Getting the Story You Need from Your CO2 Incubators
Monitoring CO2 incubators can help clarify repeatability issues, but the details matter
CO2 incubators are essential to the life science industry. Labs rely on these sealed, conditioned chambers to provide stable and ideal environments for sensitive microbiological and cell cultures.
Most scientists and technicians who work with cultures are well-familiar with the effort required to optimize and troubleshoot culture conditions. Minute changes can have large impacts on biological function. Testing and optimizing the media components and conditions—and identifying and controlling sources of contamination—can take considerable time. Even with optimization, results often exhibit frustrating variability that impacts repeatability.
Incubators are designed to precisely control environmental conditions, but their performance depends on multiple factors, including user behavior. Every time the chamber door is opened, internal conditions fluctuate. To ensure repeatability, incubators must be closely monitored. There is a story behind every fluctuation, but only by collecting meaningful data and correctly interpreting multiple streams can the full story be assembled.
What are the critical parameters in monitoring incubators?
Temperature and CO2 levels are likely the first two parameters that come to mind for monitoring incubators in the lab. Though indisputably important, there are several other variables to be considered in a monitoring plan and a great deal more complexity than might first be expected. The first step in assembling the details that form the story is to consider what should be monitored and why.
pH. Regulating media pH is critical for culture health and viability, but it is notoriously difficult to accurately and directly monitor in real-time. Reliability concerns aside, direct pH sensors for continuous use present considerable calibration challenges. Instead, pH is monitored and controlled indirectly through the environmental parameters that affect it.
CO2 plays the biggest role in determining the pH of growth media due to the bicarbonate buffer system most often used. When CO2 dissolves in the culture media, it forms carbonic acid, which then dissociates into bicarbonate ions and hydrogen ions that buffer the media. This relationship enables effective control of the media pH through regulation of the concentration of CO2 in the incubator. Other factors like temperature and humidity have indirect effects on pH and should also be controlled with that in mind.
Temperature. Temperature has a marked effect on cell metabolism, growth, and viability. Slight differences in temperature can have a drastic impact on biological function, such that even placing culture vessels in different locations within an incubator can be detrimental to repeatability. For this reason, it is particularly important to collect accurate measurements in multiple locations within an incubator to assess temperature stability over time and space.
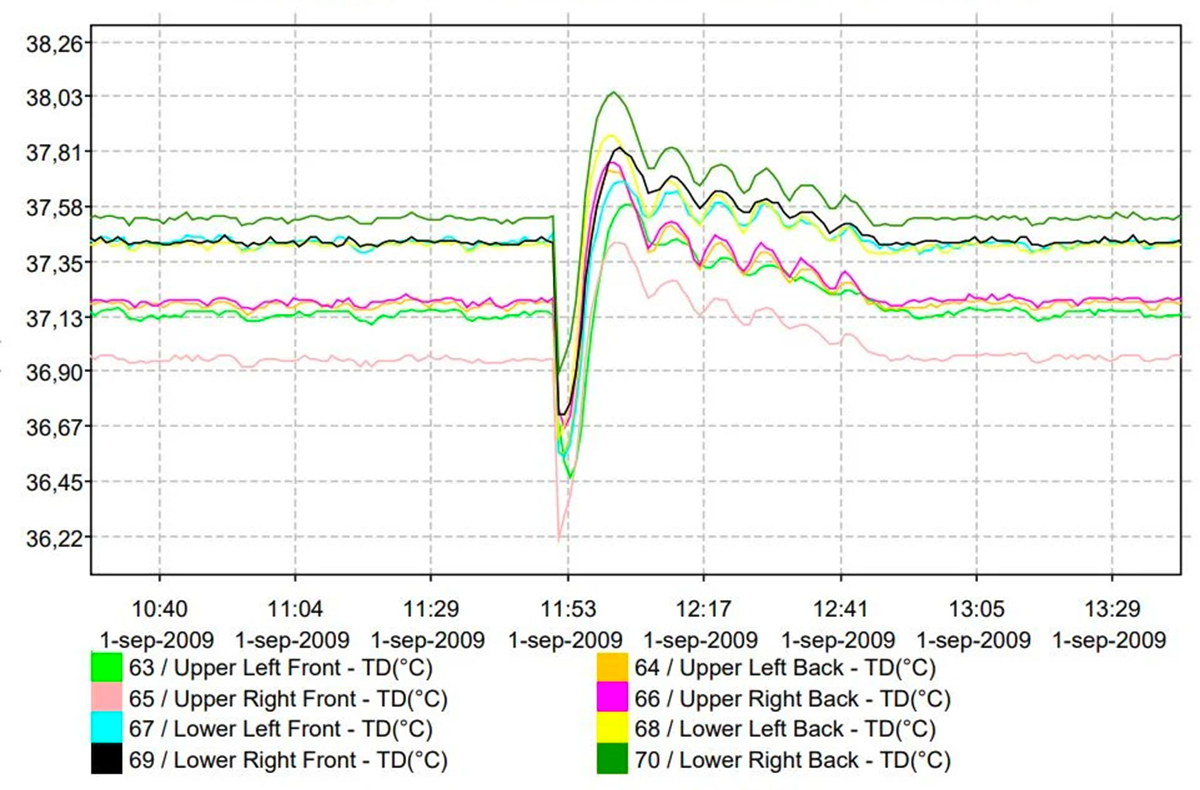
Gases: CO2 and O2. Beyond managing pH, CO2 is monitored and controlled in incubators to establish appropriate physiological conditions and ensure CO2 does not build up as cells respire. Introducing CO2 gas displaces air in the incubator, affecting O2 levels that are in turn significant to most culture applications. Gas flow may also need to be monitored for some applications, such as when pressure differentials are required for safety reasons or gases need to be replaced at constant rates.
Humidity. Relative humidity is the ratio of the actual water vapor pressure of the air relative to the saturated water vapor pressure at the same temperature. Humidity levels drive evaporation and condensation, which can change the concentration of media constituents, cause desiccation or deterioration of samples, or change absorption rates of gases. Condensation can also lead to problems with contamination or interfere with sensors.
Door openings. Opening the incubator door causes a mix of internal and ambient air. The longer the door is open, the more internal and external conditions equilibrate and the longer it will take for conditions within the incubator to recover. A thirty-second door opening can require a recovery time of 30 minutes. Frequent door openings can lead to large fluctuations in all of the above parameters and prolonged instability.
Shaking. Shaking incubators are essential for suspension cultures. Revolutions per minute—or minimally binary alarms—are typically monitored to enable rapid response to mechanical failures that jeopardize the culture.
Backup power. In the event of power supply disruptions, alternate power sources like backup generators or uninterruptible power supplies (UPSs) are critical. Monitoring their activity can help mitigate disasters. Generators and UPSs can both be monitored for on/off states. UPSs should be monitored for lifespan as well. A generator can be further monitored to confirm it is generating amps and the building is receiving power.
Continuous, real-time monitoring of these parameters generates multiple data streams that begin to flesh out the full story, but technical factors must be considered to ensure the accuracy and correct translation of these details.
Understanding sensor technology
Sensors come in a variety of underlying technologies, capabilities, and qualities that can be fairly described as bewildering. Correct deployment and interpretation of the data they generate generally requires technical expertise and experience. This section reviews a few of the factors that can lead to complications in translating the data downstream.
Type of data
Dry contact alarms. These simple alarms connected to sensors are capable of two actions: detecting out-of-specification parameters and triggering an alarm. They could be thought of as a switch, reflecting one of two states. They do not provide any measurements or other conditions, which offers limited information on what is wrong, though some incubators possess multiple dry contact alarms to indicate which parameter is out of spec.
Digital data output. Digital integration of sensors gives users considerably more insight into conditions. Recorded data streams facilitate root cause investigations of any problems, troubleshooting, and assessment of risk to samples or experiments. Of course, data quality depends on sensor quality.
Are the incubator’s built-in sensors sufficient?
Sensors that come integrated into off-the-shelf incubators are built to cost and thus do not have the best accuracy and precision on the market. They also, like all sensors, require regular calibration and checks. For non-critical applications that do not have stringent accuracy and precision requirements, they may be sufficient.
High-quality sensors have high accuracy, low drift, and long lifespans. Industrial-grade sensors are typically recommended for their accuracy, precision, and durability—including resistance to dust, moisture, chemicals, temperature extremes, or other harsh operating conditions.
The technical variability and complexity behind high-quality sensors for different parameters mean their engineering and production are specialized in niche areas. As a result, the best sensors for each parameter are likely to have different manufacturers and software, complicating the purchasing, integration, and management requirements for monitoring. However, “all-in-one” devices on the market that claim to monitor CO2 levels, pressure, temperature, humidity, and light in a single device trade convenience for quality. Initial cost savings are also quickly outpaced by replacement costs.
Determining the best sensor technology for specific needs and applications requires a deep understanding of current capabilities and trade-offs. Incubator conditions are heavily interconnected with numerous confounding factors, and this is frequently reflected in sensor considerations. For example, a high-quality, industrial-grade infrared sensor can offer high accuracy, stability, durability, and selectivity while compensating for temperature and humidity levels.
Interpreting the data
Once you have the right datasets from the right sensors and understand how they’re generated, you will need to know how to contextualize the data to complete the story—and know how to use it. Once you have a temperature dataset, what will you do with it? How will you interpret and apply it?
The good news is that the data streams described above carry a lot of information that can be combined for contextualization. Door openings and parameter readings clarify recovery times and the presence or extent of CO2 or temperature overshoot during recovery. These can highlight appropriate corrective actions, like adjusting settings or standard operating procedures (SOPs). Collectively, the data present an opportunity to monitor adherence to SOPs or other lab behavior.
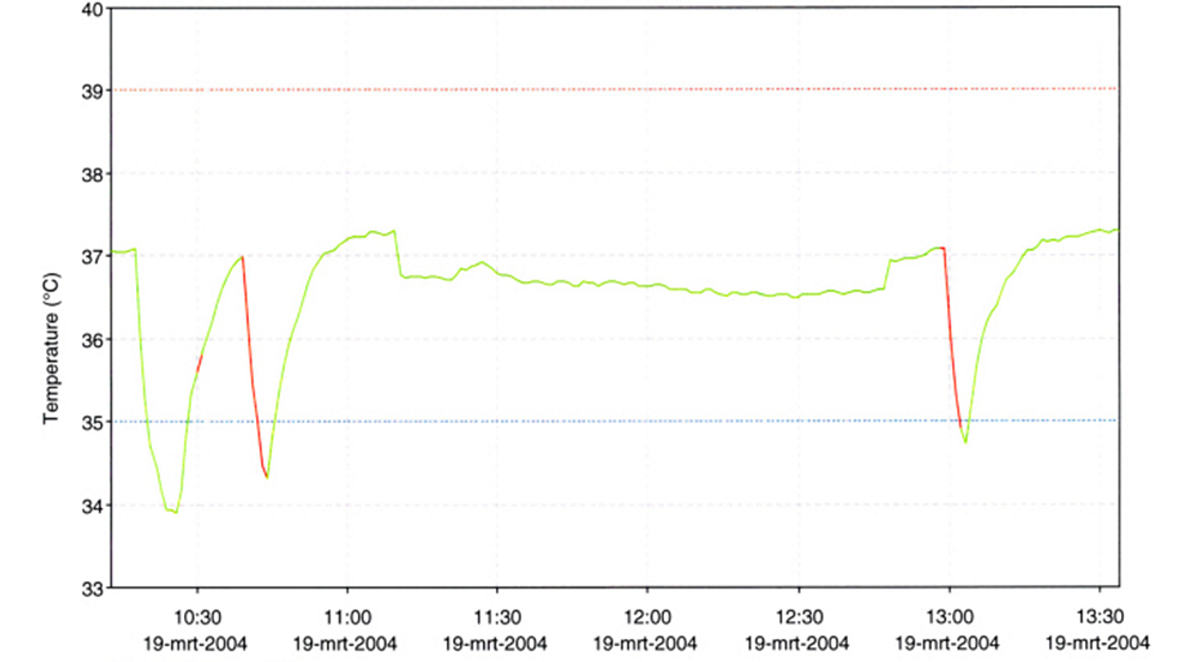
A monitoring service partner can help guide the process of implementing a new monitoring system, ensuring the right questions are asked, sensors are adequately calibrated for accuracy, troubleshooting and solutions are accelerated, and important considerations are not overlooked. They can assist with sensor-agnostic consolidation and interpretation of data across the lab, simplifying outputs with a unified dashboard.
The insights gained from dedicated services, which have seen a myriad of lab issues, are invaluable for acting proactively rather than reactively. Problems can be detected before they arrive. Increasing fluctuations or recovery times produce a data signature that signals an impending need for instrument service or replacement. Recognizing it early is key to proactive intervention. Major issues can arise from a bad combination of seemingly benign conditions that experience can help predict. For example, specific temperature and humidity fluctuations facilitate the evaporation of oils from samples followed by condensation in cool spots, resulting in widespread contamination and instrument malfunctions. Pinpointing the cause of erratic readings can also be accomplished much more quickly with experience. One example of this is condensation collecting on and falling from dangling sensors, forming a pattern of measurement drift, which can be corrected with proper sensor placement.
Ensuring consistent and optimal conditions within incubators is vital in life science research. Minor fluctuations or deviations can significantly impact the results and repeatability of experiments. Thorough monitoring and the correct interpretation of the generated data doesn't just provide assurance, it solidifies the reliability of research outcomes. Your incubator is telling you a story through data that enables informed decisions, but you may be missing it.
Partnering with specialized service providers can help laboratories aiming to comprehensively interpret their incubator conditions and data. XiltriX has extensive expertise and field experience to guide labs through the many challenges in implementing and managing monitoring solutions. Live, 24/7 support from monitoring experts helps scientists resolve issues and learn how to interpret sensor data. As research continues to advance, having access to precise data becomes an indispensable asset. In the world of science where quality and details matter, working with a provider like XiltriX can ensure that you're always one step ahead.
To learn more about monitoring solutions, visit xiltrixusa.com.