Proper maintenance and care of incubators are instrumental in the support and growth of live samples. Regularly maintaining and caring for your incubator ensures your unit remains consistent in performance and sustains precise conditions over extended periods for successful experiments and reliable results. This is vital for cell health and viability, preventing contamination, data reproducibility, calibration and accuracy, and instrument longevity.
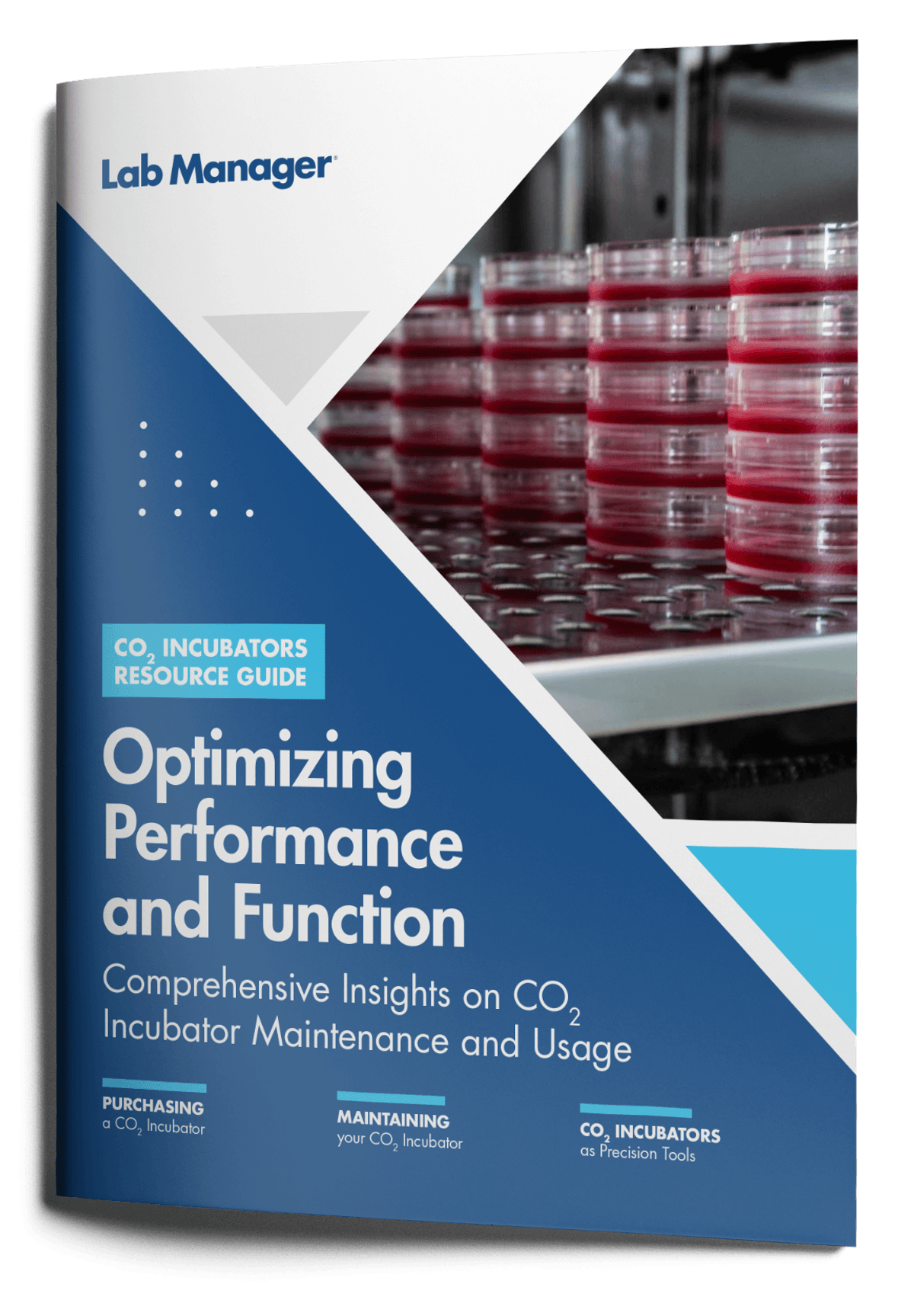
Starting from manufacturer guidelines and recommendations, various tasks must be considered when performing maintenance on your incubator. This includes routine cleaning of interiors, calibration of parameters, physical inspection of the unit, and other aspects such as the airflow and gas supply, to name a few. Keeping up with these tasks helps improve repeatability and prevent contamination, contributing to healthy, productive cultures.
Timely maintenance of your incubator ensures trouble-free functionality and accurate results predictive of the in vivo environment. While the relevant steps may differ depending on the incubator model, there are several best practices for labs to adapt.
In this eBook, you will learn about:
- Guiding principles on purchasing a new incubator
- Critical specs and parameters to evaluate and properly maintain your incubator
- Preventing biological contamination in your incubator
- Insights on incubators as precision tools for drug discovery and temperature-dependent growth of microorganisms
66235_LM_Co2 Incubaters_AV_V3
CO2 INCUBATORS RESOURCE GUIDE
Optimizing Performance and Function
Comprehensive Insights on CO2 Incubator Maintenance and Usage
PURCHASING
a CO2 Incubator
MAINTAINING
your CO2 Incubator
CO2 INCUBATORS
as Precision Tools
Table of Contents
3 Unlocking Successful Growth: Incubator Maintenance and Care
4 Buying an Incubator: Questions to Ask and Suggestions to Consider
6 Maintenance Matters: CO2 Incubators
8 How to Prevent Biological Contamination in Your CO2 Incubators
12 Comparing Cooling Technology in Refrigerated Incubators
2 Lab Manager
14 CO2 Incubators: Precision Tools Driving Drug Discovery Success
Introduction
Unlocking Successful Growth: Incubator Maintenance and Care
Proper maintenance and care of incubators is instrumental for the support and growth of live samples
Regular maintenance and care of an incubator can go a long way toward ensuring that the system can sustain consistent and precise conditions over extended periods for successful ex- periments and reliable results. As indispensable tools for growing a wide variety of organisms in the lab, proper maintenance of incubators is important for cell health and viability, prevent- ing contamination, data reproducibility, calibration and accuracy, and instrument longevity.
A good starting point is to follow manufacturer guidelines and recommendations for your specific incubator model when performing maintenance tasks. These tasks can range from routine cleaning of interior surfaces, calibration of sensitive parameters (temperature, CO2, O2, and humidity), inspecting gasket door for wear and tear, airflow, water pan, and gas sup- ply, as well as alarm testing, and record keeping. Keeping up with these tasks helps improve repeatability and prevent contamination, contributing to healthy, productive cultures.
Modern incubators can offer improved environments for cell culture with features focused on increased stability and precision. Timely maintenance ensures trouble-free functionality of these systems and further supports the integrity and health of live samples while guaranteeing accurate results predictive of the in vivo environment. Depending on the incubator model, the type and fre- quency of maintenance required may vary but there are several best practices that labs can adapt.
This e-book will guide you in getting started with maintaining and taking care of your incubator. Here, you will find the necessary steps for regularly
maintaining your incubator to best serve your lab’s cell culture needs. Beginning with the right questions to ask when purchasing an incubator, this e-book discusses crucial parameters and specs to evaluate in properly maintaining your unit and preventing biological contamination. As tools for sample growth, incubators feature prominently in various applications. Closing discussions provide a window into this world with insights on refrigerated and CO2 incubators that cater to a wider range of temperature-dependent growth of microorganisms and their application as precision tools for drug discovery.
Buying an Incubator: Questions to Ask and Suggestions to Consider
Incubators allow researchers to create optimal environments for growing a wide variety of organisms and cultures
by Lab Manager
Asking the right questions is the first step toward finding the incubator that best matches your lab’s specific needs and
standards while also accommodating its budget. The following questions and suggestions can help kick-start your search:
1
What capacity do you need now and in the foreseeable future?
Look at the internal volume of the incubator and how many shelves or trays it can accommodate.
2
What level of consistency, precision, and accuracy in temperature and CO2 conditions is required for your workflows?
Look for specifications on uniformity of conditions within the chamber and across time.
3
How quickly does the unit recover after door openings?
Check specifications on the accuracy and precision of con- trols and sensors as well.
4
Do you need humidity control or O2 control for hypoxic or hyperoxic experiments?
Check the range offered by the incubator, how it is main- tained, and what additional hookups are required.
5
What features does the incubator have to prevent contamination (e.g., HEPA filters, UV sterilization, high-temperature decontamination cycles)?
Consider how you will address contamination risks not cov- ered by the features. Look for easy-to-clean interiors with rounded corners and make note of creases or crevices where contaminants could hide.
6
What monitoring, and backup features are available?
Look for options for remote monitoring and alarms for temperature, CO2, and humidity deviations. Ask if alarms are built in, and if yes, how are notifications routed? If there are no onboard remote monitoring features, can it be connected to an existing lab monitoring system? Check for a backup power system or battery in case of power failures as well as a backup CO2 delivery system.
Disinfecting your Incubator
While incubators may differ in design and performance, an ideal unit must demonstrate and enable precise control of temperature, CO2, and possibly O2. Contamination is often the biggest concern with incubators. As such, lab managers must pay special attention to incubator design to facilitate appropriate maintenance, disassembly, cleaning, disinfection of the unit, and reassembly. Unlike manual cleaning and autoclaving which may take up precious time and costs, automated disinfection is
also a recommended alternative. Most importantly, the disinfection protocol should not introduce contaminants into the unit or pose harm to the cells being grown.
7
Does the incubator have safety certifications from recognized organizations?
Look for safety features like over-temperature protection.
8
Assess the total cost of ownership, including delivery, installation, after-sales service or maintenance plans, staff hours for cleaning and maintenance, and con- sumables or other replacement parts including HEPA filters, etc. Are there any user-serviceable parts, and what is the frequency of maintenance?
Check the warranty’s duration and coverage.
CO2 Incubators
CO2 incubators are the heart of cell-based work in many labs. When they stop, the lab stops. Yet, these units are often ignored until disaster strikes.
by Rachel Muenz and Ajay P. Manuel, PhD
CO2 incubators provide the sensitive conditions required to support the integrity of growing cell cultures. The key to happy, healthy cell cultures is a well-designed, properly functioning, and most importantly, regularly maintained CO2 incubator.
If the incubator runs smoothly, researchers need not worry. One places the cells within the incubator and shuts the door. That is all there is to it. But, when the incubator has a problem, everything comes to a screeching halt. A problem- atic incubator delays everything in a cell culture lab that is
wholly dependent on the growth of cells. If the cells aren’t growing, everything down the pipeline is delayed until this issue is resolved. It is for this reason that routine mainte- nance of the incubator is a top priority. The lack of regular maintenance can easily diminish the quality of an incubator.
Luckily, a few key maintenance tasks can keep CO2 incuba- tors running smoothly.
“Disinfection and cleaning are the keys to happy cells. ”
Disinfection and Cleaning
Experts delegate two main tasks as crucial when it comes to maintaining CO2 incubators: calibration of the unit at least once each year and making sure the door is closed. Half the problems encountered with incubators are a result of the door not closing correctly. Experts also suggest that users should make sure they change the water completely at least once a week and that the unit be cleaned and disinfected regularly. Both these steps will help in preventing contamination. Researchers should take extra time in observing their cells for any signs that they are unhealthy as this could also mean that something is wrong with the incubator.
A common mistake often made by users is choosing highly pure water as opposed to sterile, distilled water. Deionized or ultrapure type 1 water can be very aggressive. This is because they contain very few ions, with the water actively pulling ions from the materials in the incubator like the stainless steel and other incubator components, which over
time, leads to pitting and corrosion. Sterile, distilled water with a pH between 7 and 9 is ideal for the operation and the longevity of an incubator.
Using bleach to clean and disinfect incubators is another mistake as it can also corrode incubator components and even worse, the fumes from the bleach can make cells sick. Experts recommend a quaternary ammonium disinfectant instead. Adding to this, users often forget to change the HEPA filters on incubators that use them. Particulates tend to remain on these filters that should be changed every
six months or so to avoid cross-contamination in between experiments. Lastly, incubator placement is also important. Users should avoid placing the incubator in a sunny window or near an A/C vent and make sure the surface the incubator rests on is kept clean to avoid contamination issues.
While this may all feel a little overwhelming, depending on the application, a service plan can help when it comes to performing regular maintenance on a lab’s incubators. This option may bring up the concern of added costs but it is a better choice in the long run when compared to dealing with bigger expenditures incurred if, for example, the unit’s sensors aren’t working properly.
Maintenance is not something that should only be con- sidered after a problem with the incubator emerges. If an incubator is not calibrated or serviced regularly, it will not provide ideal conditions for cell growth, and any related ex- perimental results will be inaccurate and unreliable. As such, choosing the right incubator for your lab provides the ideal conditions necessary for sensitive research and development, but regular maintenance of the incubator is critical for the accuracy and reliability of your experimental results.
Other Considerations
A handheld infrared (IR) CO2 tester is usually a good thing to have for incubator maintenance, though these testers must be calibrated once a year, and some of the newer incubators have IR CO2 sensors that are more accurate than handheld IR sensors.
User manuals, sales teams, application notes, and the manufacturer are all good resources to consult about incubator maintenance.
Things to look for in your cells: Do the membranes look nice and tight? Are they peeling up at all? Are there vacuoles in the cytoplasm? Do you see crystals around the nuclear membrane? All of those are signs that something’s not right with the growth conditions and you may want to check the incubator.
How to Prevent Biological Contamination in Your CO2 Incubators
Engineering and user controls help keep contamination at bay
by Andy Tay, PhD and Ajay P. Manuel, PhD
Carbon dioxide (CO2) incubators are indispensable for biolo- gy work. They provide well-regulated CO2 levels, humidity, and temperature that are ideal for cell and tissue culture.
However, these conditions that are optimal for your cells and tissues are also likely to promote the growth of contam- inating microorganisms such as fungi, bacteria, mycoplasma, and viruses.
When biological contamination happens, it can adversely affect the progress of research. For instance, some cellular systems like organoids take weeks if not months to grow, and contamination translates to a great loss of productivity. On the other hand, contamination involving mycoplasma is usu- ally not noticeable at the early stage and is not detected until experimental data show anomalies and have to be discarded. In general, contamination disrupts scientific progress, reduc- es the reliability of scientific data, and should be minimized, if not prevented.
In a 2010 report, biological contamination was found in close to nine percent of cell cultures in the biopharmaceutical industry. The statistics were even more alarming in academ- ic labs, with reportedly 80 percent of labs in Japan and 65 percent of labs in Argentina having experienced mycoplasma contamination. Due to the prevalence of biological contami- nation, a variety of control measures have been developed to keep them at bay. Here, we share some of these tips, broadly classified into engineering and user controls.
In general, contamination disrupts scientific progress, reduces the reliability of scientific data, and should be min- imized, if not prevented.
Engineering controls
To minimize biological contamination, manufacturers have introduced several engineering solutions.
All incubators can be equipped with high-efficiency particulate air (HEPA) filters, on the interior or exterior.
) These filters can remove particles from outside air with diameters larger than 0.3 μm with more than 99.95 percent efficiency before flowing the filtered air into the incubators.
“In general, contamination disrupts scientific progress, reduces the reliability of scientific data, and should be minimized, if not prevented.”
) Because mycoplasma is between 0.1-0.3 μm, HEPA filters cannot filter them, and thus other engineering controls are needed.
) HEPA filters should be replaced every six months as they can be clogged with large particles which reduc- es their filtering efficacy.
Many incubators are now equipped with automated heat decontamination and sterilization functions which provide cleaning with the use of heat and steam.
) Annual inspections are recommended to ensure that this function is well-maintained.
) Older designs of incubators typically do not come with an automated sterilization system—thus, routine manual cleaning should be performed weekly.
Various ingenious designs have been incorporated into incubators to minimize biological contamination and users should try to make use of them.
) With the incorporation of rounded corners, users can easily identify and clean spills. Copper is also the ma- terial of choice for incubators, including the racks and water pan, due to its antimicrobial properties.
) Some incubators even come with ultraviolet (UV) ster- ilization. Typically, 15-30 minutes of UV treatment will be sufficient for decontamination, but users should take note that this works only on surfaces that are in contact with UV rays, and cells should be removed from the incubators before UV sterilization.
User controls
Researchers are home to a rich ecosystem of microorganisms and are the most likely source of contamination. By following good practices, however, researchers can greatly minimize the risk of introducing biological contaminants into incubators.
Incubators should be placed as far away from sources of contamination as possible.
) Above the ground so that microorganisms near the floor and on the shoes of users do not enter the incu- bator during opening and closing.
) Away from areas in the lab with high human traffic as the moving air may unintentionally introduce contaminants.
) Away from direct sunlight helps to avoid temperature-in- duced condensation within the incubators that microor- ganisms can exploit to grow.
Laboratory personnel should practice good protocols when working with incubators.
) Never touch the interior of an incubator with unster- ilized gloves or loose sleeves or speak into an incu- bator. Any items being placed inside the incubators should be sterilized with 70 percent ethanol and wiped down thoroughly.
) Keep the door opening frequency to a minimum—be- fore opening an incubator, users should spray the side of the door and their gloves with 70 percent ethanol to sterilize surfaces that may be contaminated with microorganisms.
) Users should also be careful not to overfill an incuba- tor with too many cell culture flasks and well plates as this can disrupt proper airflow and temperature uniformity. When temperature difference happens, condensation may occur within incubators, causing microorganisms to thrive.
Incubators should be cleaned weekly, as this helps to remove potential contaminants early before they become more serious.
) To clean the interior of the incubator effectively, items in the incubator should first be relocated to another
incubator, free from contaminants. Then, with the use of two percent quaternary ammonium disinfectant followed by 70 percent ethanol, the incubator can be properly decontaminated.
) Manufacturers discourage the use of bleach as a disinfectant as it can corrode the metals of incubators. The decontamination process is complete after turning on the heating to dry the interior of the incubator.
) During cleaning, the water in the pan that helps to maintain incubator humidity should also be changed, and only sterile, distilled water should be used. Tap water should be avoided as it often contains bacteria, and deionized water should be avoided as well as it can corrode the metal pans. Generally, chemicals such as quaternary ammonium disinfectant are also added to the water pan to prevent the growth of microorganisms.
CO2 incubators have greatly transformed the way we per- form biological experiments. By providing a well-regulated environment, they facilitate optimal cell and tissue growth and are a staple in many biology labs. There are multiple sources of biological contamination including the lab envi- ronment (air and ground) and users, but with effective engi- neering and user controls, it is possible to keep contaminants at bay to generate reliable and reproducible scientific data.
Product Spotlight
NU-5841 CO2 Incubator
provides laboratories that need to control both a broad range of chamber conditions and the constant risk of contamination with a holistic set of capabilities. This model offers control and mon- itoring of temperature, CO2, O2, and relative humidity levels to meet the demands of various cell culture applications. This design uses an infrared sensor for precise control of CO2, injects N2 to create hypoxic conditions, and routes chamber air through a humidity reservoir when its RH sensor senses moisture is necessary. The air pump constantly draws air through a HEPA filter and cycles
it back to create clean air inside the chamber on an ongoing basis, while a heated decontami- nation cycle can be used as necessary. A touch screen makes it easy to enter set points or view historical performance.
Comparing Cooling Technology in Refrigerated Incubators
Traditional compressors vs thermoelectric cooling in refrigerated incubators
by Andy Tay, PhD
When we think of incubators, the first image that pops to mind is usually an incubator maintained between 30°C and 37°C for bacterial and mammalian cell culture. However, there are
also refrigerated incubators that can maintain a wider tempera- ture range (between 5°C and 70°C) with greater precision for applications such as temperature-dependent growth of microor- ganisms, quality testing of food products, and temperature-con- trolled storage and transport. In this article, we will discuss the different cooling mechanisms and what factors to consider when selecting refrigerated incubators for your lab.
Vapor compressors vs Peltier cooling There are two main cooling mechanisms for refrigerated incubators. The conventional type is vapor compressor technology, which uses a circulating liquid refrigerant
to cool the incubator. Circulating refrigerant first passes through the compressor where it is compressed to a higher temperature and pressure. The hot, compressed vapor then passes through a condenser where it is cooled by air or water, condensing into liquid refrigerant. The liquid refrigerant next flows into the thermal expansion valve where it experiences an
abrupt pressure drop, and thus temperature, making it colder than the temperature of the enclosed space to be refrigerated. Finally, the cold liquid refrigerant is circulated into the evaporator, where it absorbs heat from warm air and cools the enclosed space in the refrigerator to the desired temperature.
Alternatively, Peltier cooling utilizes the thermoelectric effect to create heated and cooled sides in a device and does not re- quire liquid refrigerant. Refrigerated incubators that operate by the Peltier effect make use of semiconductors to achieve cooling. When direct current is applied to the device, it flows through two different types of semiconductors in the Peltier module, causing the heat sink on one side to warm, and the other side to cool, which cools the circulating air and refrigerated space.
Key parameters to consider
Peltier cooling technology does not contain moving parts, which circumvents problems of mechanical wear and tear and reduces the probability of system failure. In general, it also extends the life of the refrigerated incubator and reduces ongoing maintenance costs compared to vapor compression
CO2 Incubator Care: Best Practices
How to make a happy home for your cell and tissue culture
CO2 incubators are designed to replicate in vivo conditions for optimal growth of cells and tissues. The device controls the levels of carbon dioxide, humidity, and temperature in a contamination-free environment. Cells and tissues are highly sensitive to changes in their environment, so it is important to keep your CO2 incubator functioning properly.
technology. The typical reasons for a vapor compressor failing
are fouling such as algae growth, lubrication problems, and overheating that can reduce energy efficiency and disrupt the cooling system. Although the Peltier cooling method can also fail due to overheating, generally it is more reliable. The industrial standard for mean time between failures for a Peltier module is 200,000 hours.
Materials used in Peltier cooling technology are flexible and can be used to create refrigerated incubators that occupy less space and make the cooling of small, enclosed areas more targeted.
Additionally, with the use of direct current to generate heat flow, Peltier-cooled incubators offer better temperature control, as the direction and amount of electric current can be more precisely tuned. This is particularly important in applications such as mon- itoring the growth of microorganisms for safe product storage as well as the transport of temperature-sensitive biological materials.
CO
2
incubators are designed to replicate in vivo conditions for optimal growth of cells and tissues. The device controls the levels of carbon
dioxide, humidity, and temperature in a contamination-free environment. Cells and tissues are highly sensitive to changes in their environment,
so it is important to keep your CO
2
incubator functioning properly.
Avoid
Contamination
Always wear gloves when using
the incubator and keep the inner
glass door closed as much as
possible. Change the water in the
humidity pan weekly; regularly
clean the pan, shelves, chamber,
and any passages into the
incubator; and occasionally wipe
down the door handle.
Maintain Optimal
Temperature
CO incubators are typically
2
maintained at 37°C. Attach
a calibrated thermometer to
the inside of the glass door to
enable temperature readings
from the outside when the door
is closed. Check periodically that
the temperature sensor matches
the thermometer reading, and
recalibrate the sensor if the
readings differ.
Monitor
CO
Keep
Humidity High
If the humidity inside of the
incubator falls too low, the
cell culture can evaporate or
growth media can become too
concentrated. To keep humidity
around 95%, make sure that there
is always water in the tray under
the incubator.
2
The CO
2
concentration should
be kept around 5% to match
physiological conditions and
to maintain a constant pH.
While most CO
2
incubators are
equipped with a CO
2
sensor, an
external gas analyzer will help to
ensure the readings are accurate.
In summary, both vapor compression and Peltier cooling technology offer different advantages. Users should take into consideration these main parameters—energy efficiency, main- tenance, physical footprint, temperature control, and environ- mental-friendliness—when selecting refrigerated incubators.
CO2 Incubators: Precision Tools Driving Drug Discovery Success
A concise guide to critical CO2 incubator conditions, effective monitoring techniques, and preparing for scale-up
by Jordan Willis, BSc
CO2 incubators are essential for cultivating cells or tissues under controlled conditions in drug discovery labs. This article explores the significance of CO2 incubators with an emphasis on the importance of rigorously maintain- ing and monitoring incubation conditions. Effective cell culturing techniques require precise, real-time control of numerous environmental metrics. Maintaining sterility is also paramount to prevent contamination and downtime.
Drug Discovery—Maintaining culture conditions
Carbon dioxide (CO2) concentration: Commonly used at five percent CO2 but may vary based upon culture medium pH buffering system1
Oxygen (O2) concentration: Can vary from 1-20 percent depending on cell- or tissue-specific conditions like hypoxia or hyperoxia1
Temperature: Maintained at approximately 37 degrees Celsius (98.6 degrees Fahrenheit)1
pH level: A slightly acidic pH of 7.2-7.4 is typically used to emulate bloodstream biochemistry but may vary when studying health conditions such as cancer1
Osmolarity: osmotic stress is prevented by adjusting cell culture osmolarity in a cell- or tissue-specific manner (typically 260–320 milliosmole)1
Humidity: Maintained at 85-95 percent to prevent evaporation and maintain osmolarity of cell culture media2
Gas flow and distribution: Even dispersal of CO2 and O2 levels must be maintained throughout the incubator to prevent localized variation across cultures1
Sterility: Typically maintained via HEPA filter and UV decontamination methods in combination with aseptic techniques and regular cleaning1
From environmental stability monitoring to regular quality checks, there are practical strategies that can be implemented to ensure the reliability of cell cultures. Understanding and maintaining these conditions are key
factors in building the foundation for drug discovery pipe- line success.
Defining the importance of CO2 incubation conditions
Several primary environmental parameters require stringent monitoring and control during cell culture incubation to ensure cell viability, proliferation, and an accurate representation of
in vivo conditions. Deviations from these parameters (within or between incubators) can result in noisy, inconclusive data or even cell death. Furthermore, cell culturing conditions can
vary per experiment and cell type, so it is important to be well- informed about the requirements of the cells in your care.
Effective incubator and cell culture monitoring solutions
Success in a drug discovery pipeline lab requires a combination of tools and software for monitoring and controlling cell culture conditions. A holistic approach to monitoring both the environment and the cell cultures is fundamental to guarantee precision, reproducibility, and data integrity.
Incubators with integrated sensors, controls, and data logging
Most modern CO2 incubators come equipped with controls for temperature, humidity, and gas concentrations. Gas sensors are crucial for continuous monitoring of atmospheric conditions. Osmometers and pH meters may also be integrated to validate the osmolarity and pH levels of the culture media. These features allow real-time monitoring and adjustment of the incubation environment as needed.
Some advanced models also offer data logging capabilities that record the important metrics over time, which supports data reproducibility and validation. This is especially important for experiments or trials with a long duration.
Environmental monitoring systems (EMS) and software
An EMS integrates multiple sensors to monitor key parameters such as gas concentrations, relative humidity, and temperature. These systems provide a centralized platform for real-time data collection. They can be configured to provide alarms when triggered by changes in the culturing environment. Additionally, laboratory information management system (LIMS) software can be integrated into the EMS to manage and track experimental data, including cell culture conditions and experimental results. Incubators may also be equipped with automated culturing systems using control software that communicates with equipment, like robotic arms and liquid handlers. This software reduces human error and ensures proper coordination of experiments during high-throughput screenings. Together, these three systems can improve reproducibility, data organization, traceability, and demonstrate adherence to regulatory standards and guidelines.
Cell culture monitoring methods
CO2 incubators can be equipped with inverted microscopes that enable digital imaging capabilities for monitoring cell morphology, density, and behavior in real time. Alternately, instead of adding an inverted microscope to your incubator, some companies have developed small incubation chambers
that are staged directly upon the inverted microscope. This method facilitates the use of automated live-cell imaging systems that can capture time-lapse images or gather data for long-term experiments. Aside from cell visualization, contamination must also be monitored. The most likely incubator infection is caused by mycoplasma due to their small size (0.1-0.3 microns) and ability to slip through the incubator’s HEPA filtration systems. Currently, PCR is the most used method for detecting mycoplasma and specialized kits exist for this purpose.
Are you ready to scale up?
The process of scaling up from small-scale cell culture to bioreactors can be daunting. To reduce stress upon yourself and your cell lines, some preliminary quality control work must be done. First, prepare a blueprint of expected results by optimizing your culturing conditions and ensuring that your experimental data is rigorously gathered and well- reviewed. Next, authenticate your cell lines via DNA and karyotype profiling, determine cell viability and purity, and test for contaminating organisms like mycoplasma. Ensure that the monitoring methods you’ve established on a small scale will be feasible and available in the bioreactors. Enter the process with specific expectations about metrics like expected cell density and growth rates, product quality or consistency, and devise methods for ensuring comparability with your small-scale results.
In drug discovery labs, CO2 incubators are indispensable tools used in the meticulous process of controlled cell or tis- sue cultivation. The emphasis on rigorous maintenance and monitoring of incubation conditions can’t be overstated as they are crucial for the reliability and reproducibility of ex- periments. Establishing reliable conditions is required before scaling up production in bioreactors. With an unshakeable commitment to quality control, CO2 incubators can serve as the basis for groundbreaking experiments and the develop- ment of novel pharmaceuticals.
References
Bal-Price, Anna, and Sandra Coecke. 2011. “Cell Culture Techniques.” Neuromethods, 1–25. doi:10.1007/978-
1-61779-077-5_1.
Pamies, David, Marcel Leist, Sandra Coecke, Gerard Bowe, David G Allen, Gerhard Gstraunthaler, Anna
Bal-Price, et al. 2021. “Guidance Document on Good Cell and Tissue Culture Practice 2.0 (GCCP 2.0).” ALTEX 39:
30–70. doi:10.14573/altex.2111011.
At NuAire, we manufacture quality lab products with your specific application and long-term success in mind. We are a leading provider of biosafety cabinets, laminar airflow workbenches, CO2 incubators, animal handling equipment, and even customized containment solutions for scientific laboratories. You choose the configuration that matches your workflow, and we’ll build a long-lasting product that’s designed to meet your needs at a low cost of ownership for years to come. A half-cen- tury of expertise and a personalized approach make NuAire the safer choice for your laboratory.
In partnership with