboard entry is I don't have to interpret someone's writing. Is that a nine or is that a seven? You eliminate those kinds of issues with the barcode. The other chief advantage of barcodes is for data entry or data collection. Instead of me hand typing the number or characters off a keyboard and possibly making a mistake with data entry as I scan the code, I'm assured of a hundred percent compliance that the information I scanned is what I'm actually sending into my E R P lim system, electronic lab notebook, spreadsheet or what have you. Uh, the graphic on the right really is a, a a A tip more than anything. Barcodes tend to get printed at the point of use quite frequently, and people are put in a position to print these codes and they're not really trained or or knowledgeable of how to do that. What I wanted to indicate with the graphic on the right is that when you're printing a barcode on a barcode label printer, I can print that code in two orientations, meaning the code comes off the printer in either a ladder configuration or in a picket fence consideration. A very good rule of thumb is whenever possible you want to print that barcode so that it's coming off the printer like a picket fence. The technology of a barcode printer is called thermal transfer imaging, and it has a print head that actually has elements that heat up. If I print the barcode in a ladder configuration, I'm turning that printhead on and off very often, and as a result of doing that, the bars, the spaces will not be as crisp as if I were to print that barcode in a picket fence orientation where I would have the print head on for an extended period of time as it prints the bars and then I turn it off next. This graphic shows you different types of barcode symbologies, and I think the best way to think about barcode symbologies is really like languages where we have English in French, in Spanish. All those languages really do the same thing. They just do it it a little bit differently. Think of barcode symbologies the same way, whether it's a linear barcode or a two dimensional barcode, it's really just a series of white spaces, white, white spaces, black spaces of varying length. Or in the case of a two D barcode, you have pixels that are either dark or white. It's the pattern of these bars or pixels in the way that they're arranged that get interpreted into a number of character or a symbol. The next consideration when it comes to barcoding is to think about the density of the code that I'm going to print. The graphic that you're seeing really is all the same symbology. It's just that the bars and spaces are printed at different densities. Uh, the bottom code is a two mill density narrow bar up to the top code, which is a 70 mil narrow bar. Now, all of these codes are identical from the standpoint they're the same symbology. I am encoding 11 data characters, but I'm just doing it with a different density. This is a consideration. You want to think about when you're considering your application. Do I, do I have to put a label on a small two mil cryo vial or am I labeling a warehouse location that I need to scan from a long distance? Those are considerations you want to think about when you're printing or or procuring barcodes. The other aspect of barcode density and barcode symbology that you want to keep in mind is what is my infrastructure? What are the scanning devices that I have on the workbench or in some automation where the sample may be presented, it's important that the scanner is matched up to the barcode symbology as well as looked at from the standpoint of the density of the barcode. So for example, I could have a scanner that is set to read a 10 mil narrow bar, but if I were to print a code with a smaller narrow bar, I might not be able to read that code. Other considerations you might want to think about when picking a barcode in biology and a barcode density is, do I want to use a a linear barcode like we saw earlier in what you see on the chart? Or might you want to use a two dimensional barcode to get more information into a smaller space? Not all scanners are built the same. Not all scanners are rated to read both linear and two dimensional barcodes. So what I'm saying here, it's an important consideration to take a look at your infrastructure, take a look at your automation, take a look at what you're labeling and how small the code will need to be to fit all those kind of go into the mix of what's the best way to to approach it. Other considerations when picking barcode technology and the materials that you choose to use are the environmental considerations of your application. In life sciences, this can be a very challenging task. Some of the things that we look at and evaluate prior to making a recommendation could be is the code, uh, the label on the piece of lab work gonna be exposed to say chemical exposure? Um, there's a real interesting application we were involved in some years ago with a diagnostics company that made automated slide slide staining equipment for a histology application. They were going to automatically prepare and stain a slide. They obviously needed to identify that slide and they wanted to do it with a barcode. The challenge for us was really twofold. They needed the label to have some functional characteristics because as they were staining the slide, they were exposing that slide to chemicals and the physical label needed to have some damning effects to keep those chemicals on the tissue and not run off the slide. The other challenge for this particular application was that when in a histology application, you use xylene, which is a very caustic chemical, which can eat away at the carbon. So we had to come up with a chemically resistant combination of materials and ribbon. Other considerations as far as environment are, are the temperature? Are we going to see extreme heat or extreme cold like cryogenic storage or exposure to dry ice? Abrasion is another area that we wanna look into. Is the code gonna be physically attacked by some kind of an abrasive material, thus requiring it to be over laminated or protected in some way, shape or form? Another important consideration is what I'm actually putting the label on. There are different kinds of lab wear, if that's what we're talking about in this example, you can have polypropylene, polystyrene, polyester. All types of various plastics label materials are built to adhere to certain kinds of substrates. So if I'm going to be labeling a polypropylene tube, for example, I might use a different adhesive than if I were to label a glass vial, say, for a compound library application. Another consideration is storage and handling. In a lot of automation, you will see racks that hold vials or tubes. Sometimes these racks can be very tight that the tolerance between the circumference of the tube and the rack itself doesn't allow for for much additional space. If you put a label on a tube that goes into a tight rack, you have to pay special consideration to the materials you use to ensure that label will not wing off and get hung up in the automation. Or if the material's too thick, it creates an outer diameter that's too tight for the storage, uh, of those tubes, and that can be problematic at all. All these factors should go in the decision making process about which imaging technology, which materials is best to get your lab were identified properly. Next, I'd like to just spend a little time talking about R F I D. The session that we're highlighting today is really based on barcode because that's the majority of the applications that people are using, but R F I D, which I would consider a new form or the the most latest technology in automatic identification and data collection. So what is R F I D? Let's just go through some of the basics. R F I D stands for radio frequency Identification. A form of R F I D was first considered used during World War II by the us, British and German militaries to identify friend or foe. So the technology, the idea of the technology has actually been around quite a long time. The first true ancestor of the modern R F I D device we know today, which is a passive radio transponder with built-in memory, was first invented in 1973 and then further developed and officially patented in 1983 when the term R F I D was first used. We don't have near enough time to get into the topic in great depth because there's a lot to understand and realize before you make that jump into this technology. But let's cover a few basics of R F I D. As I stated earlier, R F I D stands for Radio Frequency Identification. It is used to identify items just like a barcode. One of the chief advantages to R F I D is that I don't physically have to see it to scan it or in some cases to actually write to it with a barcode, I have to physically see that code, hit it with the scanner's beam of light to interpret the data and input it into my system. With R F I D, I only need to be close, which in some cases is a big advantage. In other cases, it's a detriment. The R F I D is in a tag form. It is usually applied to a label, and then that label with the tag with the R F I D tag is applied to your microwell plate, your tube, your vial, your reagent or what have you. Um, the devices that read and write to R F I D are different than barcode, so that's another consideration you have to have. If I have an infrastructure that's set up to read barcodes and I decide I want to implement R F I D, that infrastructure needs to be changed out. So you really need to take a step back and take a look at what you have. And if you were to go to R F I D, what the ramifications of putting that infrastructure into my workflow would, would look like. The technology used to transfer the information, unlike the beam of light that is used with a barcode, are radio waves. Uh, the information is transmitted and received through a radio wave form of communication. There are many types of technology exists for R F I D and you really have to take a hard look at your user case application. You have to look at your budget, you have to look at the environment the tag will be used in and subjected to, as I said earlier, you really have to take a hard look at the infrastructure that you have in place for reading or writing the tags or if there is no infrastructure in place, what it will cost to build that out. Those are all some basic considerations that you have to put into the mix. When considering R F I D. Uh, another couple of things on R F I D is that the tag will hold what information you program to it. It could be a serial number, uh, it could be other data like a lot code, a date code, perhaps some, some some form of, uh, detail related to the product itself. Tags can come in in a couple of different forms, meaning I can have a tag that I can only read, so it's perhaps a serial number and it's used like a barcode as a serial number, but I can only read the information. I can't do anything else with it. There's other technologies within R F I D where not only can I read what's on the tag, but I can write information to it, and that is a great benefit for many applications. When you stop and think about it, if I had something that had a serial number assigned to it, but then I was doing work to this sample and I wanted to keep track of what work was being done by who, when I do have the possibility to write that information to the tag, um, to really create a, a database of information on that particular item for some applications, that's a really great feature. Another interesting aspect of R F I D that comes into play for some people is the fact that that data can be encrypted. So it is a much more secure form of identification and tracking as compared to the barcode. A couple more things to think about and consider when you're looking at barcodes verse R F I D, because there's benefits and limitations to everything. Uh, the cost to implement typically R F I D is gonna cost more than a barcoding system, but the benefits may far outweigh that additional cost. Another chief attribute of R F I D that I spoke about earlier was the pack with R F I D. I don't need to see it to scan it with a barcode, I need line of sight. So perhaps for an inventory control application where I want to do a quick inventory of a shelf with R F I D, I can wave a scanner over that shelf and I've collected data on all the items that have an R F I D tag on them. If that was a barcode application, I would physically have to see every barcode on every item and scan it to do that inventory. To give you some idea of the benefits of line of sight or I'm sorry, the benefits of proximity scanning versus line of sight scanning. Some other considerations to taking mine are the size of the product that I'm identifying, the environment that that product is gonna live in and needs to be scanned through. Uh, for example, micro vials pose a quite a big challenge for R F I D. There's new technologies along the lines of R F I D called MEMS technology that will allow you to identify with an R F I D like technology, a small micro vial. There are many advantages to that, especially when they're stored in cryogenic freezers and you have frost buildup over the barcode that can make barcode scanning extremely difficult and hard to do with an R F I D tag. Again, I only need to be close to that item, but realize you will pay for that benefit. Again, R F I D requires its own scanning and reading infrastructure, uh, for data reading and writing devices. And when it comes to R F I D, there's a plethora of technology options. Read only read and write size of the memory, the frequency of which the radio waves are transmitted, which could come into play if the item is shielded by metal or if the item that is marked is shielded by a liquid. Some frequencies work better through liquids than other frequencies. All these are considerations you have to take into account when considering a barcode as a solution versus R F I D. I will mention real quick for anyone that's interested, we have some really good literature on evaluating barcodes versus R F I D. We also have some very strong literature on barcode, symbologies and barcode densities. If anyone in the audience would be interested in receiving that, just leave of a, uh, leave a message for us in the q and a section or reach out to us some other way and we'll be happy to get that to you. So now that we've touched on some barcode basics and introduced R F I D as a means of traceability, let's discuss a few options related to how do we get our assets or samples properly identified. The good news is that if you're currently handwriting labels or printing labels on a sheet off a laser printer, there are better ways to do it. Also, if you're currently printing labels off a printer and hand applying those to support your automation and tracking needs, you can improve on the efficiency of your way of work to streamline and improve the process by utilizing better tools and making sure that the tools you're currently using are used properly. Let's get into that discussion for a bit. So if you take a step back and you realize that I wanna start barcoding my assets, my samples, there's really four ways you can go about the task of getting your products or LabWare identified. Um, I can decide I'm gonna get in the label printing business and procure blank labels or maybe partially pre-printed labels with my logo on 'em, get a label printer and get in the business of on-demand label printing and applying those printed labels. Uh, another way to look at it is, you know what? I'm gonna outsource the work of printing and I'm gonna procure pre-printed barcode labels from a supplier. Another option, if you do decide you have to print on demand or you have real-time data concerns that require you to print on demand, uh, you don't necessarily have to do it by hand. There's been a lot of advancements in automation and these label printers are now offering features that not only print the label but automatically apply the label, and then there's fully automated systems that will take care of all the steps required to print and apply a label onto your product or LabWare. The last consideration we'll talk about is something that's really growing in the marketplace and that is outsourcing that work and procuring pre-marked or pre barcoded LabWare. So the first category that I want to talk about a little bit, which is probably the most used out in the marketplace, certainly in the life science space, are blank labels with on-demand label printing systems, the barcode label printer. Not all barcode label printers are the same. Usually when you see barcode label printers in use, they're not really taking advantage of some of the features and benefits that those printers have to offer. And that's what I want to touch on a little bit. Not all label printers are the same, nor are all label printers set up properly to match your workflow requirements. Printer options, you can secure a label printer pretty inexpensively, but the question you need to be asking yourself is, is it gonna be set up to work in an efficient as possible way? Taking in consideration my operators and my workflow requirements, it's important that when you're doing this, you're thinking about all the inputs to the application. So for example, the importance of matching the materials to the application. Typically, there are two consumables that run through the label printer. There's the label stock itself, and then there's a ribbon. And what the printer is doing is transferring the ink off the ribbon onto the label substrate. There are heat settings involved in this. There are other printer settings involved in this, and it's not uncommon to see somebody printing labels where the heat setting isn't proper so the print looks faded or the heat setting is set too high and the print looks a little bit blurry, or I have this great polyester label stock with a great adhesive, but I've selected a wax ribbon. So if there's any abrasion, uh, that that wax will come right off, it's really important to understand and consider that all these inputs work in concert, the label stock, the ribbon, the printer, and the way the printer is set up. There's also a lot of other features and benefits that come with thermal transfer printers that people don't realize they could be utilizing to streamline their workflow. So for example, some label printers can work in a dispense mode where they will print the label and dispense the label on the liner. Other settings could print the label, dispense the label, but rewind the liner, thus turning the label printer into a dispenser, making it much easier for your operators to grab the label and get it applied to the LabWare. Increasing your time to actually do that task significantly. Other questions you might want to be thinking or asking yourself, do I need a cutter? Do I want to put a verifier on the printer so that if I'm printing barcodes, I can be assured that the barcode that I printed is of a high quality standard and will work in our ecosystem? Is the printer and print head heat settings set for optimal use with the ribbon and label stock that I'm using? Well, the image I'm printing survive the environment. Can the blank label be enhanced to support my workflow? And I'll talk about the label on the graphic in just a second. If I'm Ali quoting a sample, can the printer be set up with a scanner so that I could scan an existing sample, create a duplicate barcode, perhaps with a prefix or suffix to indicate this is a child sample to the parent and again, streamline my workflow to make the time to get the labeling task done as efficiently and quickly as possible. Another important to consider, another important consideration when on-demand label printing is the label stock that you use. There's functionality that can be built into labels that many people don't think about. They're just trying to get the barcode on it and get that label on a tube. The label that you see with the four color bars on the graphic really has a lot of functionality built into it. It's a polypropylene label that'll stick very well to a tube or vial, survive in a cryogenic storage condition and not wing. What you're seeing on that particular label are a couple of enhancements. Number one, it's a white label. That grayish area is actually a, a clear film so that the label's designed to wrap around over wrap the circumference of the tuber vial and ensure it stays adhered to your tube in minus 1 96, um, cryo conditions. The four color blocks are there as a way to incorporate or introduce color coding into your workflow. The way this particular application was set up, the operator had one of four tubes they were using. Each of the tubes had a different color stopper, red, blue, yellow, and green. So when I print this label, I actually overprint three of the colors I don't want to use and leave the one color I do happen to use or want to use for this particular vial, and thus I end up with a red color code, a blue color code, and so on and so forth. Onto the next slide. Thank you. The second option you need to consider when barcoding, um, is the outsourcing option. Do I want to have somebody else pre-print these barcodes for me? Um, you can certainly do it yourself. There are applications where you're more or less forced to do it yourself. I think what a lot of people don't understand is there are service bureaus, there are companies like copy type that can preprint the barcodes for you. The advantage to something like this is we will track the sequences, we will visually inspect the barcodes. Oftentimes we can introduce additional functionality to the label sets like we do for the transfusion medicine application Becky talked about earlier. So realize that. Um, another option that you have available to you is to have somebody print the barcodes for you. The next option I want to talk about is automation. So I'm printing these labels on demand. I have to, I'm applying these labels, my volume goes up. Business is great, we're getting a lot of samples. Well, I really don't want to do this by hand. There are a lot of automation options that aren't to the scale of packaging that can really streamline your workflow. Here's an example of a label printer from Germany called cab. These are two different printers, but each of them has an applicator built into it. So not only am I printing the label, I'm printing and applying it to a tube or vial, thus streamlining my process. And the last slide I wanted to talk about was just outsourcing the work completely. There are more and more people going in this direction. You are seeing more OEMs offer pre-marked LabWare. Um, so one thing you can think about is, should I just procure pre-marked or pre barcoded LabWare? As I mentioned, you see a lot more skews by the LabWare OEMs offer this up. Uh, companies like comp type do this on a custom basis. So not only can you get your LabWare prepared in advance for you with a barcode, but we can do things like add graduated line scales, color coding, branding, fill lines. It's, it's really unlimited. So a lot to think about when you're implementing barcodes at this point in the presentation, 'cause I'm going too long, sorry Julia. Um, my colleague Julia, uh, uh, someone who has found herself on the bench for a long time is gonna talk quickly about some use case applications. Thank you Dave. So this does bring us to our implementation and success stories and we're gonna go through three different, um, scenarios that we've worked through and partnered with some organizations on. So to start with, we're gonna speak to a global diagnostics organization that we worked with. Um, they had purchased and invested in automated equipment that would be for high throughput samples, specifically for infectious disease that is for blood-based, um, tests because it's blood-based, it was extremely important for them to be accurate with their barcoding and they essentially wanted to leverage their already purchased automated equipment as best as they could. When they partnered with Comfy Type, we were able to provide accurate barcoding and custom markings. Um, the placement was accurate because of our history and transfusion medicine that allowed us to leverage our existing vision system verification technology to image and manage the barcode sequences without duplication, which was essential. Um, as I mentioned, because they were blood-based patient samples, um, um, they overall they were successful at using their automated equipment that they had invested in, um, when they were using their best practices in place for barcoding with the partnership that they had managed with comp type. Um, so another successful example of how we can apply barcoding to, um, some organizations in real life invention scenarios would be at a biopharmaceutical organization. Um, a large pharmaceutical organization had a short deadline for a global clinical trial. Um, it was essential for them to get these specific two milliliter tubes for patient collection samples. Um, once they were able to partner with comp type, um, we were able to leverage our existing, um, supplier relationships to source them without facing some of the supply chain concerns that maybe some others had been facing at the time. Um, and then we were able to mark them for them for their automation. Um, specifically they needed, uh, in addition to just the two D code, they needed customer information and a custom logo. Um, so we were able to provide them with those colors and the custom image as well. In total, we provided 85,000 barcoded vials and they were shipped from our manufacturing facility in Minnesota over to the east coast and where they then distributed to their global clinical trial. Um, with this successful partnership with compute type, we were able to provide a quick turnaround for their custom marked and barcoded LabWare and they were successful in, in, in, um, completing their global clinical trial. Uh, so this will bring us to our final example, which is a central accessioning in reference lab. Um, so we partnered with a central lab that would receive patient samples from nationwide clinics. Um, so each clinic may have a different collection vial for each sample. Um, sometimes they had different labels from each clinic site. Um, so they partnered with comp type in order to provide one consistent vial that's pre-marked and could be provided to those clinics. Um, so once the lab received them, then it would fit more efficiently with their lab workflow. Um, I know those of us who have worked at the bench could probably appreciate that anything to make the actual lab workflow more efficient once you get the sample that you need is extremely helpful. Um, so these vials were then, um, shipped nationwide and they were successful to get to each clinical location and then they could ship them back to the lab to do processing. Part of their processing did include some ALI quoting. So in addition to the pre barcoded vials, we were able to provide them with a print and scan station to allow them to print that child sample label to go with the parent that had been aliquot from. Um, so that allowed patient samples from different locations to be easily identified and tracked, uh, nationwide, and then come back to that central lab and, and go through some pretty efficient processing once it got to the lab. Um, so this kind of brings us to a little recap. Um, so we've covered some of the challenges that we faced industry-wide, um, and we also covered some solutions. So there are solutions to identify and track critical assets in your critical samples throughout the lab. Um, we discussed some of the solutions. It could be gys and bar coding options. Um, we discussed some of the compute type services. That could be an option that would be helpful. Specifically LabWare procurement like I just spoke to in LabWare marketing, sequence management and even packaging and distribution like we did in some of those success stories. Overall, we're just here to help increase efficiency and help your lab workflow. Um, so this is gonna bring us just I think in time for some questions at the end. Um, I'm gonna start with the first question though, and that is, who is comp type? Um, we are a, an identification and tracking services company that supports the science community to gain insights into the chain of custody in the workflow in their lab. Thank you. Okay, great. Thanks very much to Becky, Julie, and Dave for a wonderful presentation. At this point, we are gonna move into the q and a session with our audience. We have about 10 minutes left. Uh, a reminder if you join us late, you can send me your questions or comments by typing into the q and a box on the right hand side of your screen. Even if you don't have a question, if you'd like to leave a comment for us to pass along to the COMPI type team, please, uh, just leave it in i q and A. If you want them to reach out to you and provide more information, we will have your contact info. So just leave a comment there. Uh, one more quick reminder, please visit the handout section on the right hand side of your screen for supporting information for this event. There's also a certificate of completion for this webinar if you need that. And I would like to remind you again, um, visit the polls section. We have a couple polls, uh, from the copy type team here, and we also have a poll from lab manager where if you submit an answer, you can be entered for a chance to win a gift card. Um, so Becky, Julie and Dave, thanks again. Let's jump into the questions. Uh, we have another question up at the top from the audience. Can you gimme some insight into how barcoding and LIMS work together for data management? I'll, I'll take this one. So, um, like we talked about, barcoding is really automatic identification and data collection. It's a way to uniquely identify an asset and conversely get that information into a limb system, into a spreadsheet, into an electronic lab notebook. So they really do work in concert, um, and it's, it's just an enabling data collection tool for a limb system. Okay, great. Thanks Steve. Um, if you scroll down a bit, we have another question from the audience here. How can we ensure 100% instrument reading in my tecan? We have regular issues with reading barcodes and then downtime occurs. I'll take this one on too. I, I, I think it really, um, you, you have to take a look at the root cause of, of what's going on. Um, printing barcodes properly is, is probably the most important aspect to consider. Am I using the right materials? Is the printer set up properly or is the company that's providing these pre-printed barcodes set up properly to match with the scanning devices that I'm using? Uh, but if you kind of check all those boxes and you understand the infrastructure that you're working within, once you get it set correctly, typically you don't see problems. It's, it's when somebody picks the wrong label material or they're printing a code that's too dense for the scanners that are, that are being used to read the code. So, um, kind of an open-ended question that can go a lot of different directions, but as we talked about, um, there are certain, um, certainly there's, there's things that you can do to assure that you won't have these kinds of problems. Okay, wonderful, thanks. Uh, underneath that one we have another question. This one says, can label printing work for field work labeling or only in the lab? What I mean is decision of field label style can change in situ. Um, yeah, I mean we, we get involved in many applications that are lab-based, but they're oftentimes field-based as well. Um, there's been a lot of advancements in the technology. So for example, if I'm identifying a container in the field that's gonna be used to collect a sample that's gonna go back to a central laboratory, there's a lot of ways to skin that cat. You can, um, start with a tube that's pre-labeled problem solved. Uh, there are portable devices. There's portable printing devices that can be used in the field that work off battery power, that could allow you to print a code at the point of collection and uniquely and properly identify that sample, uh, to be later received and scanned and perhaps processed and allocated into the lab. So yeah, these things can be done, uh, on a bench top within a lab, but they can be done out in the field too with either a, a pre-marked tube or a portable device that allows you to print labels out in the field. All right, great. Thanks. Uh, I think we have about five minutes left for a few more questions. This one says, are there any options for laser marked LabWare? Yeah, um, that's another imaging technology. Uh, typically laser marking is not done at the point of use because of the cost of the equipment. So typically laser marking is used when you do pre-marked lab wear. Um, what you have is, uh, a tube typically with a label or white patch applied to it. And what the laser does is it hits that white patch and actually change the color from white to black, thus creating the lines used in the barcode. Uh, another technology used for laser is that it a blades the material, um, thus removing it and exposing a different colored layer of material. So laser marking can absolutely be done. Um, it can be done on a label, it can also be done directly marked on the container. Uh, but it's just one of many different imaging technologies that you could consider, uh, when you understand the full scope of what you're trying to accomplish. All right, great. Thanks. Uh, we have a few more questions. We'll see how many we can get through in the time allotted. This one says, how much does it cost to automate the process of printing and applying labels? Um, kind of an open-ended question again because, um, you can start with semi-automatic automation. I showed a couple of, uh, cab branded printers, uh, that are made to both print and apply labels to tubes and vials. That type of system you can get, uh, started for less than $10,000. Now, a fully automated custom system and we've been involved in projects like that, um, they could, they, they could range well over a hundred thousand dollars depending on how large it is, how much material handling I'm implementing, if I'm gonna have a vibrator bowl, a conveyor system, a print and apply system verification, additional material handling to take that just mark tube and perhaps put it in a rack. Um, so it's, it's, I'm not trying to avoid the question, but there's a big range you can get started relatively inexpensively and then it really kind of goes from there. All right, great. Thanks. Uh, looking at the clock, I think we have time for one more question. Uh, this one says our lab is currently hand labeling, but now we are processing many more samples. What would you suggest we do? Am I gonna take the last one too? I think I am. I love to talk. I I would say you should, you should call us is what you should do. Um, actually, um, this is pretty common. Typically, applications start out low, start out small, they get bigger, they ramp up. That's why we talked about the options. You know, it might make a lot of sense for you to print and hand apply labels to get started. As volumes increase, you really don't want to be paying expensive labor to be labeling tubes. Nobody likes to do it. Nobody likes label parties. So that's when you start to look at either automation or you think about outsourcing it. You know, you're not really in the business of printing and applying labels. You're in the business of science. Let somebody else do the label printing and applying for you. So when we were on that slide with the four different, um, options of how to get there, I would say you, you take a deep dive into each of those four boxes and you pick the, the right path for you. All right, wonderful. Thanks so much. So we are at time. That does bring us to the end of this webinar. So on behalf of Lab Manager, I'd like to thank Becky Gza. Julia Weis Broad, and Dave Harris for all of the hard work they put into this presentation. And I'd like to thank all of you for taking time outta your busy schedules to join us. A reminder that all of the presentations from the Automation Digital Summit will be available for free on demand viewing. So please watch your email for a message from Lab Manager once these videos become available. Once again, thank you to our sponsors, copy type, Integra Brand Tech, scientific Metro U S A analytic Jenna and Automata. Their support allows Lab Manager to keep these events free of charge for our readers. Please be sure to tune in for our next presentation at 12:30 PM Eastern today fully automated n g s sample preparation using a digital micro microfluidics platform. For more information on all of our upcoming or on demand webinars, or to learn more about the latest tools and technologies for the laboratory, please visit our website www.labmanager.com. Thank you all for being part of our Automation Digital Summit, and we hope you have a great day. Thank you.