How to Ensure a Positive Relationship Between Lab and Design Teams
Collaboration and technology improve the design process to achieve successful new lab buildings and renovations
Embarking on the design of a new lab building or lab renovation can be both thrilling and overwhelming. The excitement to build a new state-of-the-art lab or refurbish an existing one is quickly met with the realization that resources are finite. To deliver a project on time, on budget, and within the available space, all stakeholders will need to make compromises throughout the design process. Compromise itself is not a bad thing, as long as it is always being made in alignment with a shared vision: to ensure a successful project. The below strategies help create an environment where collaboration, communication, and compromise all work to ensure the best possible outcome for a project:
Hire a qualified team
For a smooth design and construction process, begin with an experienced, well-rounded team. When selecting a design team, choose architects and engineers based on their collective expertise in the proposed lab typology. Contractors with experience constructing high-quality laboratories should be considered as well. In addition to the core design team, specialty consultants providing guidance in commissioning, qualification, and validation may be required if the lab needs to meet FDA regulations and requirements.
Establish a culture of collaboration, shared vision
Establishing a collaborative culture is key to delivering a new lab building successfully. It’s also critical in lab renovations where existing conditions must be considered. To do so requires engagement with the lab manager, scientific end users, and leadership throughout the process, along with fluid communication between the design team and the contractor. Each person on the project team approaches a new lab design with their own objectives and priorities. At the beginning of a lab design project, a recommended first step is to host a visioning session with the key stakeholders to identify the project’s goals, priorities, and constraints. By setting the stage with an open dialogue, everyone has a chance to voice their thoughts and come to an agreement on the most critical project factors.
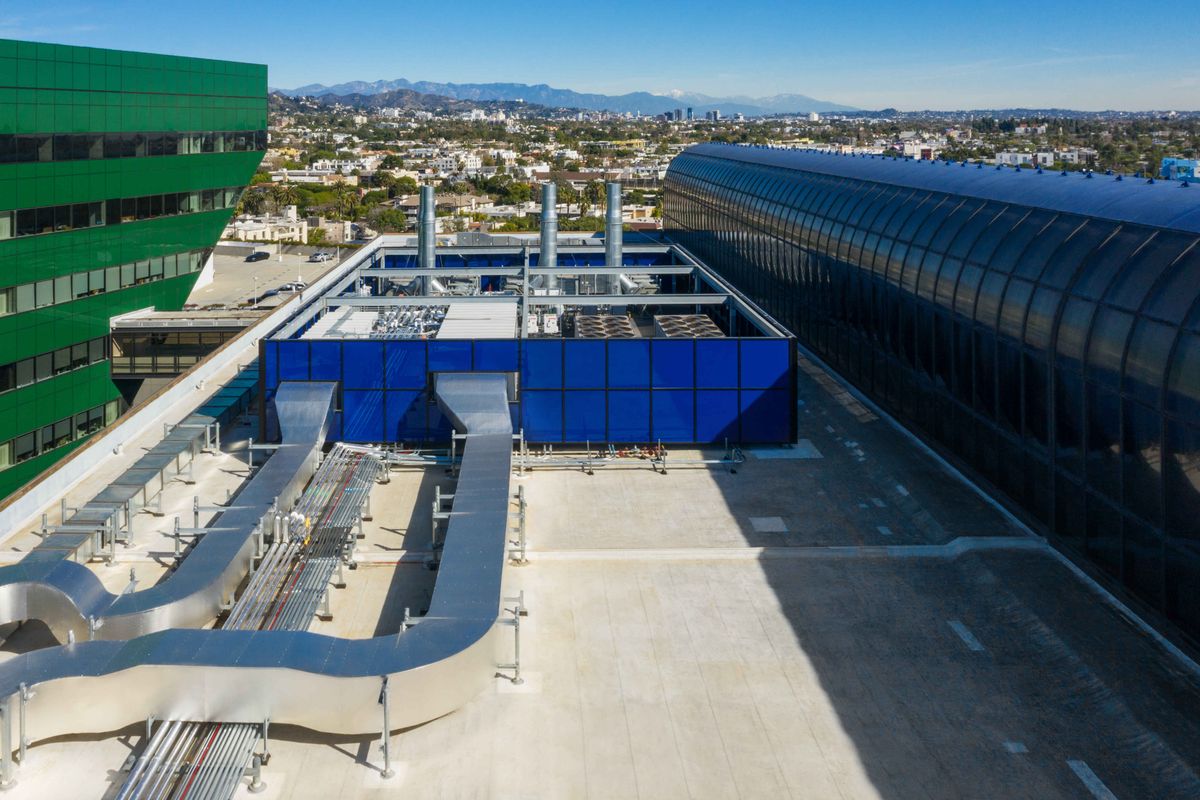
These discussions lead to a better understanding of each individual’s needs and wants, and how they can be accommodated. It offers stakeholders the opportunity to work together to develop strategies and compromises that will benefit the project holistically. Once consensus is built, all parties are invested in the shared vision to advance the project forward.
Identify space-saving strategies before any design work begins
As unpredictable market conditions are known to influence construction and operational costs, space utilization and energy-saving measures are vital to meeting project requirements. During the programming phase, identifying ways to share equipment, storage space, workshops, and server rooms can save program square footage and increase efficiency. A good understanding of the answers to the following questions can help teams make sure they’ve identified the best opportunities for the most successful, efficient, and productive space utilization. It assures those who feel compromises were made that they were done in the best interest of the project.
What can be shared?
For example, having biosafety cabinets and fume hoods that can be shared by multiple departments can not only save space, but also reduce the upfront mechanical and electrical infrastructure costs and operational costs. A shared workshop supporting multiple labs eliminates the need for expensive, redundant equipment that may not be fully utilized if located in separate labs.
The concept of having shared spaces within labs can be met with skepticism. However, highlighting that shared space can bring substantial cost benefits may offset initial objections.
How do users prefer to work?
To understand the needs and functions of scientist and lab technician workspaces, quality time should be spent in the programming phase to plan the workplaces efficiently. For instance, some data input may need to be done in the lab at an instrument workstation. However, others may prefer entering data outside of the lab.
Enclosing labs with glass and placing workstations adjacent to the laboratory allows staff to monitor processes in the lab while providing a quiet environment for heads-down work. Rethinking the typical workstation arrangement can save space and create a better environment for productivity.
How is productive collaboration best supported?
Another effective space-saving design trend is to expand high foot-traffic areas to encourage impromptu, casual conversations and collaborations. Flexible, multi-purpose spaces incorporating shelving and storage can be reconfigured to double as break space or meeting space, while also functioning as the lab library when not occupied.
How much flexibility will be required over time?
New lab buildings and lab renovations must be planned for long-term flexibility to accommodate new workflows, processes, compliance regulations, and technology. Designing and installing mechanical and piping infrastructure that can easily be reconfigured will allow for such flexibility. Providing growth lab space with the appropriate support infrastructure can allow today’s conference room or storage rooms to be converted into lab space in the future. During the design phase, the project team’s strategy should prioritize how to best accommodate future growth to ensure infrastructure is properly sized.
Use technology to build consensus and reduce changes in construction
While architects and engineers still produce drawings, most design work is now developed in 3D modeling software. Today, lab designers leverage the most current building information modeling (BIM) and virtual reality (VR) technologies.
BIM technology assists architects and designers with coordinating mechanical, plumbing, electrical, lab piping, and fire protection with the building structure in much more detail. For example, it can be used to verify clearances and coordinate placement so infrastructure can be easily maintained. BIM technologies also equip designers with the ability to produce high quality renderings, quickly. These are meant to reflect an accurate vision of the proposed spaces, which better inform the client and help speed up the approval process for design, materials, and products.
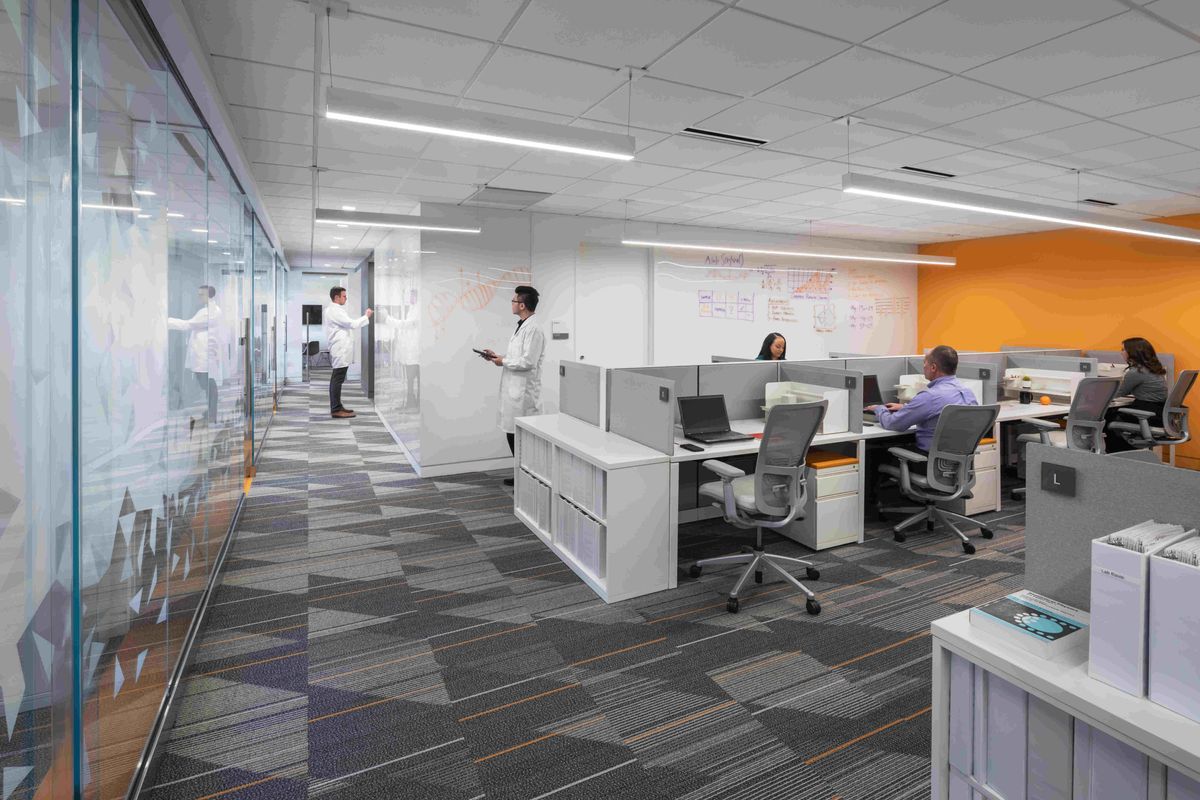
The use of BIM was critical in the Cedars-Sinai Biomanufacturing Center that was developed in the existing Pacific Design Center in West Hollywood, CA. This 23,000-square-foot lab was located on the second floor of a six-story building with low floor-to-floor heights. BIM was used to create snaking pathways through existing fan rooms for mechanical ducting and piping to reach the rooftop’s central plant that served the labs.
Given the low floor-to-floor heights and desire to maximize ceiling heights, all the infrastructure was strategically placed within the model to avoid crossing ducts and align conduits and sprinkler piping in corridors flanking the labs. The BIM model was then shared with the selected contractor to expedite the development of shop drawings and provide easier coordination in the field.
In addition to BIM, utilizing VR technology allows clients to “walk” through their building’s design to see how it will feel to experience the physical space while in the design phase. Scheduling VR sessions for the project team, including the contractor, shares the design intent and project vision. It is a tool that can be used to communicate, collaborate, and build consensus.
With the Cedars-Sinai Biomanufacturing Center project, VR sessions were scheduled with the lab manager and lead scientists, offering them the opportunity to inspect equipment locations and clearances, adjacencies with lab support areas, and other lab details. Adjustments were made in real-time to enlarge rooms, shift equipment and doors for better clearances, and enhance process flow before construction started. The ability to harness the latest VR technology prevented potential costly and time-consuming changes during construction, while also creating a great sense of excitement for the project becoming a reality.
As efficiency and flexibility continue to be top priorities in lab design strategy, the latest technology and collaboration tools ensure compromises between stakeholders are communicated, understood, and delivered in the design and construction process.