Before scaling up synthetic production, optimizing reaction conditions is critical
Flow chemistry requires only small amounts of material, can achieve reaction conditions that aren’t possible with batch reactions, and offers greater control and reproducibility of reactions. The FlowSyn Maxi™ is a high-throughput flow reactor for process chemists that enables reaction optimization and production scale synthesis with a few simple adjustments.
Benefits of a compact high-throughput flow reactor system:
- Optimized flow chemistry reaction
- Greater capacity for scale-up and high-throughput reactions
- Ensure critical parameters remain within defined limits
- Carry out superheated reactions up to +260°C (1400 psi) and cooled reactions down to -70°C
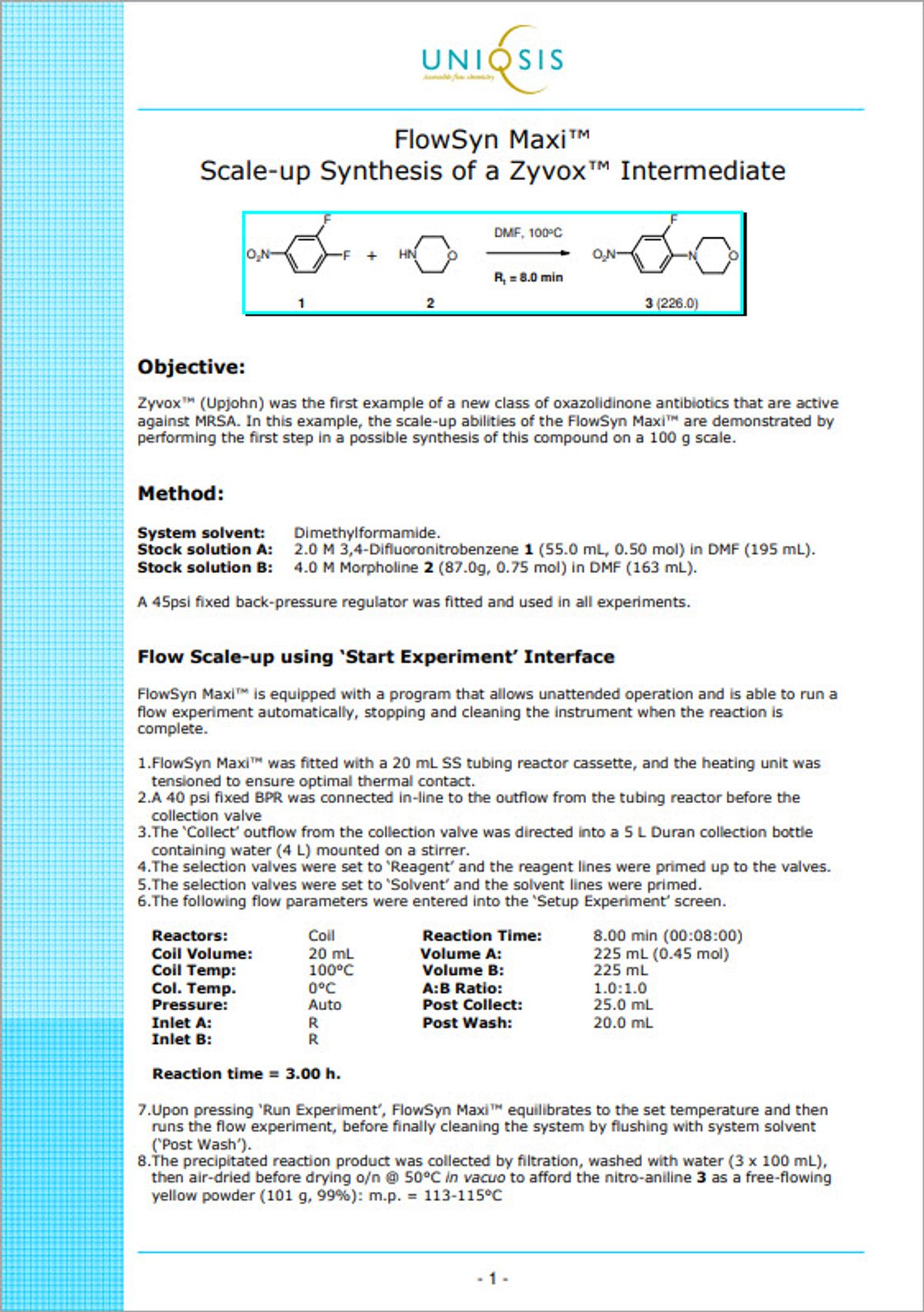
This application note demonstrates the scale-up abilities of the FlowSyn Maxi™ for the first step in the 100g scale synthesis of a novel antibiotic compound. Explore how the above benefits make it one of the most versatile process scale flow reactors available.
Download the free application note today, courtesy of Uniqsis.
FlowSyn Maxi™
Scale-up Synthesis of a Zyvox™ Intermediate
Objective:
Zyvox™ (Upjohn) was the first example of a new class of oxazolidinone antibiotics that are active against MRSA. In this example, the scale-up abilities of the FlowSyn Maxi™ are demonstrated by performing the first step in a possible synthesis of this compound on a 100 g scale.
Method:
System solvent: Dimethylformamide.
Stock solution A: 2.0 M 3,4-Difluoronitrobenzene 1 (55.0 mL, 0.50 mol) in DMF (195 mL).
Stock solution B: 4.0 M Morpholine 2 (87.0g, 0.75 mol) in DMF (163 mL). A 45psi fixed back-pressure regulator was fitted and used in all experiments.
Flow Scale-up using ‘Start Experiment’ Interface
FlowSyn Maxi™ is equipped with a program that allows unattended operation and is able to run a flow experiment automatically, stopping and cleaning the instrument when the reaction is complete.
FlowSyn Maxi™ was fitted with a 20 mL SS tubing reactor cassette, and the heating unit was tensioned to ensure optimal thermal contact.
A 40 psi fixed BPR was connected in-line to the outflow from the tubing reactor before the collection valve
The ‘Collect’ outflow from the collection valve was directed into a 5 L Duran collection bottle containing water (4 L) mounted on a stirrer.
The selection valves were set to ‘Reagent’ and the reagent lines were primed up to the valves.
The selection valves were set to ‘Solvent’ and the solvent lines were primed.
The following flow parameters were entered into the ‘Setup Experiment’ screen.
Reactors:
Coil
Reaction Time:
8.00 min (00:08:00)
Coil Volume:
20 mL
Volume A:
225 mL (0.45 mol)
Coil Temp:
100°C
Volume B:
225 mL
Col. Temp.
0°C
A:B Ratio:
1.0:1.0
Pressure:
Auto
Post Collect:
25.0 mL
Inlet A:
R
Post Wash:
20.0 mL
Inlet B:
R
Reaction time = 3.00 h.
Upon pressing ‘Run Experiment’, FlowSyn Maxi™ equilibrates to the set temperature and then runs the flow experiment, before finally cleaning the system by flushing with system solvent (‘Post Wash’).
The precipitated reaction product was collected by filtration, washed with water (3 x 100 mL), then air-dried before drying o/n @ 50°C in vacuo to afford the nitro-aniline 3 as a free-flowing yellow powder (101 g, 99%): m.p. = 113-115°C
Throughput = 0.15 mol/h (34 g/h).
UVLC-MS (ESI +ve): (m/z 289.12 (MH+)); Rt = 3.60 min, >99%;
IR (ATR): 1595(w), 1495(m), 1470(m), 1380(m), 1234(m), 1120(s), 1098(s), 980(m), 750(s), 690(s) cm-1;
1H NMR (CDCl3, 400 MHz): ?H 7.20-7.30 (m, 8H), 7.10-7.15 (m, 2H), 6.70 (s, 1H).
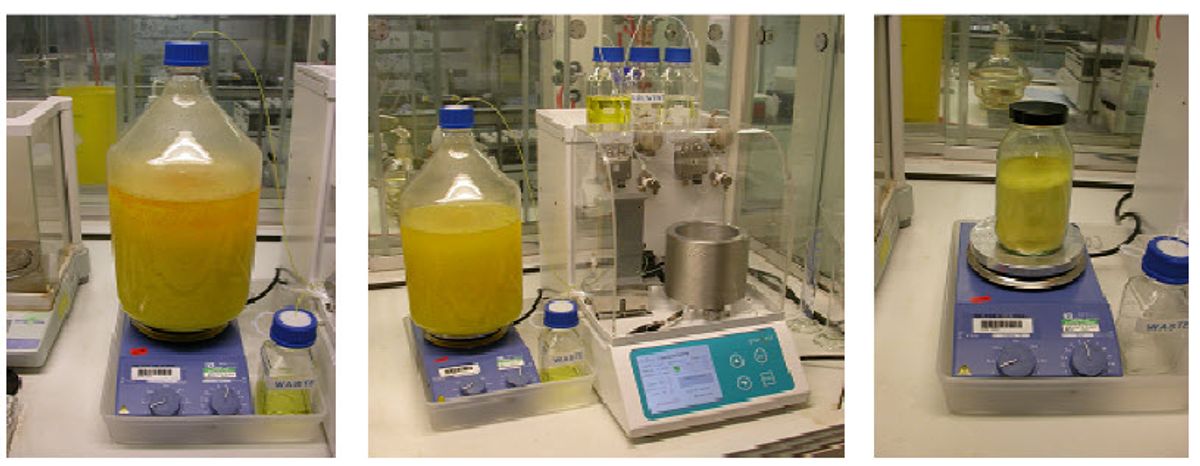
Supplementary Information:
Figure 2. Schematic FlowSyn Maxi™ configuration used.
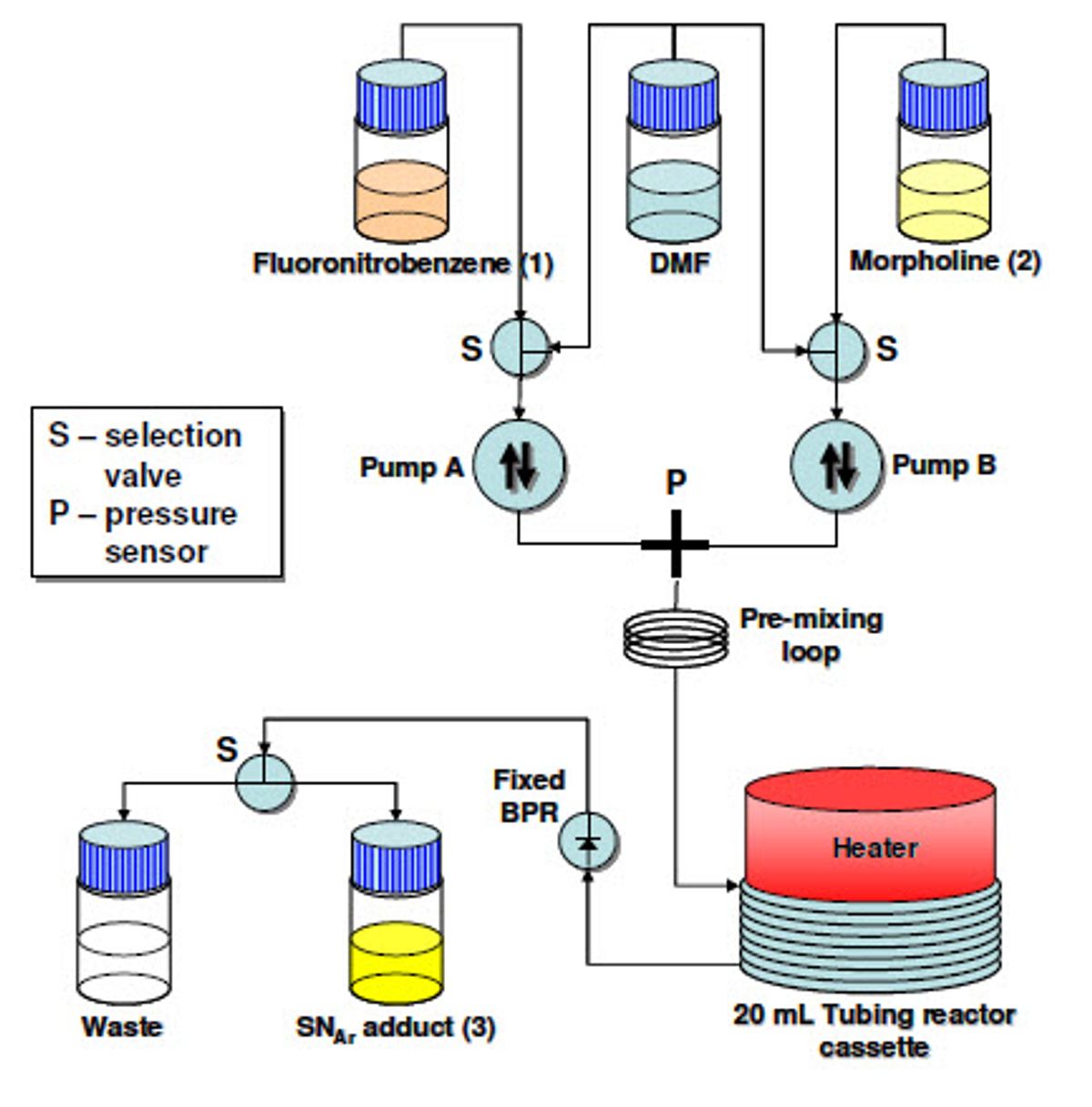