Incubator shakers are commonly used for cultivating cells and microorganisms, as many chemical and biological processes rely heavily on their control of temperature and shaking speed. For instance, temperature fluctuations can induce structural changes in proteins, leading to a rapid loss of function and erroneous results. However, achieving and maintaining precise control of temperature and shaking speeds has proven challenging for many labs.
Space limitations can further complicate operations. The typical physical footprint of incubator shakers, combined with their need for sufficient clearance for ventilation and maintenance access, can make placement challenging. This can restrict throughput and hinder the scalability of operations.
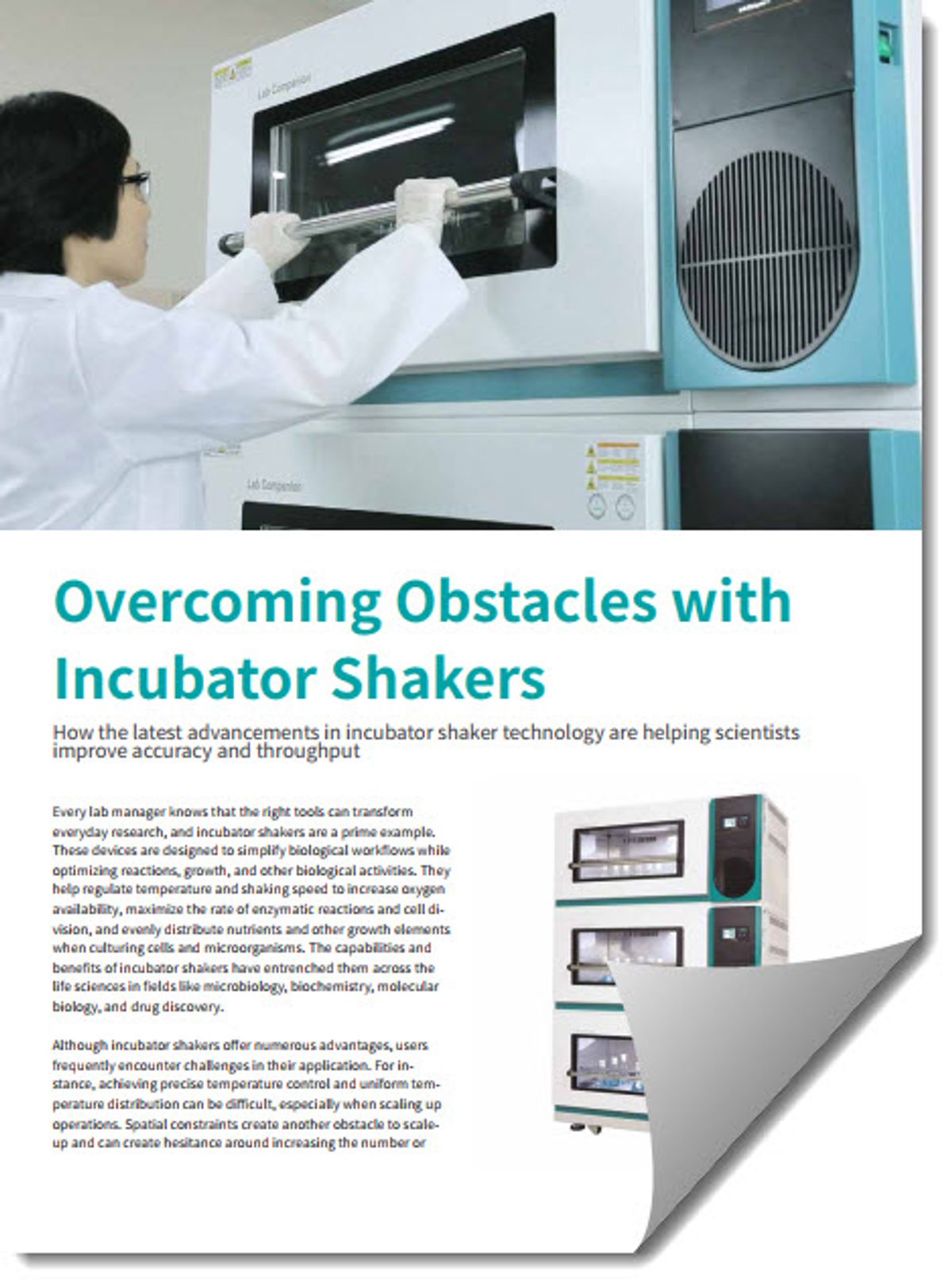
Fortunately, the latest advancements in incubator shaker technology address these pain points, offering innovative features that help labs maintain experimental integrity and boost efficiency. By equipping themselves with a thorough understanding of these features, lab managers can make informed decisions that ultimately improve research outcomes.
This comprehensive white paper explores these technological advancements and provides lab managers with practical strategies to overcome common challenges. It also includes a detailed, step-by-step guide for optimizing protein expression workflows using an incubator shaker.
Download this whitepaper to learn:
- Best practices for maintaining precise control over temperature and shaking speed
- Strategies to maximize lab space and throughput
- Benefits of real-time monitoring and advanced safety features in incubator shakers
- Key features to look for when purchasing an incubator shaker
- Practical steps for optimizing protein expression workflows
68803_LM_JeioTech_Article_PROOF4
Overcoming Obstacles with Incubator Shakers
How the latest advancements in incubator shaker technology are helping scientists
improve accuracy and throughput
Every lab manager knows that the right tools can transform everyday research, and incubator shakers are a prime example. These devices are designed to simplify biological workflows while optimizing reactions, growth, and other biological activities. They help regulate temperature and shaking speed to increase oxygen availability, maximize the rate of enzymatic reactions and cell di- vision, and evenly distribute nutrients and other growth elements when culturing cells and microorganisms. The capabilities and benefits of incubator shakers have entrenched them across the life sciences in fields like microbiology, biochemistry, molecular biology, and drug discovery.
Although incubator shakers offer numerous advantages, users frequently encounter challenges in their application. For in- stance, achieving precise temperature control and uniform tem- perature distribution can be difficult, especially when scaling up operations. Spatial constraints create another obstacle to scale- up and can create hesitance around increasing the number or
size of incubator shakers in the lab, ultimately restricting efficien- cy and throughput. Lab managers can address these challenges and enhance the utility of incubator shakers by considering both strategic approaches and advanced equipment features.
Maintaining experimental integrity through temperature consistency
Many chemical and biological processes, such as protein expres- sion, depend heavily on temperature. For instance, microbial cul- tures' growth rate and metabolism, which directly affect product yields, are highly susceptible to temperature fluctuations. Precise temperature control is also essential when studying proteins,
as variations can induce structural changes, such as misfolding aggregation, or denaturation, leading to a rapid loss of function and erroneous results. Any temperature deviations or uneven heat distribution within an incubator can also produce unreliable and inaccurate data, altering research outcomes and leading to significant setbacks.
To mitigate these challenges, labs must implement robust pro- cedures that maintain equipment reliability and accuracy. This includes regular validation and calibration, temperature monitor- ing during operation, and optimizing sample placement within the incubator shaker to promote air circulation and uniform temperature distribution. However, adopting incubator shakers equipped with advanced temperature control features reduces the need for such manual interventions. These machines often come equipped with digital control systems that help maintain consistent and accurate temperatures, a broad temperature range to support diverse experimental needs, and integrated sensors that continually monitor conditions inside the chamber to ensure they align with set parameters.
Remote and real-time monitoring capabilities are another valuable addition to incubator shakers, facilitating the quick identification and correction of deviations. Additionally,
over-temperature protection-complete with visual or audible alarms-safeguards samples from heat damage by automatically disabling the heat source if internal temperatures exceed prede- termined thresholds. Real-time self-diagnostics further protect sample integrity by continually monitoring for operational issues like temperature fluctuations or system instability, providing early warnings that minimize the risk of experimental failure.
To improve consistency, incubator shakers should come equipped with features that combat temperature loss. This may include tight door seals, which act as thermal barriers, and door open alarms, which serve as reminders to keep the door closed. Additionally, selecting an incubator shaker with an internal fan can promote uniform heat distribution and rapid thermal recov- ery after door opening.
Navigating spatial constraints and increasing throughput
In any lab, effective space management is important for ensuring the proper function of all equipment. This is especially true for incubator shakers, which need sufficient clearance for ventilation and overheating protection. Clearance is also crucial for maintain- ing operational integrity and longevity and facilitating easy access for operation and maintenance. Depending on their size, incubator shakers typically require at least one inch of clearance for smaller units, and up to four inches for larger units, which can restrict placement options. As a result, labs with limited space may opt for smaller incubator shakers that limit experimental throughput.
Lab managers can ensure operational efficiency, maximize their space, and avoid unnecessary reorganizations by carefully consid- ering their options before purchasing an incubator shaker. There are several options available including benchtop, floor-standing, and stackable models. Benchtop units are ideal for smaller labs, of- fering a compact design that makes efficient use of available bench space. For larger facilities requiring greater capacity, floor-standing models are a good option as they can handle larger sample vol- umes and loads. Labs that need to maximize capacity or through- put but are space-constrained can capitalize on vertical space with stackable incubator shakers. Investing in stackable units also offers the greatest flexibility for labs anticipating changing needs.
The JeioTech incubator shaker
JeioTech has designed its incubator shakers with user needs in mind by addressing common lab challenges and ensuring their products meet dynamic research needs. These systems have three operational modes: temperature and shaking, temperature only, and shaking only. They also feature orbital shaking capabilities with a soft start and stop function for gentle, thorough mixing, and advanced digital temperature controls ranging from 20°C below
ambient to 80°C. Precise temperature management is achieved through temperature auto-tuning, a microprocessor PID system, and three-point temperature calibration. These features, com- bined with a high-velocity fan and an air-tight silicone door seal, ensure spatial and temporal consistency with uniform temperature distribution and rapid thermal recovery after door opening.
"Any temperature deviations or uneven heat distribution within an incubator can also produce unreliable and inaccurate data, altering research outcomes and leading to significant setbacks."
The system is equipped with several features that ensure optimal performance, including a real-time self-diagnostic system that con- tinuously monitors the actual rpm and temperature, comparing them against preset values. Based on this information, the system makes automatic adjustments in response to device instability or shuts down the machine if abnormal conditions are detected. An optional remote and real-time monitoring service is also available. This service alerts users of any temperature deviations, which is particularly helpful for experiments requiring continuous monitor- ing or extended operation.
Sample integrity and the lab environment are also protected through comprehensive safety features, including overcurrent protection, a controller lock function that prevents accidental
adjustments, and a triple-independent temperature monitoring system. This system includes a temperature deviation alarm and both electronic and conventional over-temperature protection systems. The electronic over-temperature limiter, equipped with a precision temperature sensor and controller, automatically
disables the heating element if the temperature exceeds set limits. Meanwhile, the mechanical over-temperature limiter acts as a fail- safe, protecting against excessive temperatures even if electronic systems fail.
With benchtop, floor-standing, and stackable models available, JeioTech offers solutions tailored to the diverse needs of any lab. Each model is designed to enhance user experience with features like a glide-up door and slide-out platform, facilitating safer and easier sample access compared to platforms with detachable structures. The unit is also compatible with various accessories such as flask clamps, microplate holders, funnel holders, attach- ment platforms, sticky mats, spring wire racks, and test tube racks. These accessories support different container types, allowing users to design experiments with greater flexibility.
Optimize Protein Expression with Incubator Shakers
See the step-by-step guide below to learn how incubator shakers can help you optimize your protein expression work- flows, from culturing cells to inducing and evaluating protein expression.
Built with durability and versatility in mind, JeioTech incubator shakers are a reliable, efficient, and adaptable solution for any lab looking to enhance its research capabilities.
To learn more, visit www.jeiotech.com
Plate transformed cells on solid media with antibiotic(s) and incubate overnight, then resuspend one colony in liquid culture with antibiotic(s) and incubate with shaking overnight
Inoculate a new liquid culture containing antibiotic(s) with the overnight culture for expression, then incubate with shaking
Step-by-step guide to optimizing recombinant protein expression
Once the culture reaches the optimal OD600, add an inducer and return it to the incubator shaker
Harvest cells by centrifugation and lyse, then evaluate protein expression using an SDS-PAGE or other suitable technique
Set temperature and agitation speed based on your culture's optimal range1
Monitor the culture
Is there foam or spillage?
YES
Decrease speed
by 10-20 rpm
NO
YES
Is there cell death or discoloration?
Decrease temperature by 1-3°C
NO
Is there visible growth?
NO Increase
temperature by
1-3°C or speed by 10-20 rpm
YES
Monitor the OD600
2
Add inducer3
Place in incubator shaker4
Harvest cells by centrifugation and lyse5
Evaluate protein expression
Is protein yield as expected?
NO
YES
Are there inclusion bodies?
Switch to the slow induction method4,6
YES
NO
Optimal conditions achieved
YES
Did the medium look turbid?
Induce at a lower cell density6
NO
Induce at a higher cell density6
E. coli is typically cultured at 37°C with agitation speeds of 200-250 rpm. When using a different bacterial strain, consult the literature for studies or protocols specific to your bacterial host. The preferred environment of the bacteria-whether they are thermophiles, mesophiles, or psychrophiles-can also provide clues about their optimal growth conditions.
Inducer is typically added when the OD600 falls between 0.2-0.8. The OD600 should be checked every 30 minutes to an hour following induction for new bacterial strains, and every one to two hours for routine culturing.
IPTG, at a final concentration of 0.1 to 1.0 mM, is one of the most commonly used inducers for protein expression in E. coli
and other bacterial systems under the control of the lac promoter or its derivatives.
There are two common protocols for induction: fast (~37°C for three to five hours) and slow (~20°C for 12-16 hours). Fast may not work for all proteins and can give suboptimal yields, while slow induction can enhance the solubility of some proteins.
A time-course analysis by SDS-PAGE of protein expression after induction can be performed to determine the optimal induction period.
Cellar debris is pelleted out using centrifugation. The cells in the supernatant can then be lysed via physical disruption (e.g., sonication and French press) or solution-based cell lysis.
600
Inclusion bodies can also be reduced by inducing at lower cell densities, for shorter periods, and with lower concentrations of the inducing agent. Adjust the OD in increments of 0.1-0.2 to modify cell density, incubation time in increments of one to two hours, and inducer concentration in increments of 0.1 to 0.2 mM.