Understanding the nuances of evaporator selection and operation is essential for lab managers aiming to maximize efficiency. Streamlining operations by selecting evaporators that match throughput needs and minimize solvent waste reduce costs and support green initiatives. With their crucial roles in sample processing, concentration, and solvent recycling across industries—from chemistry and pharmaceuticals to food analysis and environmental science—key considerations vary based on the application and lab needs. .
Ensuring safety and efficiency begins with purchasing. Understanding factors such as space requirements, sample and solvent types, safety considerations, and throughput is vital for selecting the right evaporator for your lab. This will mean finding the balance between opposing technical elements like solvent volatility and solute sensitivity and operational elements like throughput and space constraints. Comparing the main technologies and their features is equally critical to finding the best solution for an application. Exploring alternative evaporator designs and innovative features opens up new possibilities for enhancing lab efficiency and productivity. From dual-function capabilities to advanced automation, staying informed about the latest advancements in evaporation technology empowers lab managers to make strategic investments that drive long-term success.
Following best practices for maintenance and operation further supports safety and efficiency. Adherence to safety and maintenance protocols helps avoid incidents that can be costly, disruptive, and hazardous to staff. Strategies to mitigate common problems such as solvent bumping and foaming minimize process disruption, sample loss, and contamination. Further, best practices can help ensure equipment longevity and consistent, reliable results.
This exclusive Lab Manager resource guide provides actionable insights and advice to boost lab efficiency, productivity, and safety. Read it to learn:
- Considerations for evaporator selection, including operational parameters and evaporator types
- Safety and maintenance tips to mitigate common hazards and reduce downtime
- How to prevent challenges like solvent bumping and foaming with a variety of solutions to, for example, maintain sample integrity during long evaporation runs
- How more advanced features can substantially cut manual labor and reduce error in sample processing and solvent recovery
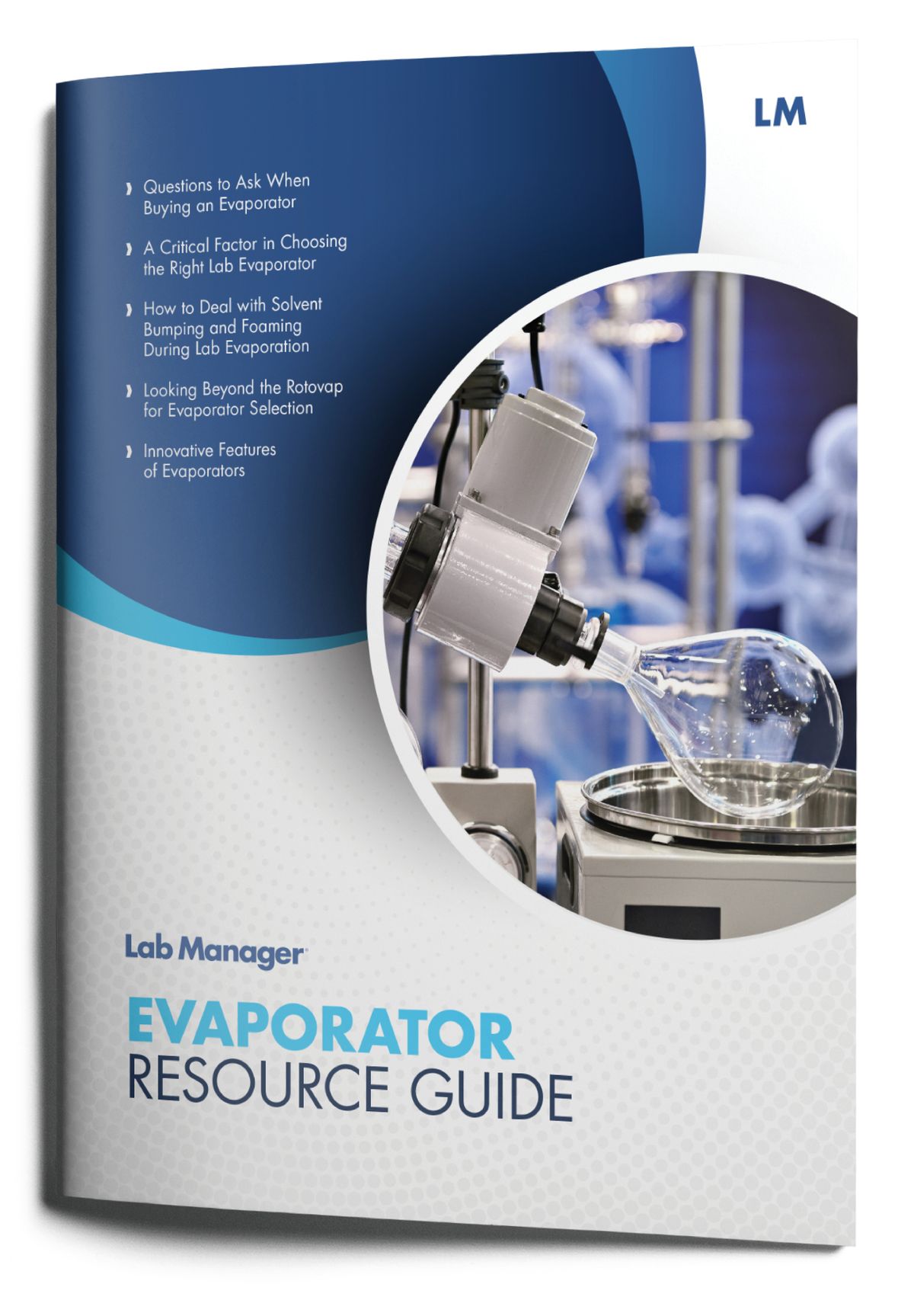
59678_LM_KNF Evaporatos Guide_eBook_AMV-V4
? Questions to Ask When Buying an Evaporator
? A Critical Factor in Choosing the Right Lab Evaporator
? How to Deal with Solvent Bumping and Foaming During Lab Evaporation
? Looking Beyond the Rotovap for Evaporator Selection
? Innovative Features of Evaporators
EVAPORATOR
RESOURCE GUIDE
Questions to Ask When Buying an Evaporator
Selecting an evaporator for your lab, and how to avoid common errors in operation
by Lab Manager
Evaporators remove water or organic solvents from samples, often for sample concentration, solvent recycling, or separat- ing solvent mixtures. They are widely used in pharmaceutical and food and beverage industries, as well as many chemistry and life science laboratories. Rotary evaporators are often used to remove low boiling organic solvents, and the addition of vacuum can lower the boiling point. Nitrogen evaporators apply a steady stream of nitrogen to remove moisture. Cen- trifugal evaporators, ideal for high-volume processing, use vacuum centrifugation to evaporate samples.
7 questions to ask when buying an evaporator:
How much space is available? Is a compact benchtop model or a floor model a better fit for the space?
Will it be used primarily for separation, cleaning, or concentrating?
Will you be working with heat-sensitive samples? Keep in mind a vacuum concentrator can add heat through friction.
What type of samples will you be working with?
What sample volumes will you be working with? Nitro- gen blowdown is ideal for small sample volumes <50 ml.
Will you be processing multiple samples at once? If so, a centrifugal evaporator may suit your needs best.
Operating Tip
Foaming is a common problem that arises during evaporation and can lead to sample loss and contamination. To avoid foaming, use an anti-foam agent, a large flask, or dedicated glass condenser, which provides more space for foam to expand.
What safety features are available?
Tips for choosing the best evaporator for your lab
How will sample type affect which evaporator is ideal?
The sample in question will play a key role in the evaporator setup. For example, if acids are being used, the system must be properly coated to prevent corrosion (especially on the pump) and will need proper ventilation. Solvents can damage rubber and plastic components and should also be protected against. Another important consideration is that different samples are condensed at different temperatures, and may require different cold traps: typically a -50°C cold trap is ideal for aqueous-based samples, a -85°C cold trap traps most solvents, and a -105°C cold trap is recommended for alcohols.
Maintenance Tip
To keep your evaporator happy, you’ll want to look after the seals, glass joints, and tubing, inspecting these parts regularly and replacing when necessary. This will help your system maintain the proper level of vacuum during evaporations. You’ll also want to keep the needles clean so they don’t become plugged or corroded.
How are safety concerns addressed for evaporators?
Due to the nature of heating up aqueous samples, acids, and solvents, a variety of safety accessories can be used to ensure the safety of the operators. As glassware is under extreme pressure due to the vacuum pump as well as being heated, coated glassware can be used to ensure flasks don’t shatter during operation. Shields and protective hoods with ventila- tion can also help ensure operator safety. Some manufacturers offer advanced options, such as motorized lifts and shutoff procedures for power outages or if the heating bath goes dry.
What environmentally friendly options are available for evaporator usage?
Safety Tip
Contact with the water bath or steam can cause scalds or burns—users should always wear safety goggles and a lab coat and have heavy gloves within easy reach. Lab staff should also ensure they don’t overheat the water bath or its contents. To reduce the risk of a solvent fire, users should always keep organic solvents away from the evaporator’s electrical components and the water bath.
For the condensing and collection of samples, many options exist. Condenser coils or cold fingers are generally paired with circulating tap water or dry ice. While these methods are adequate for the purpose, constant changing of water to prevent algae buildup can get wasteful, along with a con- stant need for dry ice. Many manufacturers offer circulating chillers which can be attached to evaporators, allowing for highly efficient condensation without the waste associated with using tap water or dry ice.
A Critical Factor in Choosing
the Right Lab Evaporator
Understanding the balance between sample heat sensitivity and solvent volatility is an important consideration
by Brandoch Cook, PhD
The controlled evaporation of chemicals and biological mole- cules in solution is crucial for many applications. Investigators use it to concentrate analytes to threshold detection levels pri- or to environmental testing, control purity at multiple steps of pharmaceutical production, and preserve biologically active reagents for investigative workflows. The type of evaporator used for each process depends on a delicate balance of ridding solutions of volatile solvents while protecting non-volatile, temperature-sensitive solutes. Although water is the most common solvent and testing matrix, semi-volatile organic compounds often have comparatively higher boiling points, and concentration procedures have to be planned accordingly.
Laboratory evaporators manipulate heat, gas, vacuum, and motion separately or in combination. They are used to steadi- ly remove solvent and therefore concentrate a previously dilute solution, or to eliminate solvent altogether and generate a powder suitable for long-term storage. The widely used rotary evaporator typically employs motorized systems to
rotate a sample flask, and manipulate it to and from a heated liquid bath. A vacuum system and vapor duct additionally divert solvent vapors into a collection flask. The reduced in- ternal pressure created by vacuum above a solution functions to lower solvent boiling point and distill it out at sufficiently low temperatures to preserve the chemical structure of the solute or analyte. As an added benefit, recovered solvent can be recycled into downstream procedures, mitigating waste and expense.
During the initial stages of solvent phase change, natural evaporative cooling properties are at their peak, and the greatest amount of heat can be applied with the least risk to the sample. Subsequently, as volume decreases, the sample itself attains greater risk of molecular damage, tragic events such as bumping or foaming, and the fouling of heat transfer surfaces with thin concentrated films. Optimal transition and timing between high and low temperatures can most efficiently yield the highest quality analytes. These princi- ples extend into other evaporation/concentration platforms that fit different needs intrinsic to sample size, number, and desired outputs.
Gas blowdown evaporators introduce heat and nitrogen through vertical needles to volatilize solvent and promote evaporative cooling. This procedure is especially useful with multi-well plates in preparation for HTS or GC/LC-MS protocols, although it is applicable for multiple samples up to about one liter in volume.
Vacuum centrifugation-based concentration can handle up to hundreds of smaller samples, and can maximize throughput for extraction procedures, or speed evaporation by distribut- ing starting volumes across many smaller vessels. Again, there is a delicate balance between evaporative cooling and heat sensitivity as cooling plateaus and then subsides. Monitoring
correct temperature and flow of nitrogen is critical. Centrif- ugal rotor hubs generate heat at high speed that can damage samples unless instrumentation is refrigerated with a con- trolled cooling system.
Finally, for preservation of biological activity, especially for large-volume and highly heat-sensitive samples, lyophiliza- tion is often optimal. Here, patience is paramount, as samples must first be fully frozen before applying heat and vacuum to sublimate water or other solvents.
There is a versatile array of instrumentation to evaporate solvent and concentrate chemical and biological samples, for which considerations of heat sensitivity and volatility must coordinate with sample number and size.
Must-Have Features for Your Rotary Evaporator
While many features are standard to all rotary evaporators, there are several additional features that will promote versatility, connectivity, and automation in your rotary evaporator.
Rotary evaporators, or “rotovaps,” are standard equipment found in nearly all laboratories. Chemical, pharmaceutical, food, and environmental industries are the most common users, but rotary evaporators may be found wherever
Download the full infographic compliments of Lab Manager
processes require sample concentration or solvent distillation. While all rotary evaporators include a set of basic components, certain features may be added to promote greater versatility, connectivity, and automation.
Lab Manager 5
All rotary evaporators include..
ROTARY
How to Deal with Solvent Bumping and Foaming During Lab Evaporation
Both products and techniques can help reduce these issues
by Erica Tennenhouse, PhD
Bumping and foaming are problems that commonly arise during evaporation and can lead to sample loss and contami- nation. The primary culprits of these challenges are too much rotational speed, too much heat, or too much vacuum for a particular application.
Bumping occurs when the sample boils and bubbles rapidly, causing the product that is being concentrated to splash out of the vessel.
Foaming, on the other hand, results from surfactants, or com- pounds that lower the surface tension, which can be found in natural extracts and artificially made products. Foaming is a
slower process than bumping and foam tends to stay inside the evaporating flask for a longer period of time.
Tricks of the trade
The traditional way to avoid bumping during evaporation is through visual inspection—simply watching the samples and adjusting the vacuum pressure so that bumping doesn’t occur. Foaming cannot be avoided per se; it can only be reduced.
The most common method to avoid this phenomenon is to manually open and close the stop cock whenever foam appears. Another way to diminish the issue is to gradually apply vacuum.
Along with these methods, several products are available that can reduce sample loss and contamination when bumping and foaming occur, help eliminate bumping altogether, and minimize foaming.
Bump traps, foam brakes, and more
To specifically address the issue of foaming, experts suggest using an anti-foam agent, a large flask, or a dedicated glass condenser, which provides much more space for foam to expand. In addition, a simple glass foam brake can help keep foam from entering the receiving flask.
A bump trap, which is a secondary flask that is smaller than the main flask, is also often used during evaporation. This additional flask is placed right above the main flask so that if bumping occurs, the sample will get caught in the bump trap before getting drawn into the rest of the rotary evaporator or condenser. The solution is not elegant as putting a bump trap in line doesn’t actually reduce bumping, but it does prevent sample loss.
Automation advances
Vacuum controllers get closer to the root of the problem. By controlling the speed of the pump, these devices can drasti- cally reduce or eliminate the likelihood of bumping.
New vacuum controllers have an automatic feature that senses the vapor pressure of the solvent and uses that as a set point. This feature allows the user to optimize the speed of evaporation without bumping.
Then there are foam sensors, which can detect the foam inside an evaporating flask and aerate the system slightly to
ensure collapse of the foam. Using a foam sensor allows for automatic, unattended distillation of foaming samples.
Automation might be the ideal solution to bumping and foam- ing. Automatically adjusting vacuum using automation can allow users to manage the conditions.
However, despite all these advances in automation, many chemists still prefer to make manual adjustments. Budgetary constraints may be part of the reason, but there are also sea- soned and patient chemists who simply feel more comfortable with the manual methods they have always used.
Product Spotlight
Next-Generation LABOPORT® Vacuum Pumps—Unique Design for Lab Life
A new series of three KNF diaphragm pumps expands upon the proven LABOPORT pump innovations of oil-free, non-contaminating, chemically-resistant construction with a modern look and added benefit of speed-controlled DC motors for greater versatility. The new pumps also feature exceptionally small footprints (10 – 20 percent reduction) and lighter weight (5 – 30 percent reduction) for improved portability.
A color display indicates pump status at a glance. Smooth rounded surfaces enable easy, thorough cleaning. An integrated gas ballast valve in the two larger models facilitates short process times, even for high-boiling solvents.
These two models are also expandable with optional separator and/ or condenser modules. This approach provides a cost-efficient way to expand pump functionality as needs grow.
Maximum flow rates for the new series ranges from 7 – 34 L/min with ultimate vacuum levels from 97.5 – 4.5 torr. Applications include rotary evaporation, degassing, filtration, SPE, fluid aspiration, gel drying, centrifugal concentration, vacuum ovens, and more.
Looking Beyond the Rotovap for Evaporator Selection
Lab managers might consider designs other than standard, single-bulb rotary evaporators
by Angelo DePalma, PhD
Evaporation is a staple of most biology and chemistry labs. Depending on sample size and composition, solvent type, and required throughput, laboratory managers might consider designs other than standard, single-bulb rotary evaporators.
One drawback of standard rotary evaporator models is that the evaporator, bath, hoses, etc. occupy too much bench space for just one sample. Multiflask designs multiply the sample- per-square-foot value proposition since they employ one bath, one condenser water source, and one solvent recovery flow path for up to 10 samples.
Nitrogen blowdown units use an entirely different process. Samples are heated in a water or dry aluminum bead bath. As the sample heats, nitrogen blows across the surface of the liquid. As anyone who has tried one-off nitrogen-blowdown evaporation knows, the process can be slow, and it becomes
even slower with high-boiling-point solvents. Using con- trolled heat in evaporation can help speed up this process. However, blowdown should not be used for very large samples as the higher the boiling point, the slower the evaporation.
With water bath temperatures limited by the 100°C barrier and solid bath temperatures reaching about 120°C, users need to assess the suitability of blowdown evaporators for high-boiling solvents like toluene and dimethyl sulfoxide. Solvent removal in those instances is usually accomplished by addition of water to polar aprotic solvents followed by extraction, or, in the case of high-boiling hydrocarbons, by extraction alone.
There are vacuum and nitrogen blowdown evaporators avail- able that use dry block heat to keep sample flasks in direct contact with the heat source. This configuration eliminates the need for a water bath, which can reduce system main- tenance and potential contamination. Centrifugal vacuum concentrators are also available. These multiple-sample evap- orators use centripetal force, dry heat, and vacuum to quickly remove solvents.
Best practices
Operational and safety best practices are similar between waterbath evaporators and conventional rotovaps. Bump- ing—the sudden, nonevaporative flow of sample through the solvent recovery path—is a common problem when either heat or vacuum is applied rapidly. Splash or bump traps usually suffice to prevent the sample from traveling all the way to the solvent collection vessel.
Adding a boiling chip when such problems are anticipated can help prevent bumping. Users should also watch the flow of nitrogen when using blowdown systems. The surface of
Evaporator Resource Guide
the fluid should be moving, but not so strongly that it causes splashing, which can result in sample cross-contamination. While solvent recovery from blowdown evaporators is impossible, solvent reservoirs for closed, bath-type systems fill very quickly with solvent of varying purity, dryness, and composition. This “product” can serve directly, or after rudimentary drying, in noncritical applications such as glassware washing or rinsing, or in extractions from aque- ous suspensions. Given the price of high-purity solvents, many large research groups recycle evaporated solvents to reagent grade or above.
Lab managers should focus on sample needs when selecting an evaporator (or concentrator). The first consideration is sample volume, as systems using heat baths or blocks typi- cally accommodate larger samples than nitrogen-blowback
evaporators. Heat-sensitive or volatile samples will require a higher degree of temperature control, and possibly refrig- eration as well, to remove solvents efficiently while preserv- ing the sample.
You should also make sure you have the required accesso- ries to help with solvent recovery such as chemical traps, cold traps, one or more trapping valves, etc. Experts advise to, when purchasing, look for flexibility in design and lay- out, for example floor versus benchtop models.
Some manufacturers recommend conducting evaporations in a fume hood and carrying out cleaning periodically with the solvent you’re evaporating to prevent future cross-contamination.
Innovative Features of Evaporators
Tapping into new features of evaporators can boost research productivity
by Andy Tay, PhD
There are three main uses of evaporators in the lab. Most typical evaporators—except evaporator concentrators—apply heat directly to the sample with a heating block (a dry evap- orator) or water bath (a wet evaporator) while maintaining a vortex motion to mix the sample and boost evaporation. They help remove water or organic solvents to concentrate the samples, recycle solvents, or separate solvents.
Rotary evaporators are typically used to remove low-boiling organic solvents. With a vacuum, they can further reduce the boiling point of solvents to accelerate evaporation under reduced pressure. Another common evaporator uses nitro- gen gas, which enhances the rate of evaporation by blowing nitrogen across the sample surface. Evaporators are used extensively in the pharmaceutical industry, toxicology, and environmental testing for sample purification and analyses. Here, we highlight innovations in evaporators to enhance your research productivity.
Dual functions
Not all commercially available evaporators can both evapo- rate and concentrate. For separation purposes, samples can be heated directly to remove solvents. If the sample is not heat-sensitive, it can be concentrated using direct heat. How-
ever, for biological materials that can be denatured by heat, such as peptides and nucleic acids, there are evaporator con- centrators that instead generate centripetal motion within the sample tube to evaporate the solvent. Although this process
is more time-consuming, it protects the biological activity of the analyte.
Heating rate
Manufacturers have introduced digital controllers to manage heating and rate of temperature change. This is helpful to prevent overheating and to maintain a constant temperature to optimize the evaporation rate. Another innovative feature is the fast termination of heating after the set end point is achieved. This is important because operators need time to remove samples or perform additional procedures. However, if there is still heat transfer, evaporation does not stop, and the sample might dry out. This may be problematic for samples where a small amount of solvent is needed to maintain struc- tural integrity and bioactivity.
Throughput
While wet evaporators can handle larger sample volumes than dry evaporators, the former can only work on one sample at a time. Innovations in dry evaporators have enabled as many as 100 samples to be processed concurrently. This can be helpful for labs with high throughput needs, especially when they are trying to optimize a chemical synthesis process and require concentrated analytes for downstream analysis.
User interface
A good user interface is important so users can easily and accurately regulate heating rate and pressure. Older evapo- rators do not offer digital interfaces, so users must manually adjust parameters. On the other hand, new evaporator models are equipped with digital user interfaces that display vortex
Evaporator Resource Guide
speed, heating block temperature, time, and vacuum levels. They also have alarms to notify users when the process is near completion or completed. Users can also save programs for easy recall and protocol modifications.
Featured Manufacturer
KNF Neuberger, Inc. is a leading manufacturer of reliable oil-free laboratory vacuum pumps, systems and controllers, liquid dosing/metering and transfer pumps, and rotary
evaporators. All KNF laboratory products offer compact design, long service life, and dependable performance. Contact KNF Neuberger today to discuss your specific laboratory needs.